Production Cycle
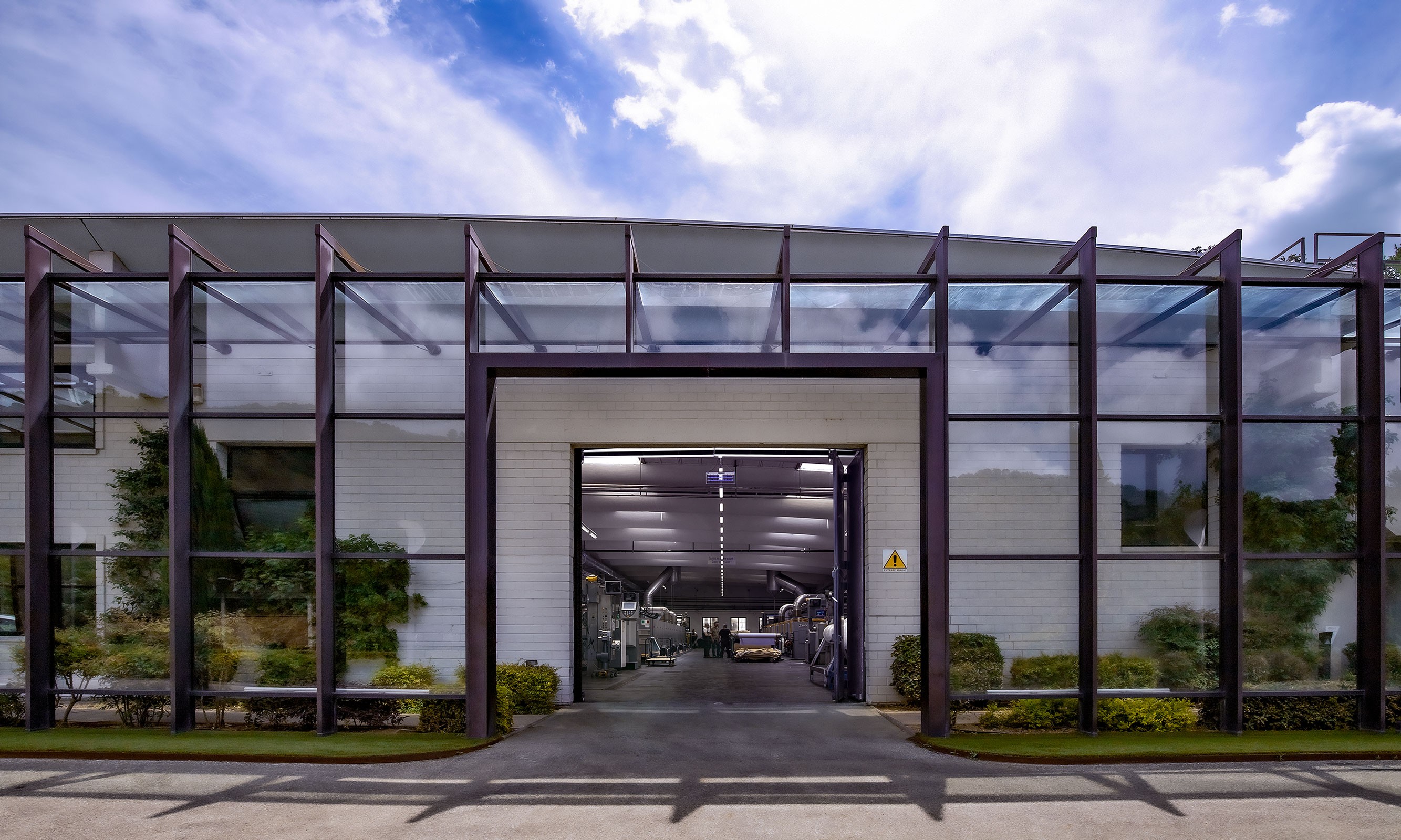
Ours is a vertical factory. Raw materials enter and exit as finished garments, going through each step of the production.
Machinery + Technology + Research + Human excellence = Beste
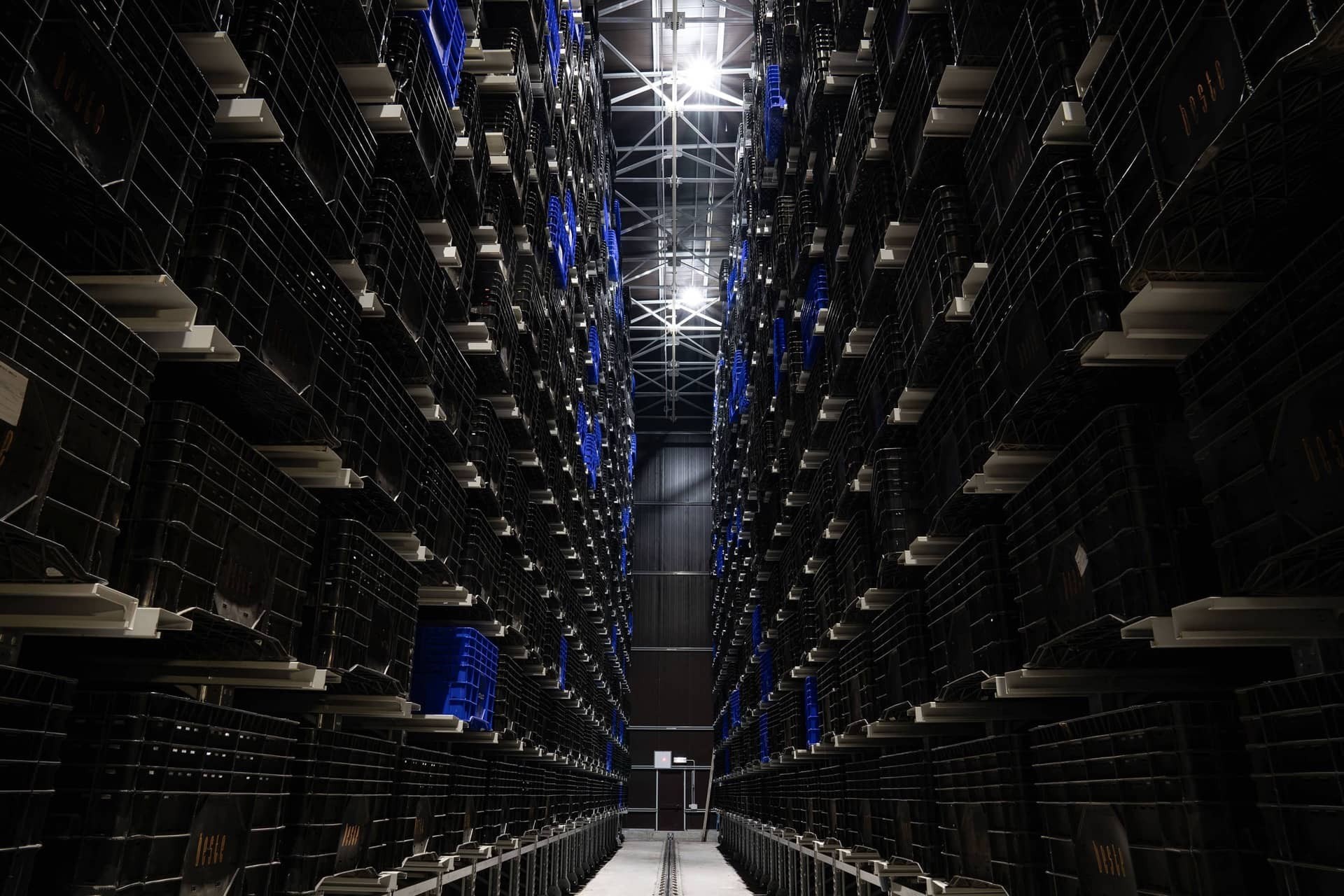
Robotized Yarn Warehouse
The yarn, both greige and dyed, is automatically stored through the use of a remote-controlled robot.
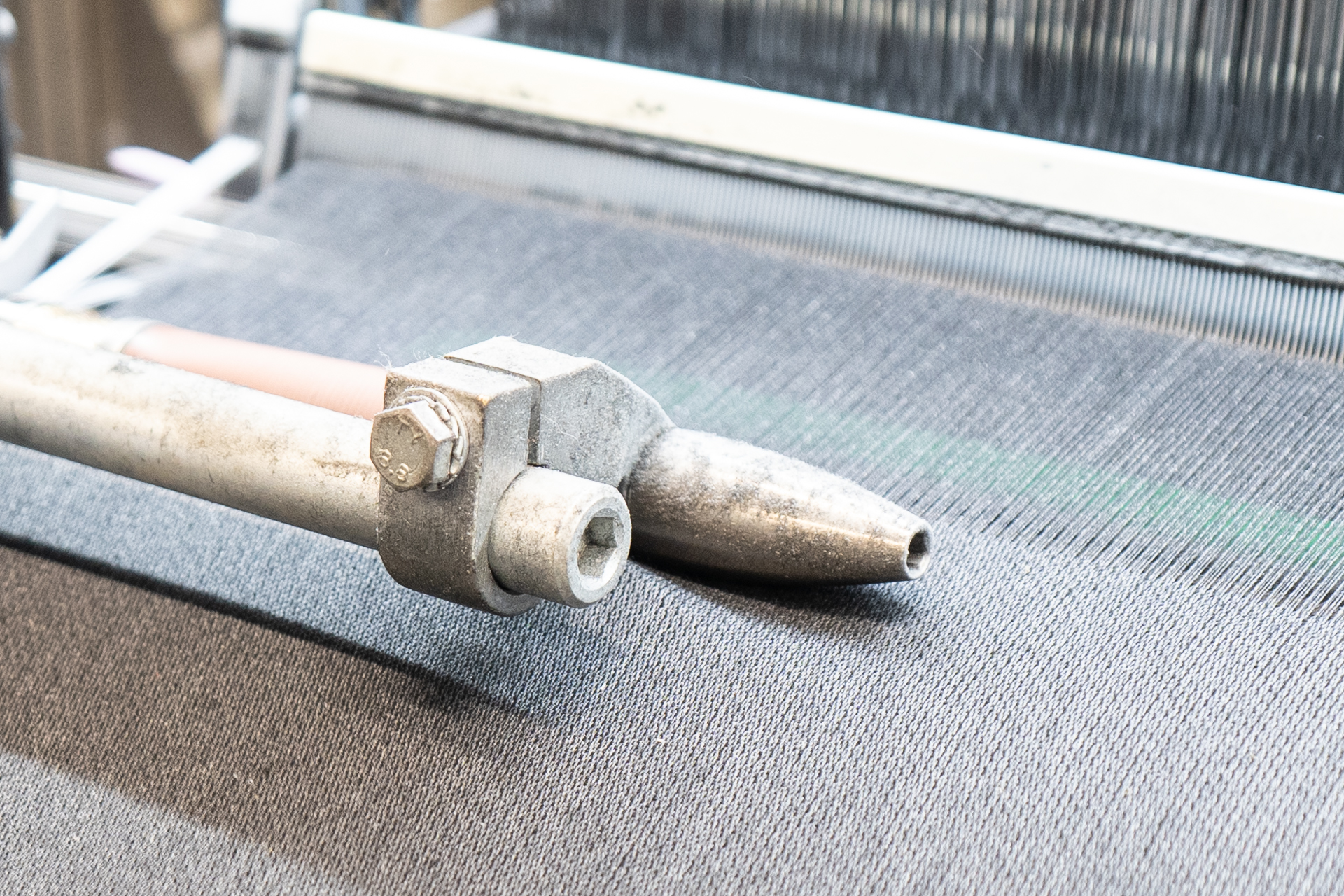
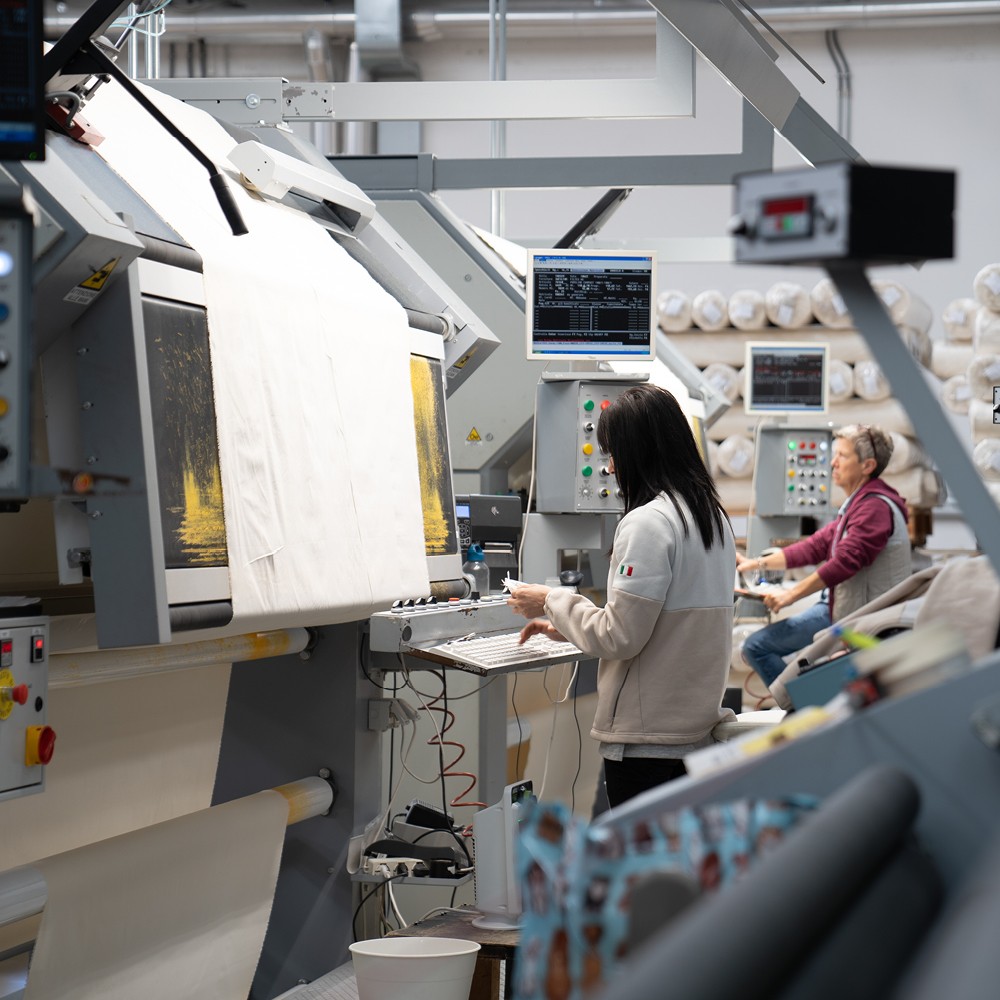
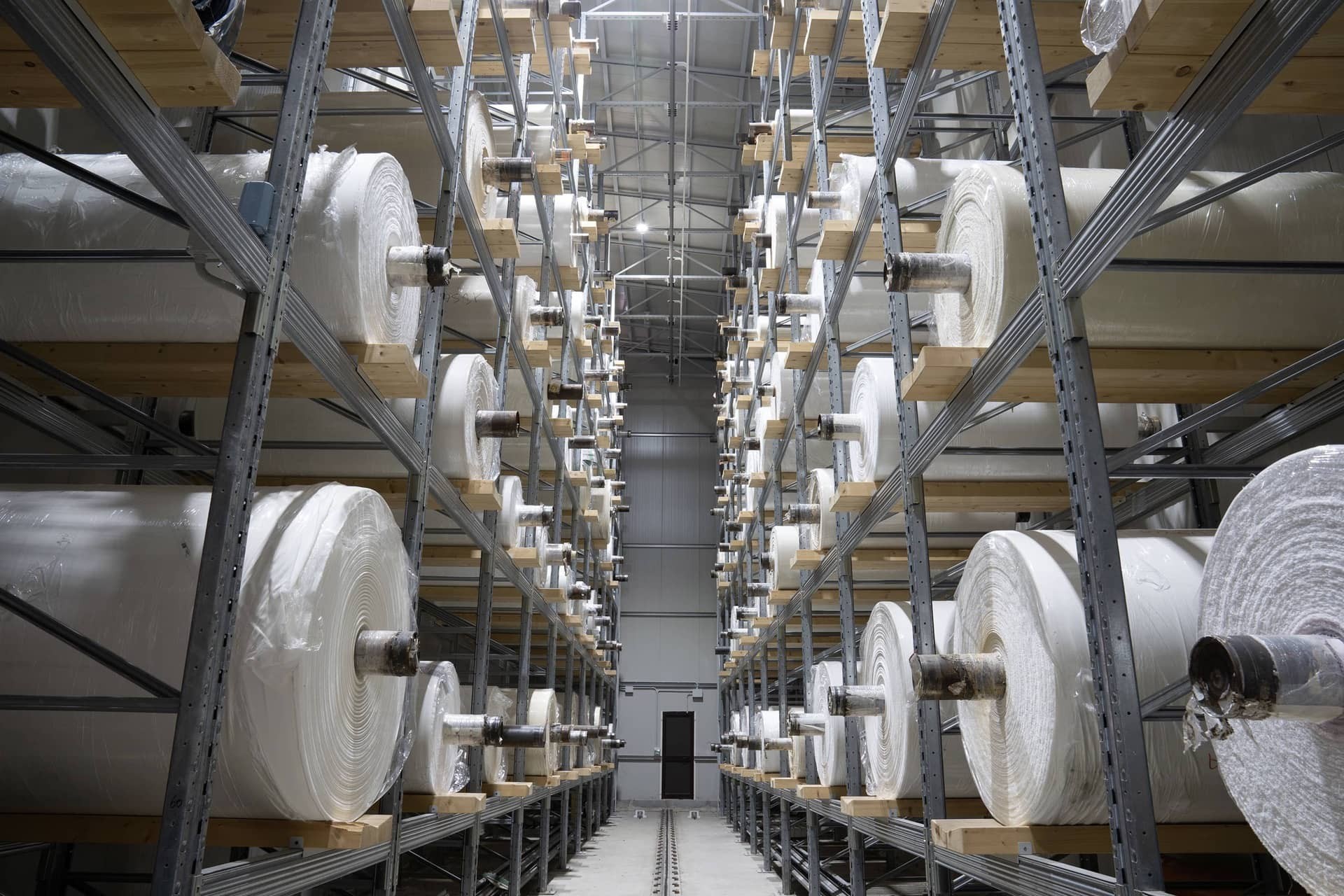
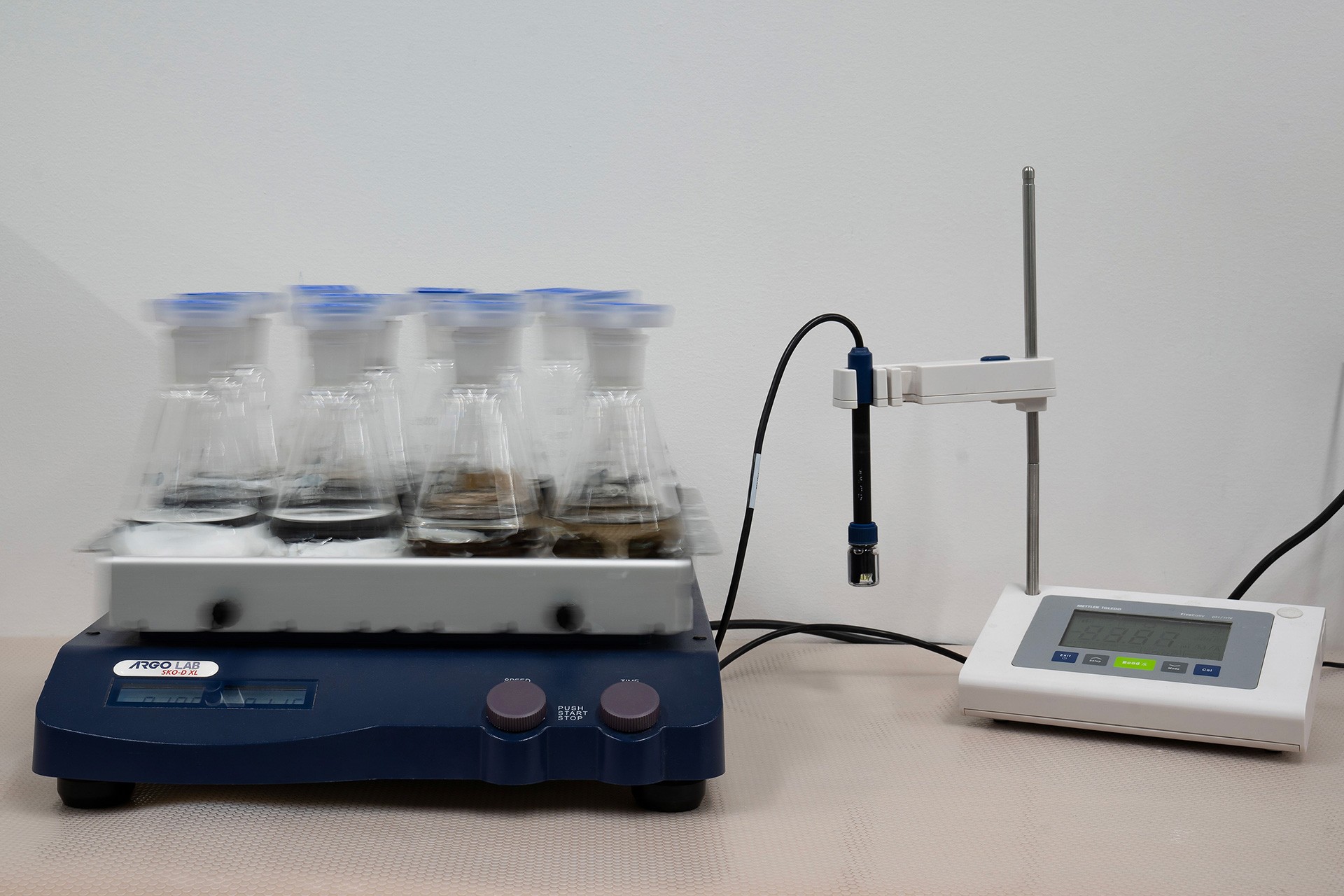
PH-meter
We determine the pH-meter (index of acidity, basicity or neutrality of the environment) in order to judge the skin compatibility of the fabric, namely the result we can feel when it comes into contact with our skin so as to avoid causing allergic and/or inflammatory reactions. The alterations on the pH watery extract values are due to the textile material processing cycle and for this reason it has to be controlled by employing the pH-meter, an instrument made up of a probe (electrodes) which is linked to an electronic device that gathers the signal, computes the pH respective value and shows it on a display.
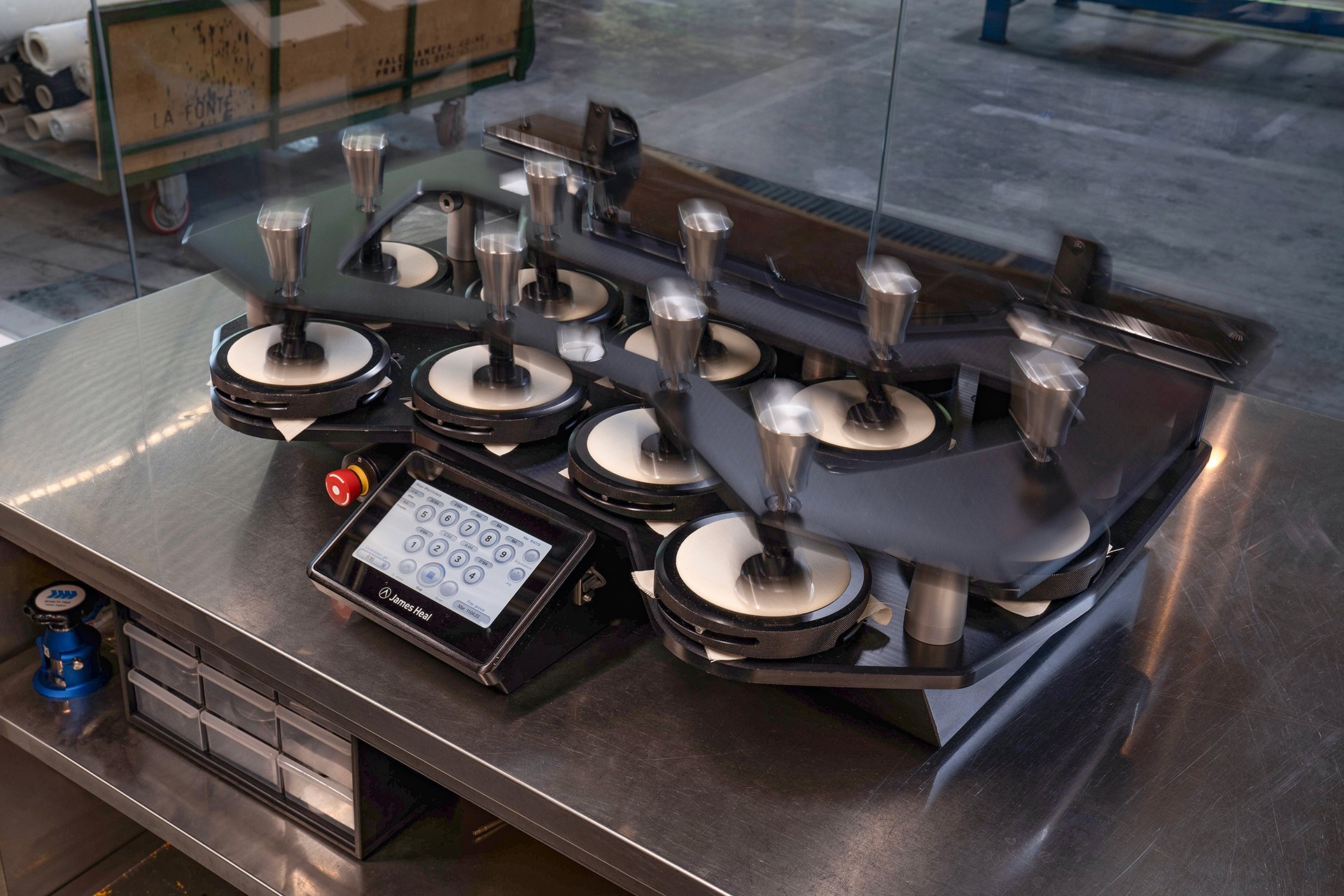
Martindale
The Martindale is used for analysing fabrics and leather (natural or synthetic) resistance to wear. In particular, it analyses: the resistance to fabric breakage (abrasion), the pilling formation, eventual colour change and the fabric weight loss.
This test has to be conducted on at least three samples of material at the same time that, in contact with an abrasive material (or with a sample of the same material), undergo some automatic rubbing cycles at a certain pressure. According to the fabric sampling we get, results will determine the number of cycles reported. The abrasion test ends when we witness the rupture of two non-consecutive threads related to the fabric weave. Whereas the pilling test ends with the formation on surface of some abraded material balls.
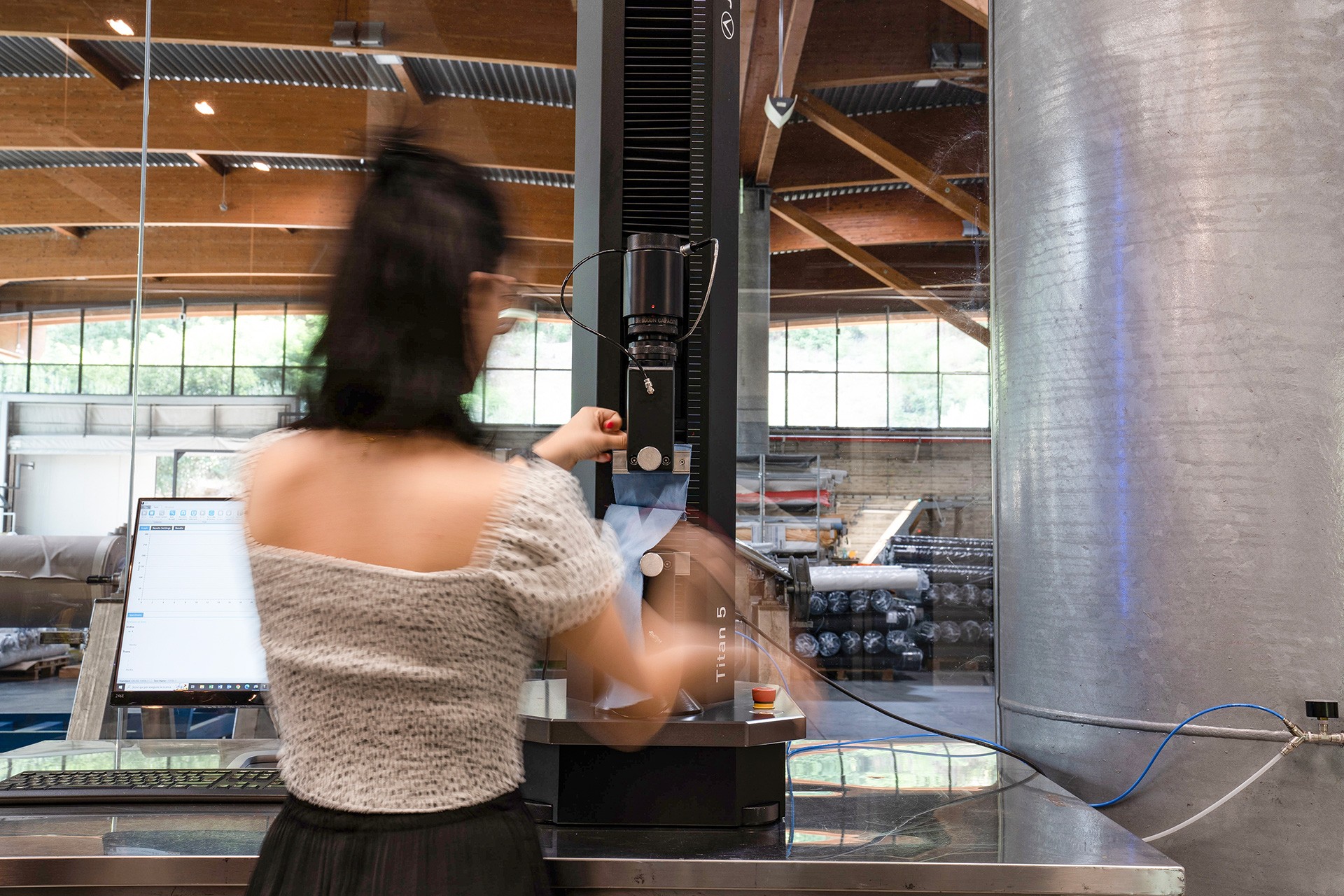
Dynamometer
The Dynamometer is an instrument used to determine the entity of textile strength. In our laboratory, the dynamometer allows us to measure the needed strength to break or lacerate a fabric, open a stitching, consider the ability an elastic fabric has to return to its original shape or split some bonded fabrics into layers.
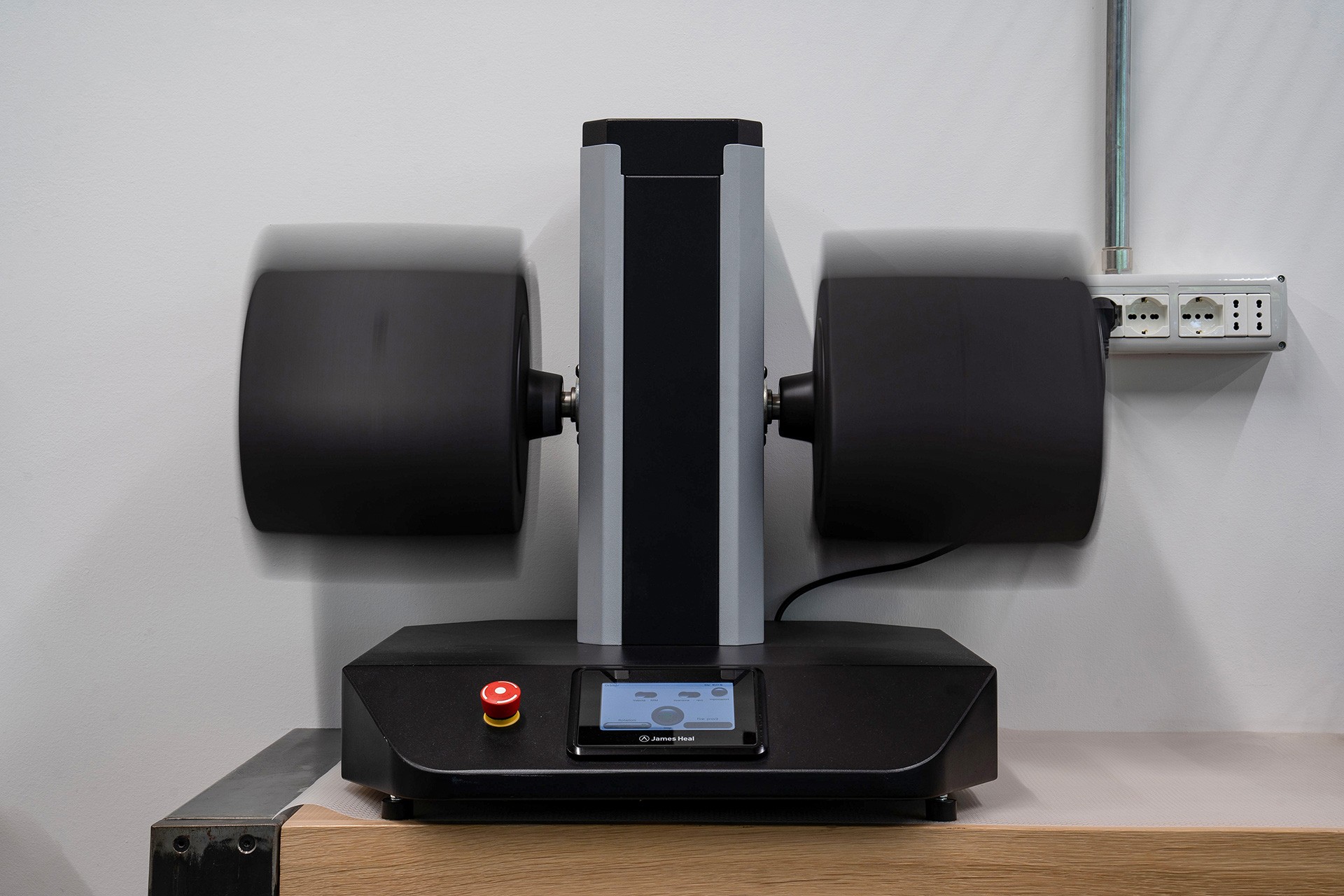
Pilling Box
The Pilling Box is employed to consider the pilling performance of knitted products, woollen, etc. The phial containing the sample is placed into the pilling box, an instrument that, when engaged, flips the sample over and rubs it into the body of the box. Once the cycles end, an operator evaluates the sample.
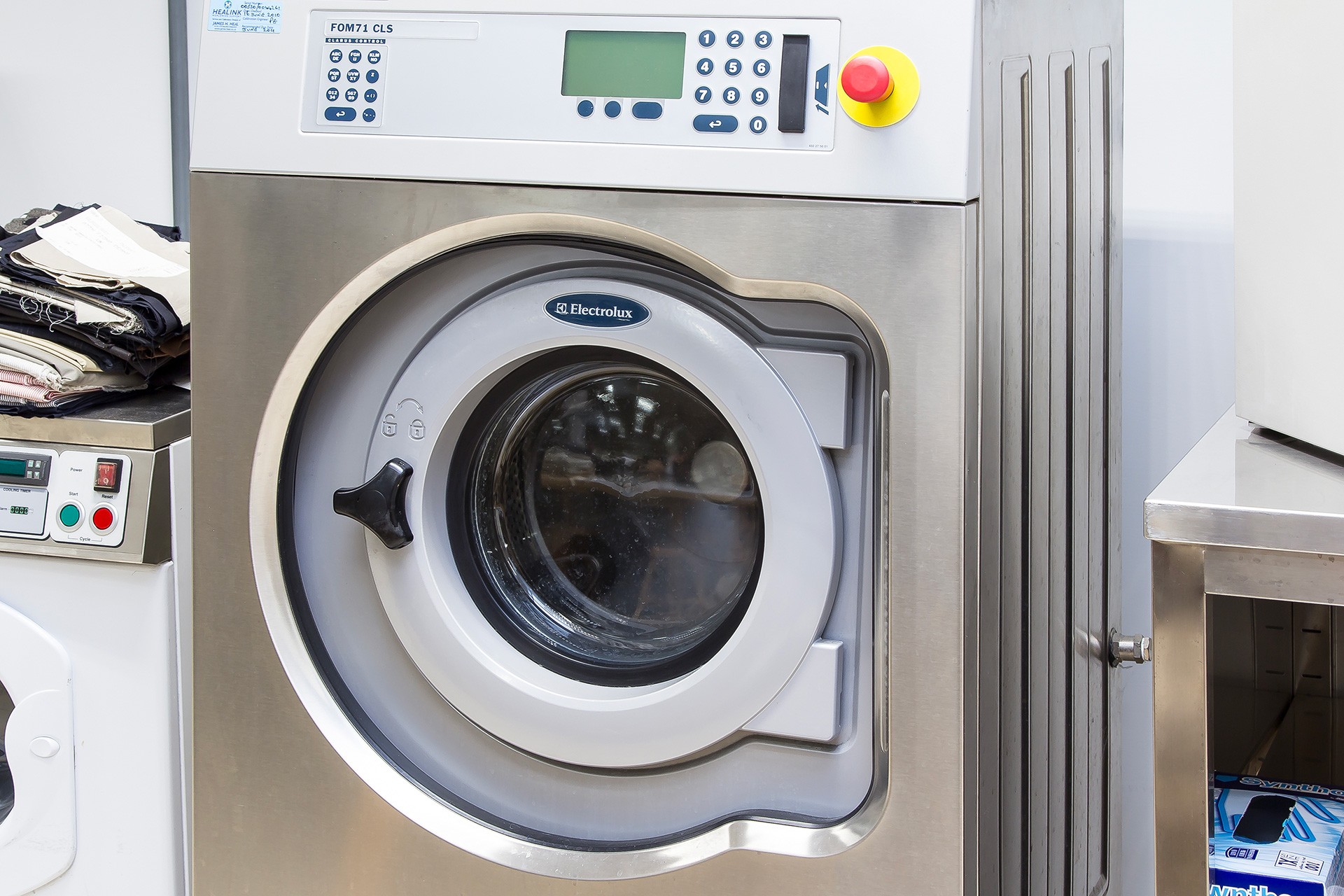
Wascator
Wascator is a standardised European washing machine for textile laboratories, used for determining the shrinkage, dimensional stability, and the after washing appearance of some fabric samples. It is actually able to reproduce all the household washes, so it is fundamental to determine the shrinkage of the fabric when undergoing a wash.
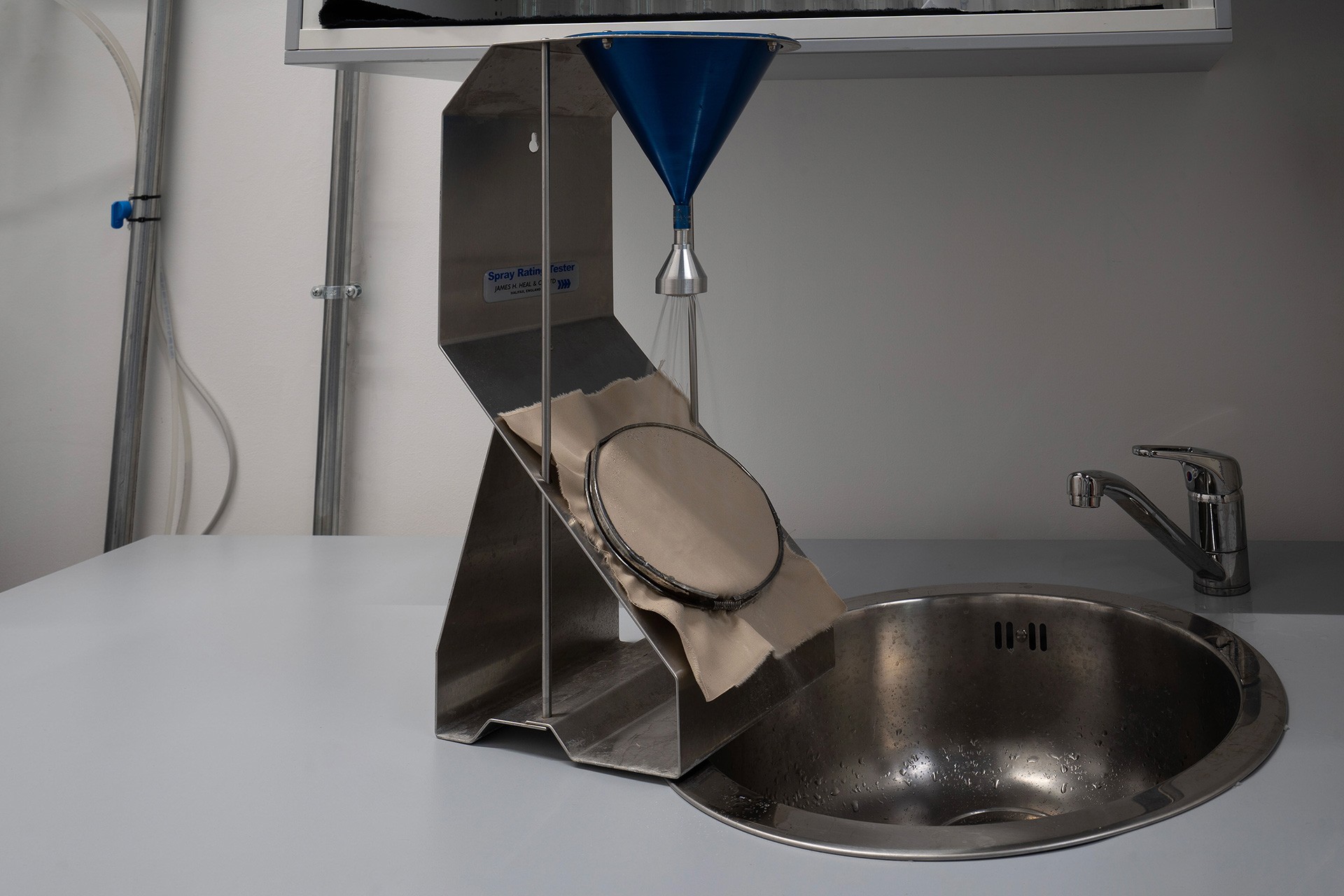
Spray Tester
The “Spray Test” is employed to carry out some watery repellent tests on fabrics or leather by using the spray method. This instrument permits us to determine the aptitude of a fabric or leather to absorb water (precipitation) it comes in contact with. The exact definition we have for this testing method is “wetting endurance”. It determines the index related to the “wettability” that comes from the comparison between the phial aspect and the one concerning all the descriptive and photographic samples given by the referenced standard. We visibly evaluate the “wetting index” according to descriptive (ISO) and photographic (AATCC) scales.
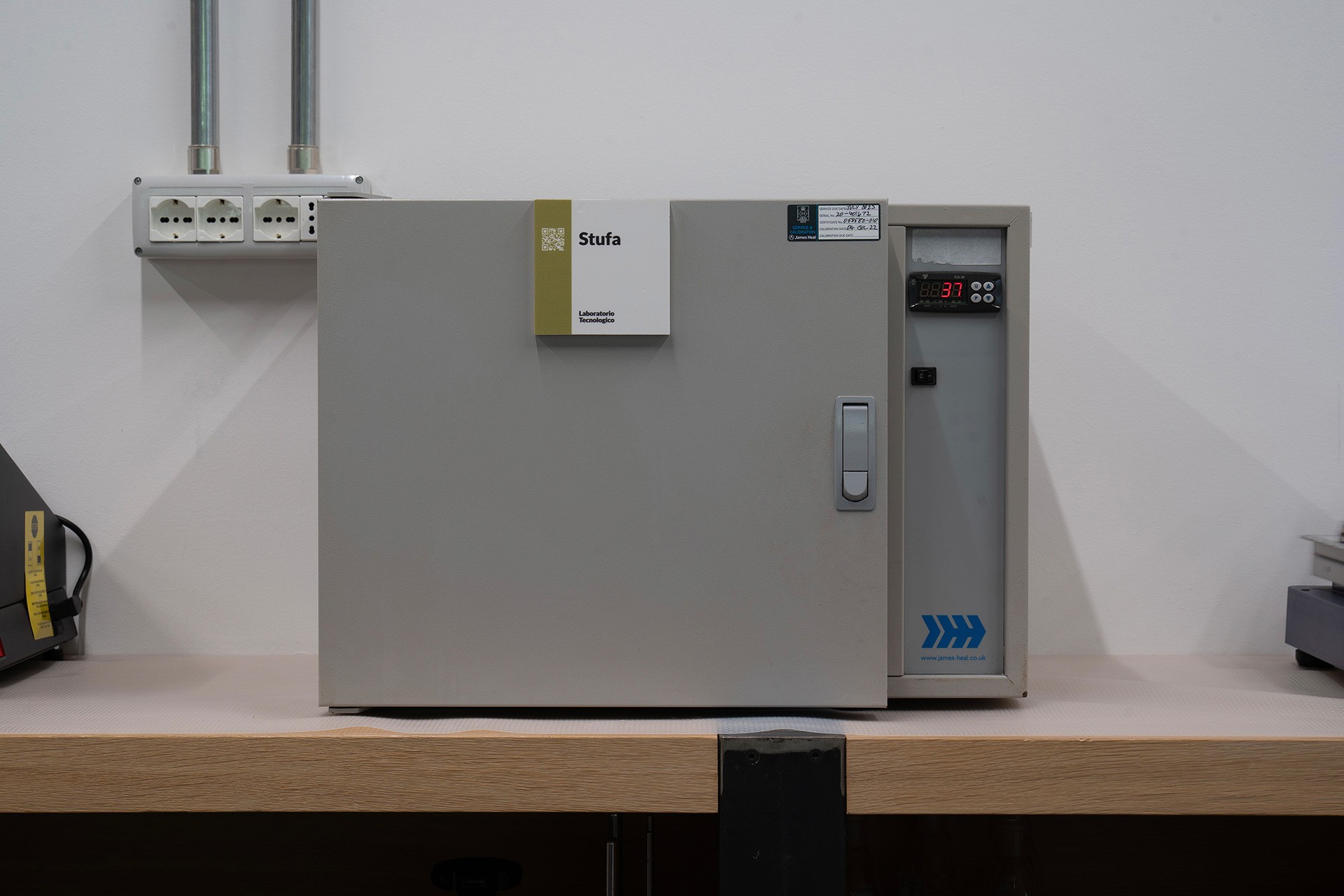
Stove
Thanks to this instrument, we can do all those tests related to color fastness to water, alkaline sweat, acid sweat and saliva. For these types of tests, some specific solutions are prepared with the aim of reproducing the required alteration agents, with the employment of chemical powder products. The samples come into touch with a multi-fibre fabric and they are later plunged in the solution for approximately 30 minutes and then left drying in a stove at 36 degrees for approximately 4 hours. Once dried, we evaluate the washing discharge intensity on the fibres and the dye degradation.
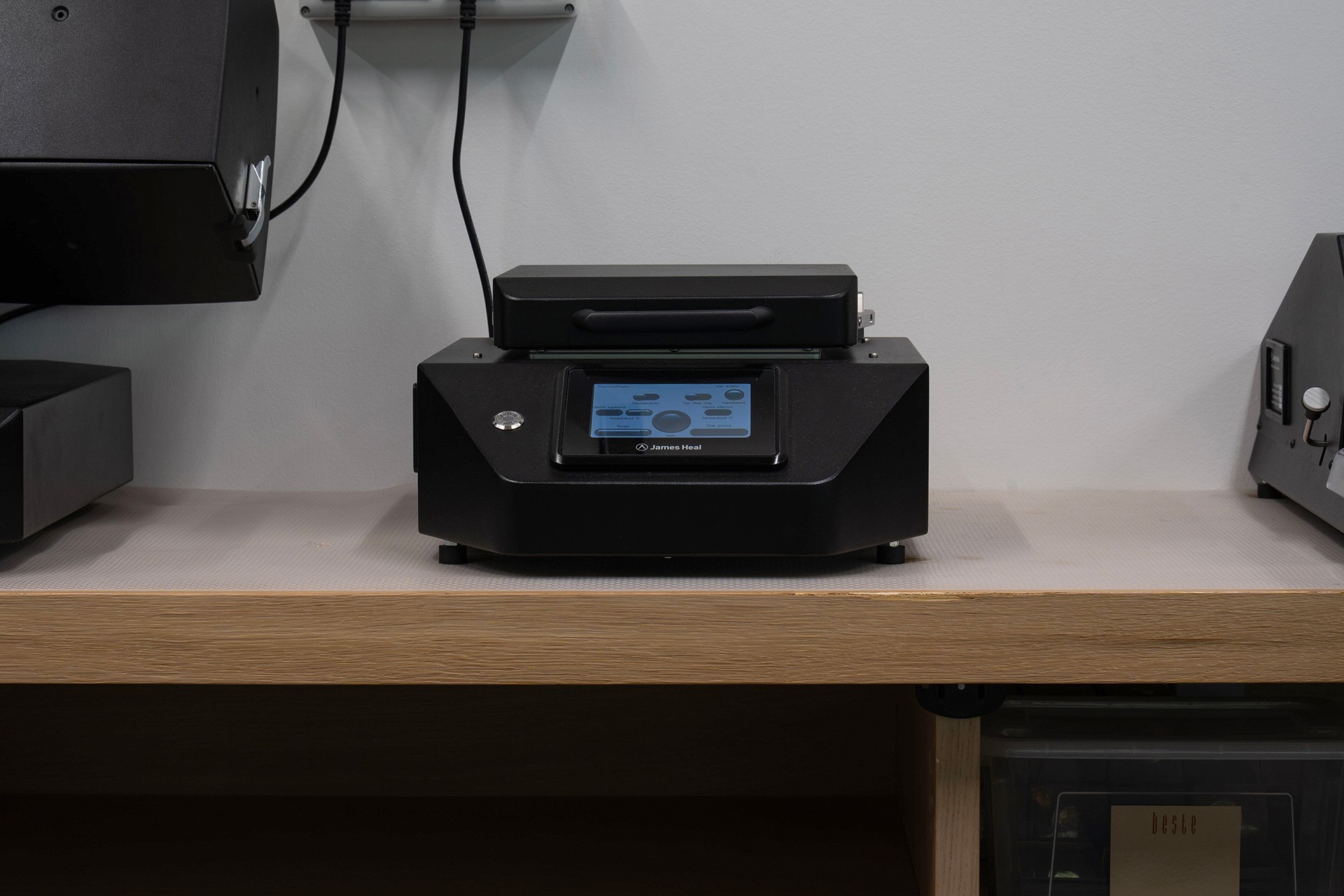
Scorch Test
The ironing fastness evaluates fabrics fading degree during the ironing phase and the eventual colour migration over a white sample of fabric, both in moisture and dry conditions.
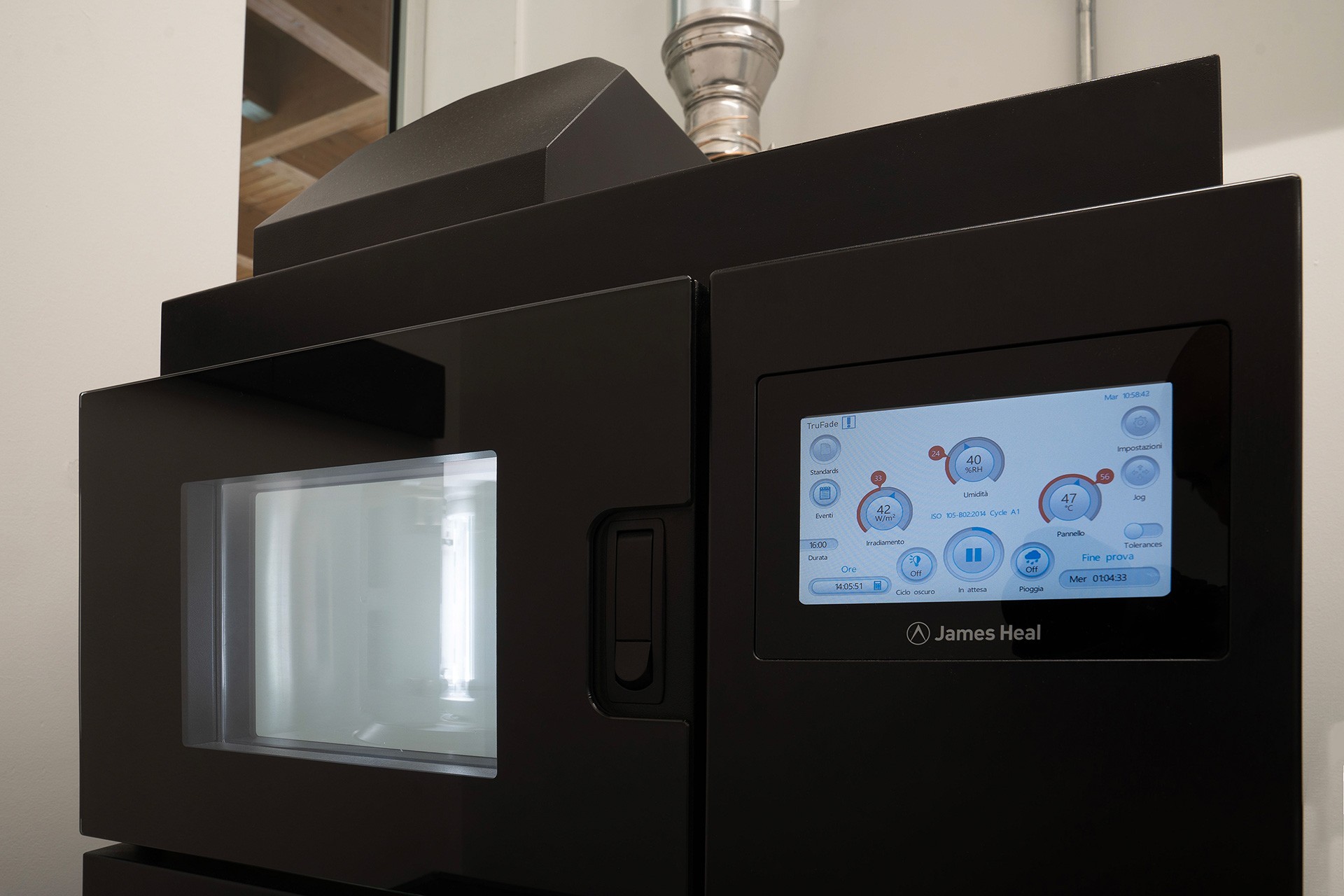
Trufade
The light fastness refers to coloured fabrics fading degree that is due to the sunlight. In this case, an artificial light is employed to simulate Sun’s properties, by accelerating the exposition process to observe and judge all the related effects in the long-term period: during this process, a lighting source with a spectral composition similar to the Sun’s one is chosen and magnified for a more compressed and accurate test. The results of this test are evaluated on a blue fades scale with an index oscillating within values from 8 (the best result) to 1 (the worst one).
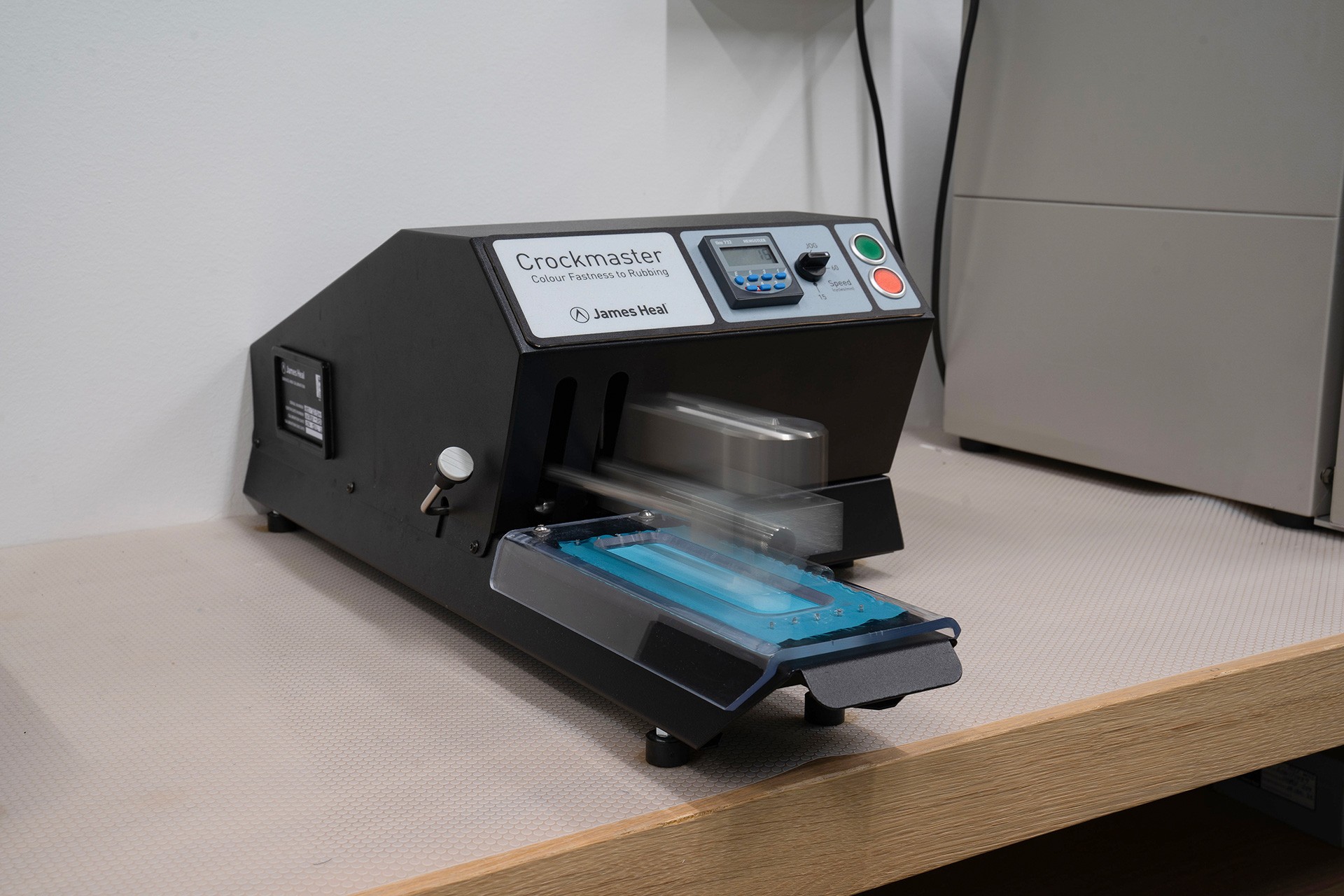
Crockmeter
Through this tool, the colour fastness to rubbing is assessed. It consists of a very simple test aimed at proving the degree of the dye fading fabrics: we rub a white cotton sample on the fabric, firstly in dry conditions and later in humid ones (specifically after having plunged the cotton sample into the water). The colour fastness is then evaluated according to the staining degree of the white fabric: the more the fabric is stained, the worse the result will be, that occurs because the dye index is not suitably set, due to an error during the finishing phase.
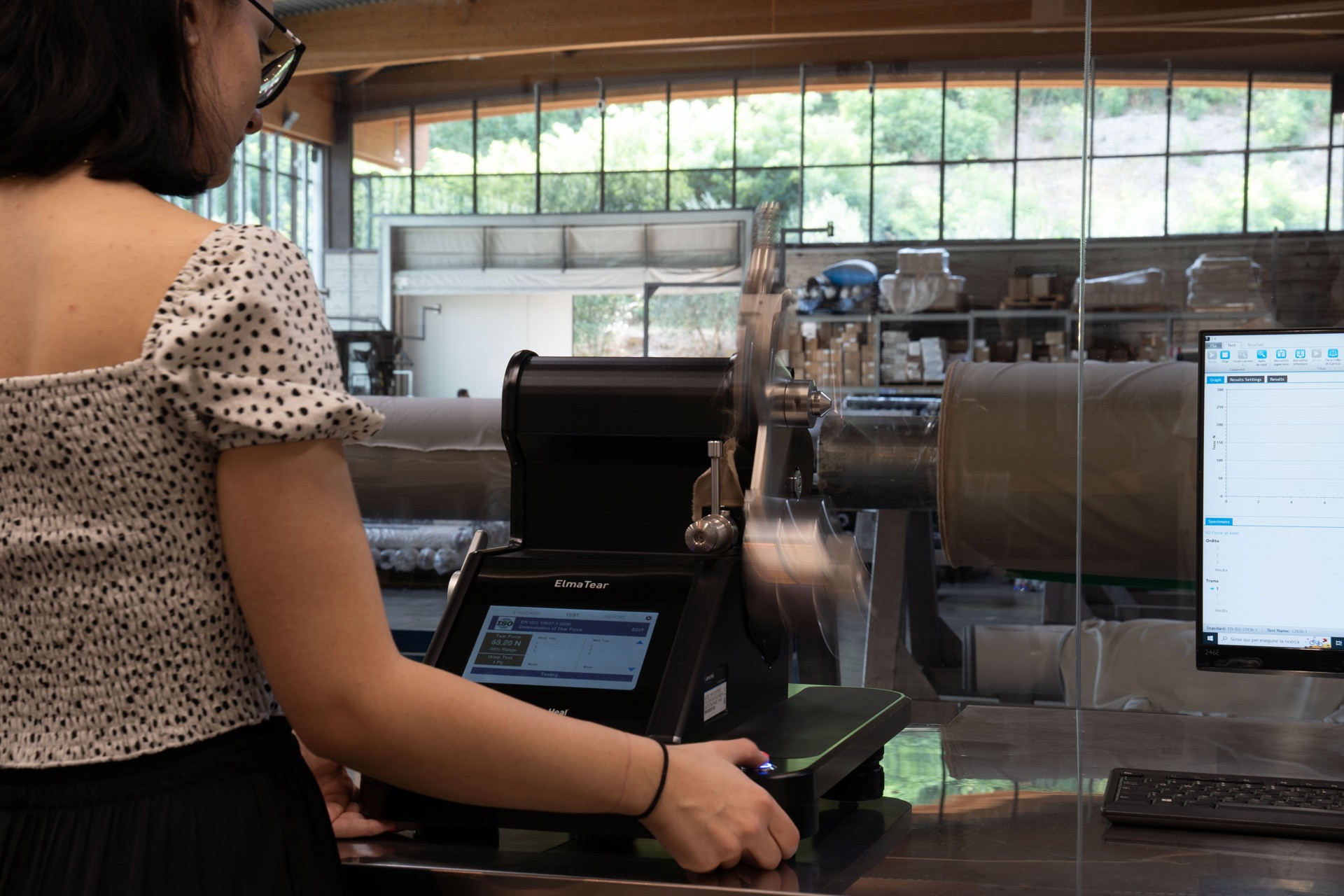
Lacerometer
An instrument for the tearing strength measurement, mainly applied on plastic films in relation to the Elmendorf method (in accordance with the international norms). This instrument disposes of an automatic clamping and cutting system of the proof, in addition to a display aimed at analysing the results that can also be transferred onto laptops through the software.
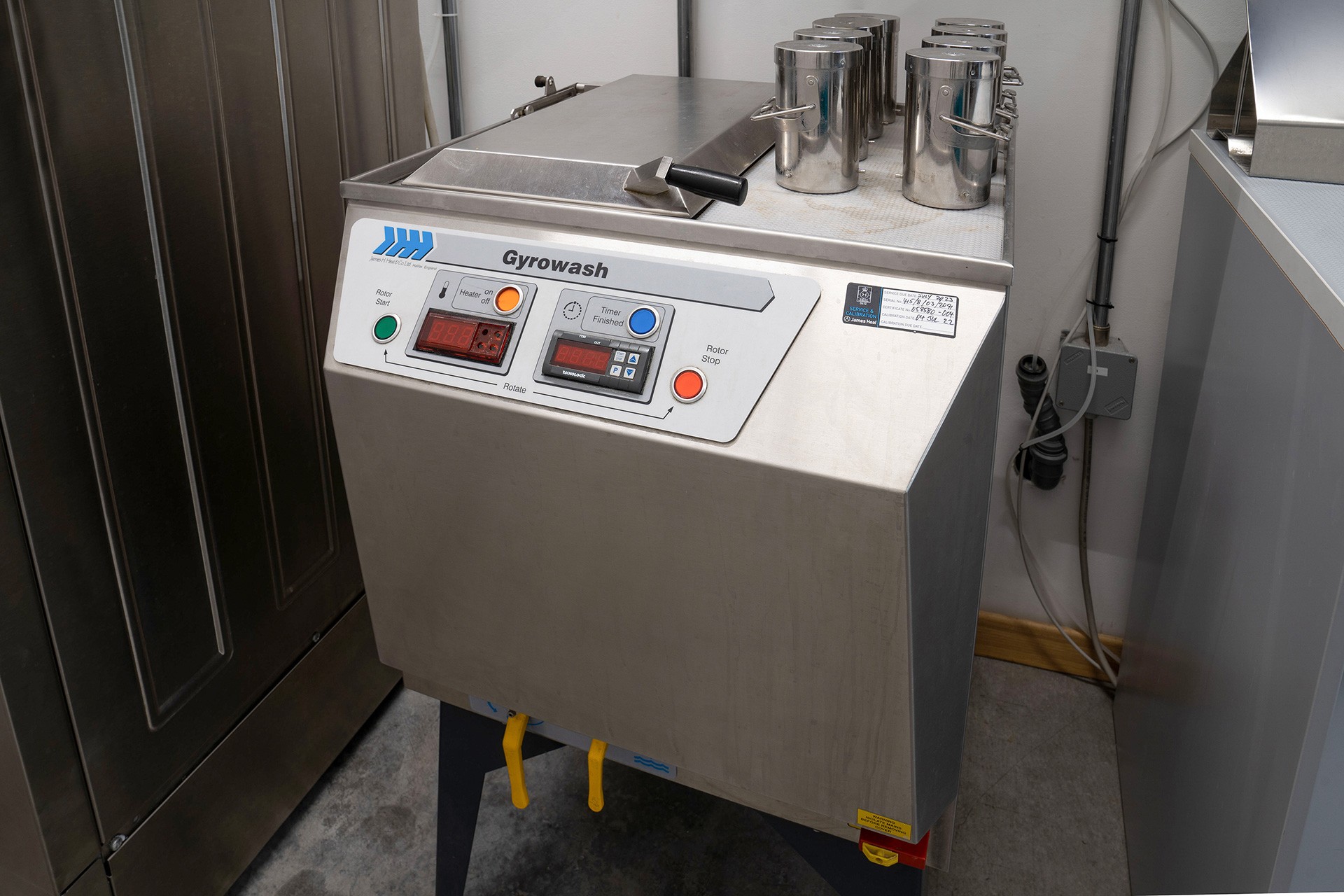
Gyrowash
Thanks to the Gyrowash, we are able to consider the colour fastness to washing, namely, the degree of degradation and/or the colour fading dyed fabrics suffer from after a washing with a detergent or after a dry cleaning.
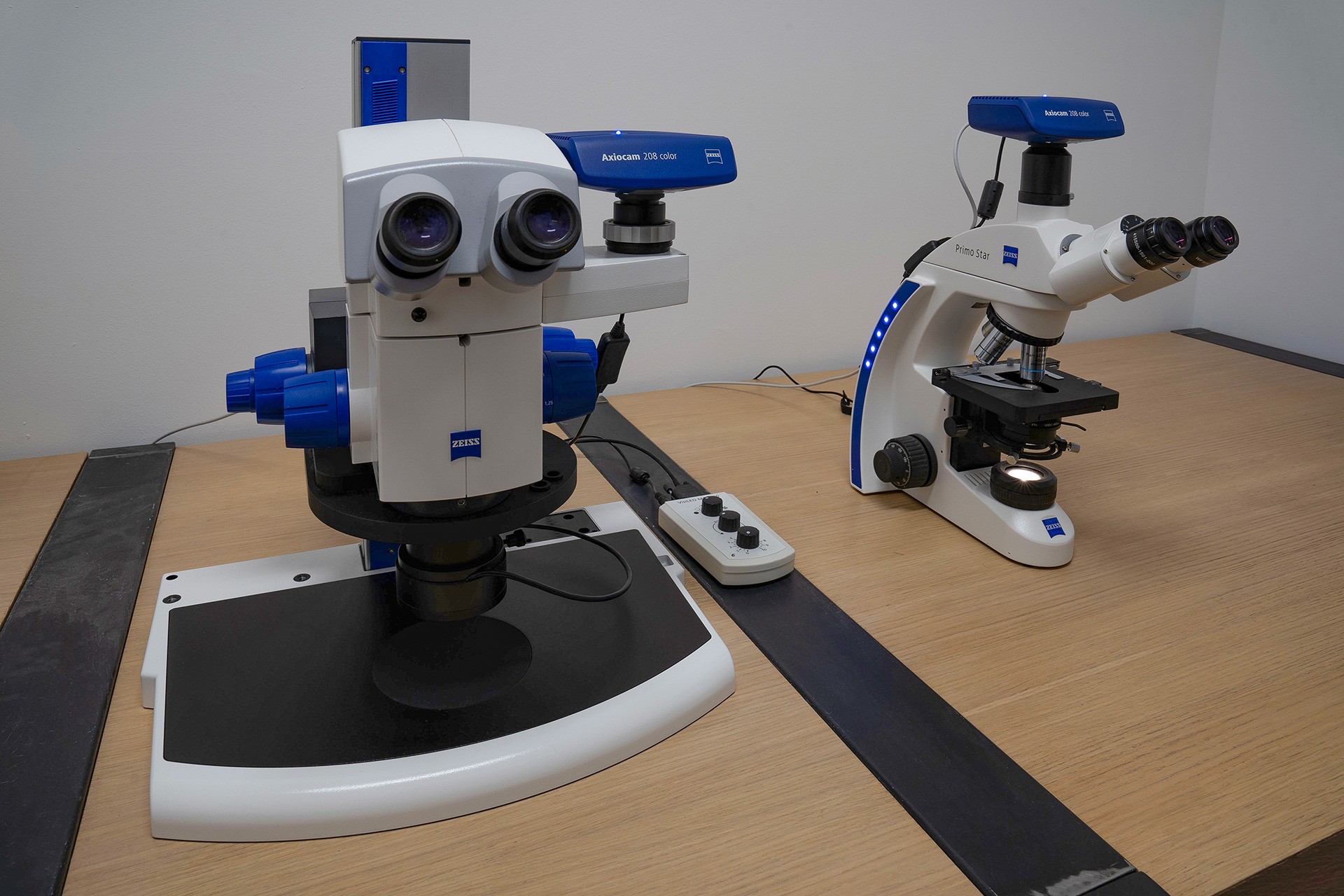
Microscopes
Optical microscopes are widely used for studying the structure of textiles, identifying fibers, examining any defects caused by treatments, as well as studying dye penetration.
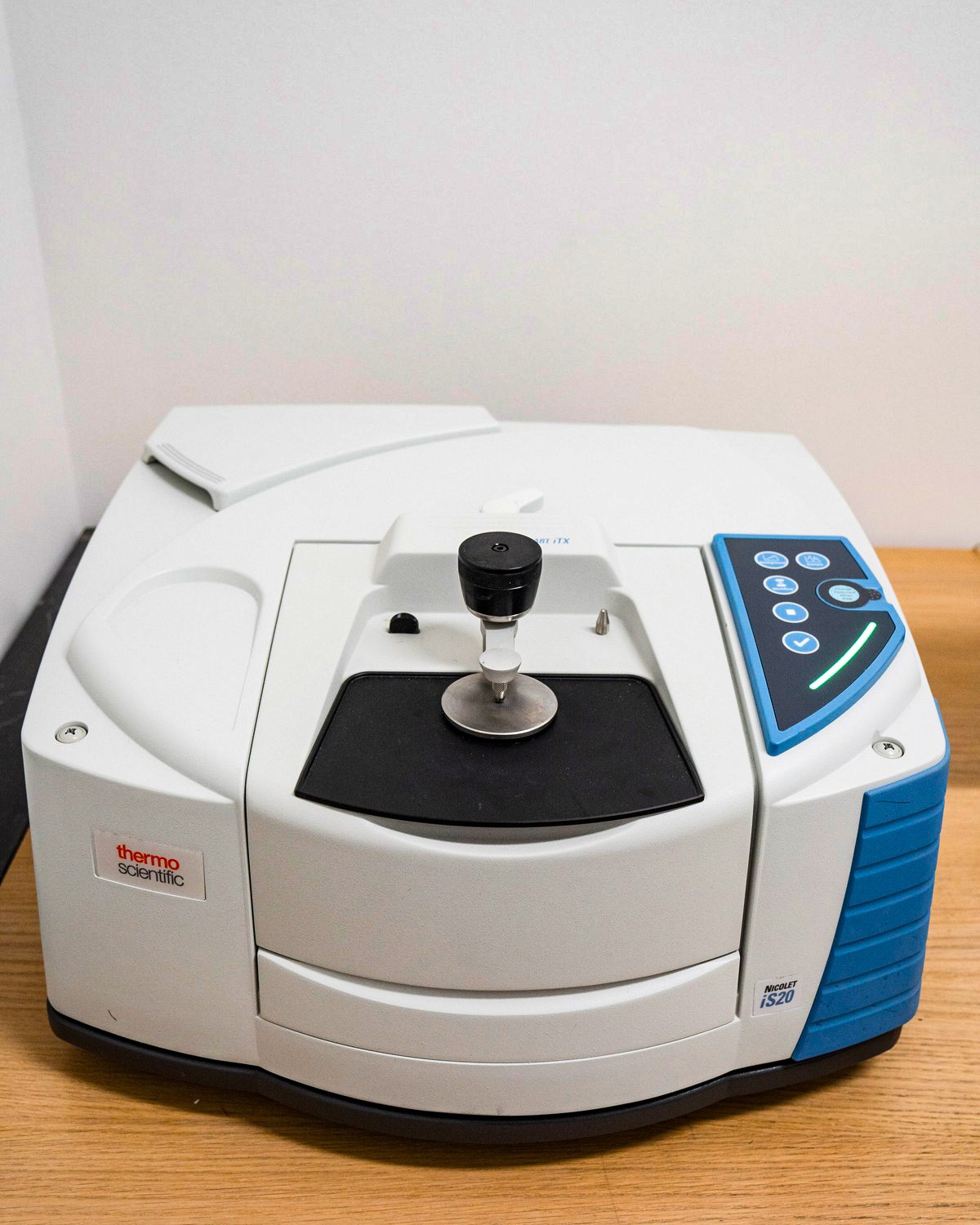
IR spectroscopic
IR spectroscopic analysis is a widely used technique in the qualitative and quantitative analysis of fibers, and especially for the identification of substances present on textile products. It is used both as a quality control tool and as an aid in solving quality problems.
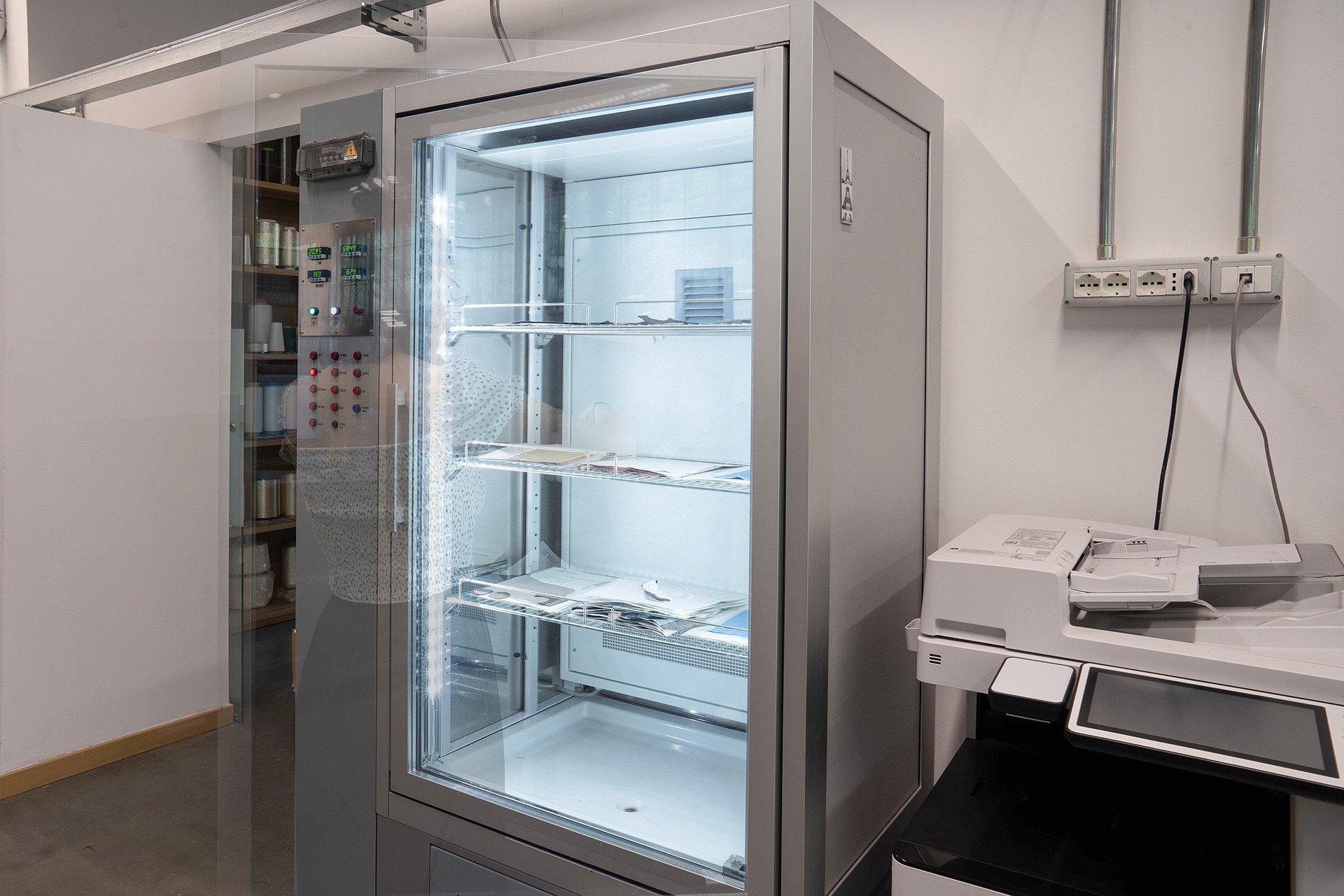
Conditioned room
The conditioned cabinet stores samples intended for quality control laboratory testing, with the aim of bringing them to an ideal equilibrium condition in terms of both temperature and humidity.
Samples are placed on the inner shelves, and air is evenly distributed over several levels, minimizing temperature and humidity gradients, thus ensuring homogeneity according to the requirements of regulations.
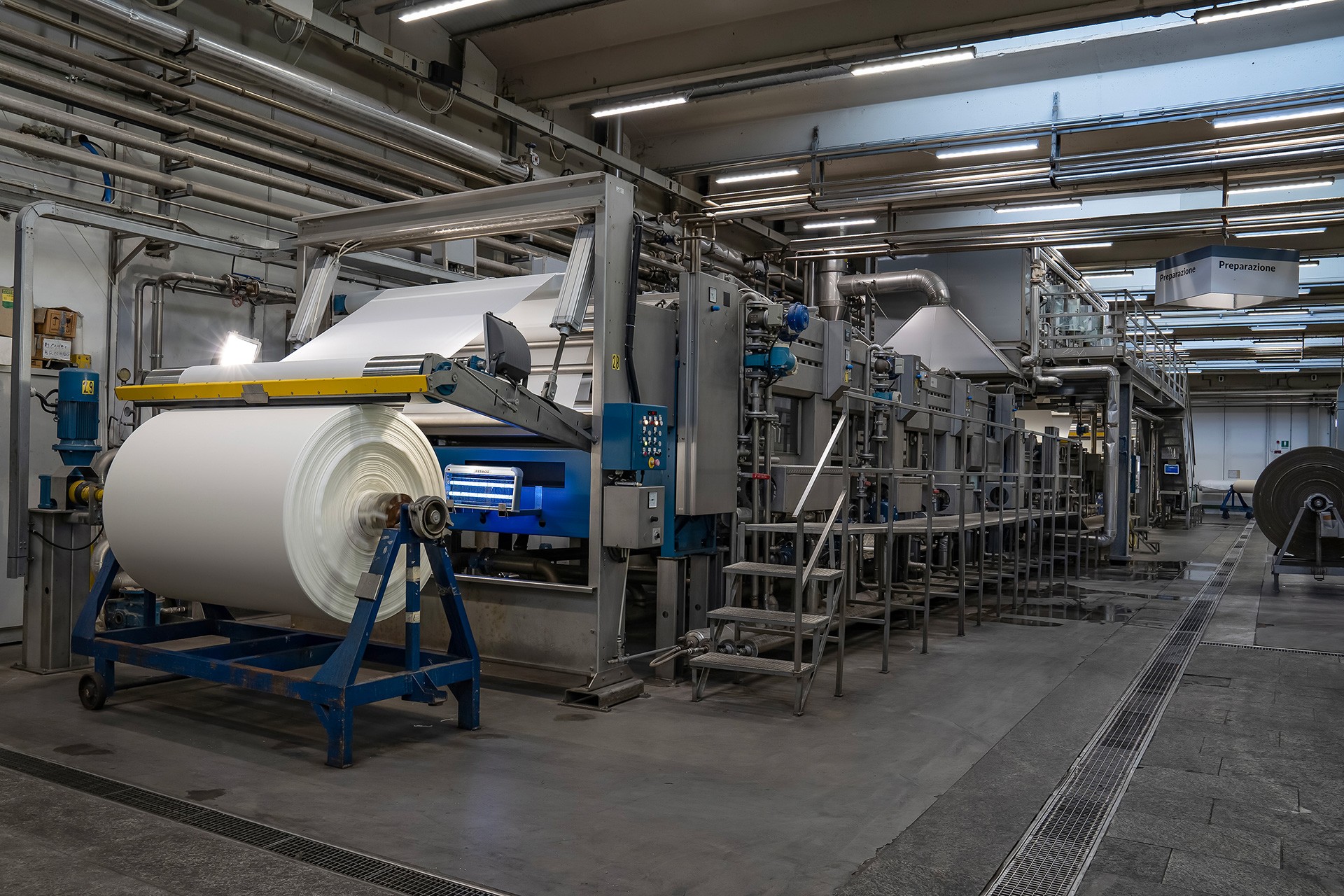
Washing, Bleaching, Mercerisation
The preparation deals with one within the most important operations that occur before the dyeing process. This action is fundamental for the perfect outcome in the final fabric aspect and touch. Inside a single machine, the fabric is washed, bleached (to white) and mercerised (a very strong alkaline treatment capable of making fibres akin to dyeing).
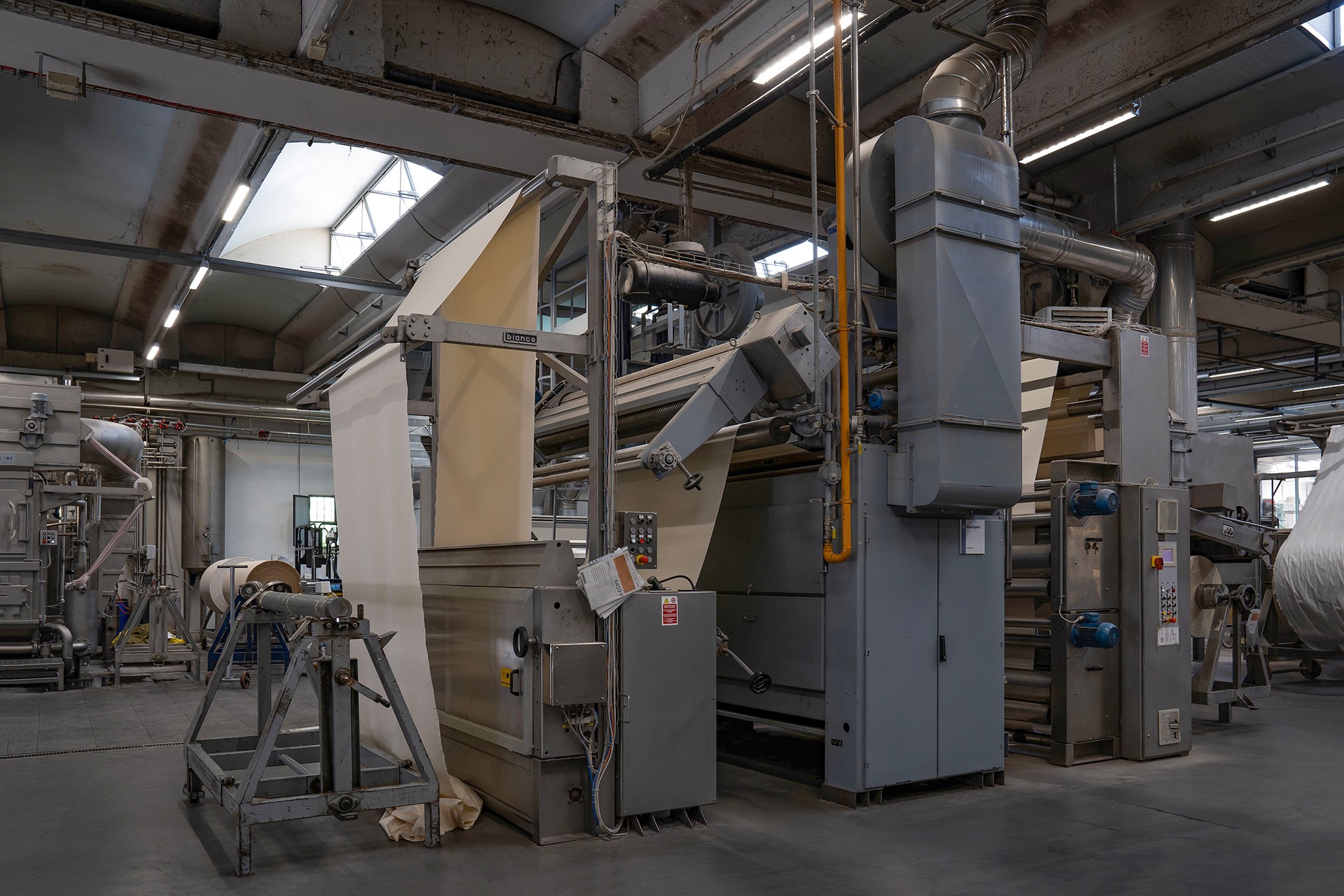
Singeing process
The fabric is treated in this machine through a gas flame that “burns” all the superficial fibre hair in order to make the fabric cleaner to the touch and sight.
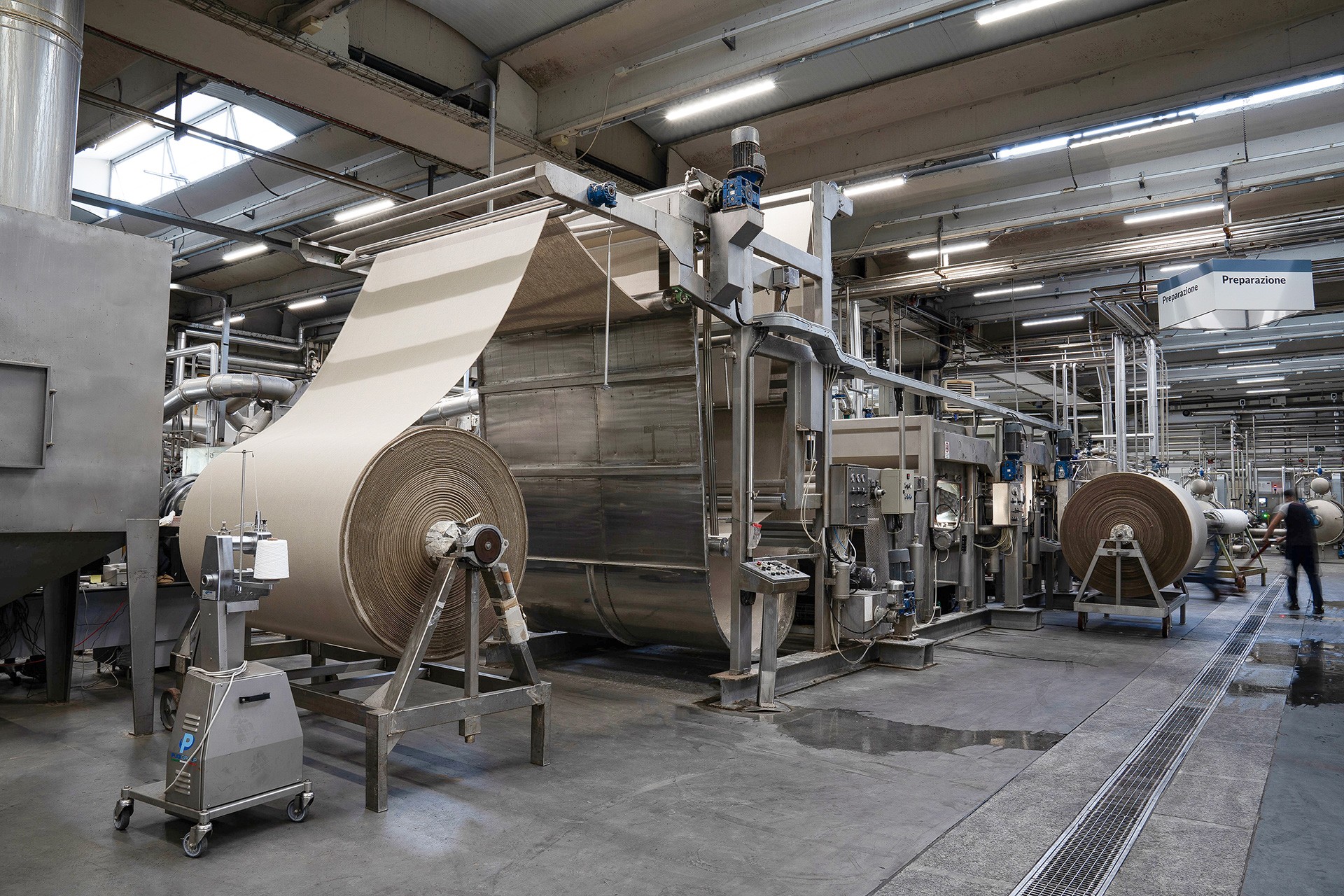
Enzyme Impregnating Machine
The fabric is impregnated with organic enzymes that “clean” the external bark of the cotton, working on the fabric spinning process 24 hours a day.
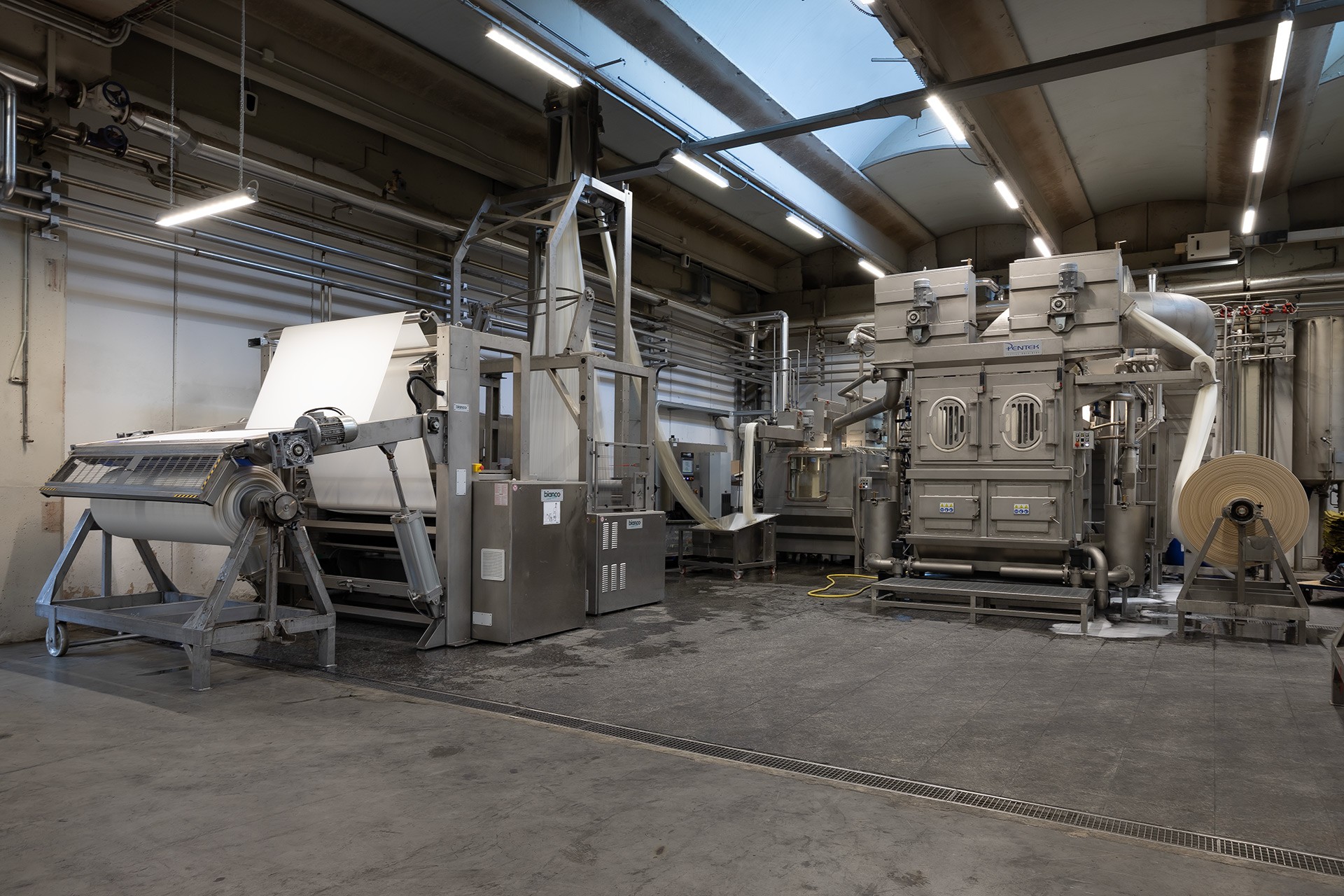
Rope Washing and Enzymatic Treatment
It deals with the production of what happens in the Drum but with somewhat more industrial and reproducible characteristics. We do not achieve the same touch and aspect as in the drum treatment but they are both reproduced in a similar way.
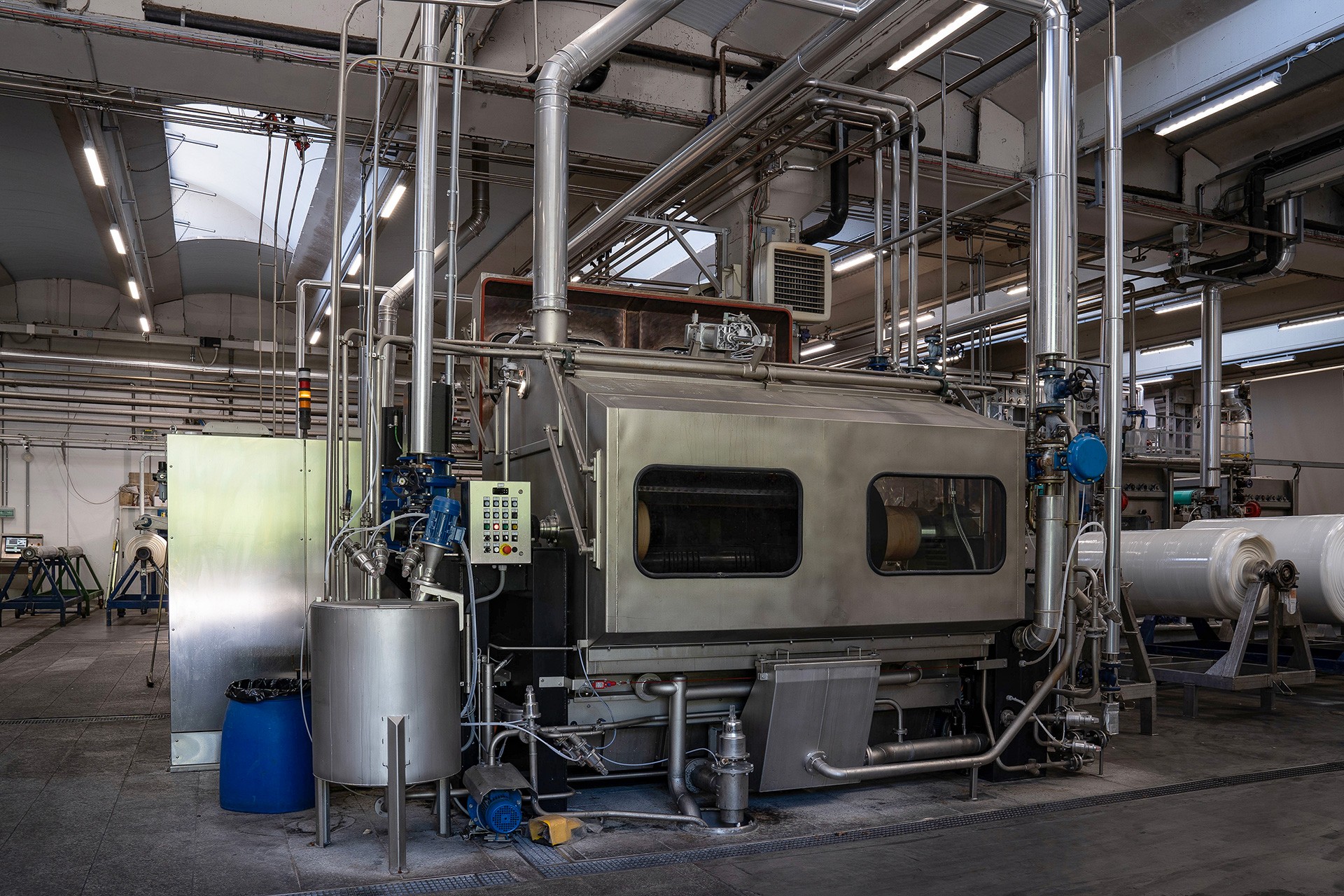
Jigger Preparation
A machine that, by working on the fabric width, prepares the fabric through the washing and bleaching processes, getting it ready for the next dyeing operations.
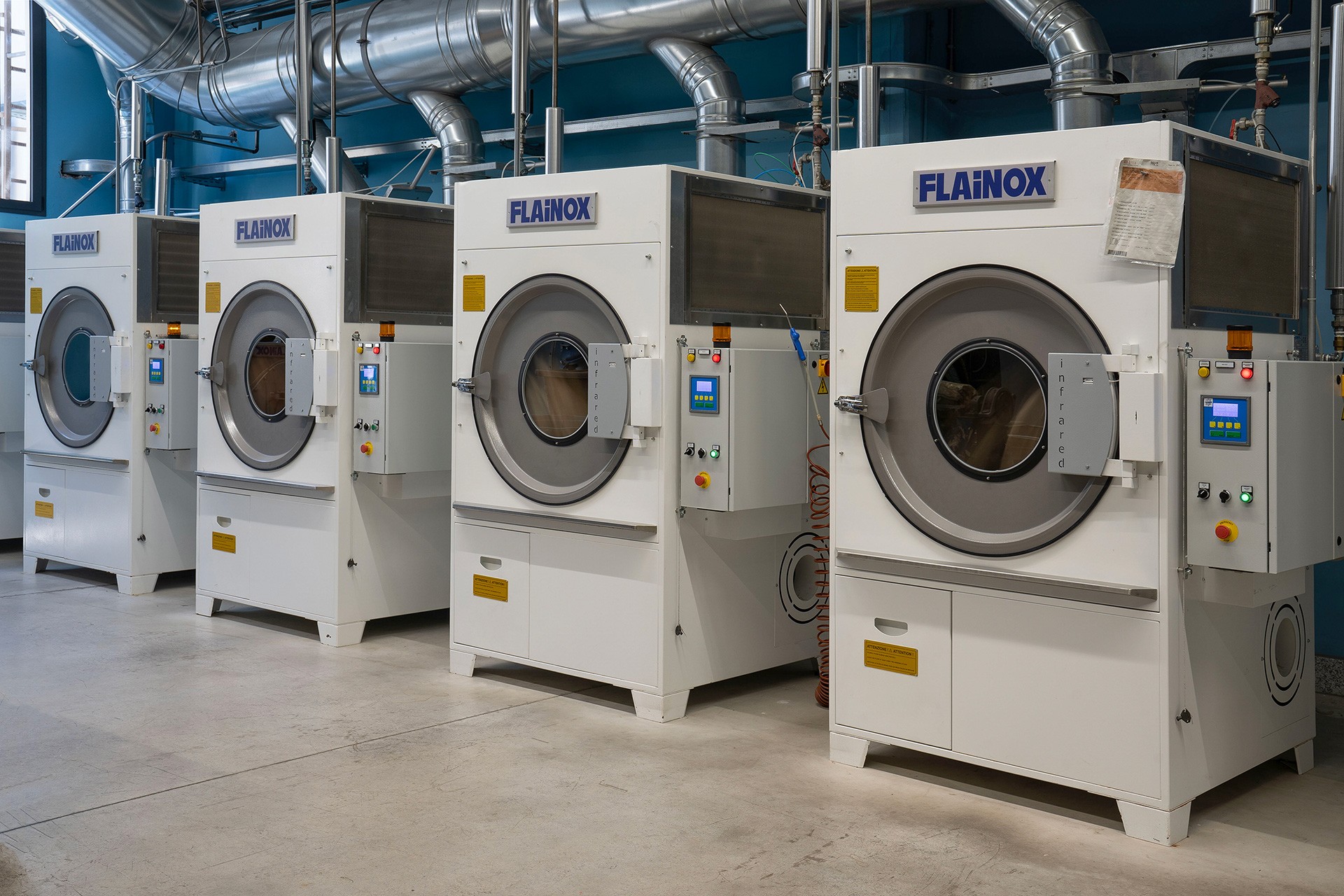
Tumbler Drying Fabrics
Spinning drums where the fabric is dried through steam jets that give the fabric unique shrinkage and elasticity.
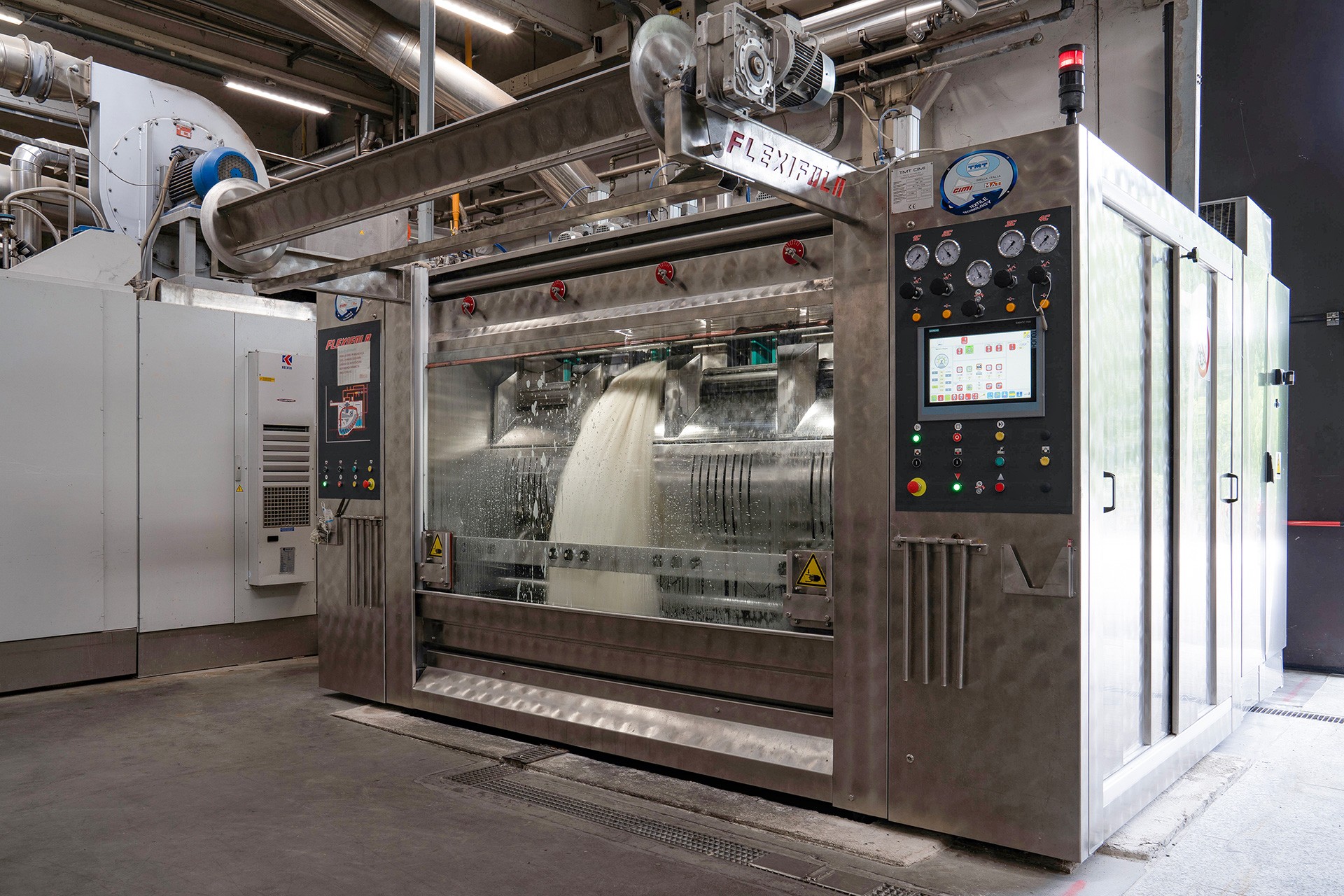
Turbofola
The processes of fulling and rope washing fibrous rope such as woollen ones are carried out in this machine and controlled automatically with an Industry 4.0 management system.
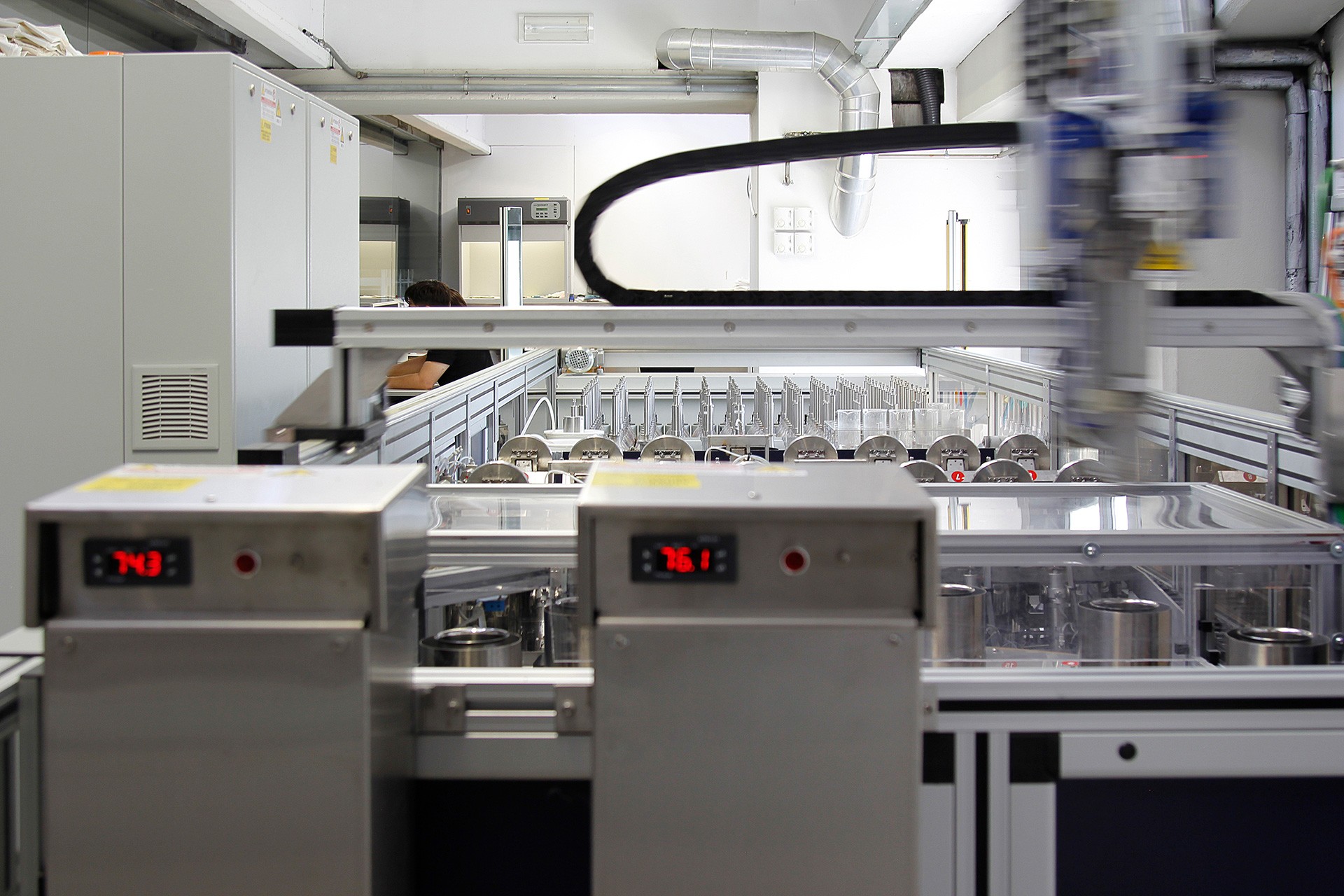
Robot Dye Testing
A fully computerized machine capable of managing the weighing of dye powders, the preparation of the solution and dyeing fabric samples of various sizes. The machine operates automatically 24 hours a day.
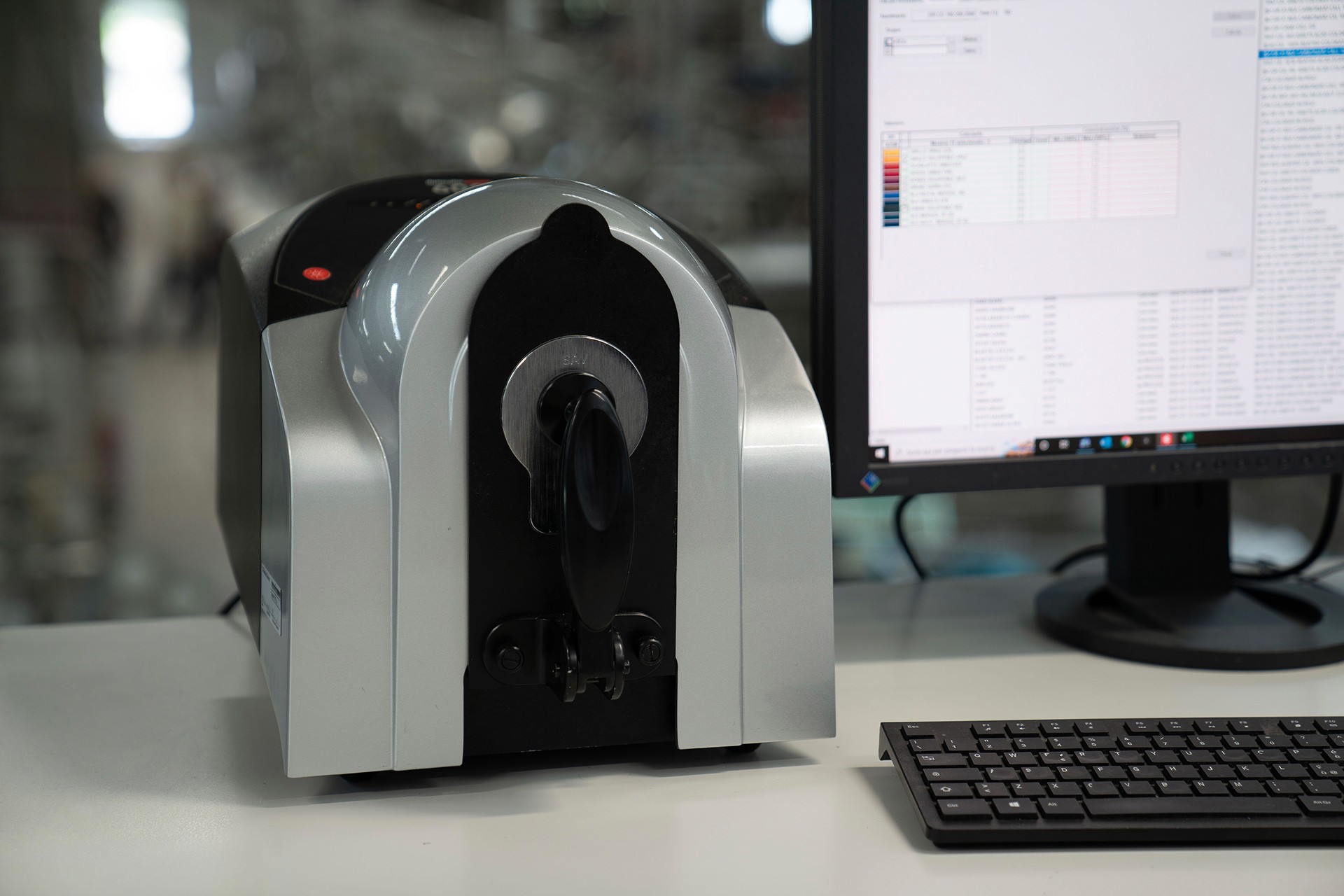
Spectrophotometer
Spectrophotometer is an optical instrument employed for measuring wavelength intensity in a spectrum of light. We employ it so we can read and reproduce all the colours on our fabrics, with instrumental accuracy and not manual.
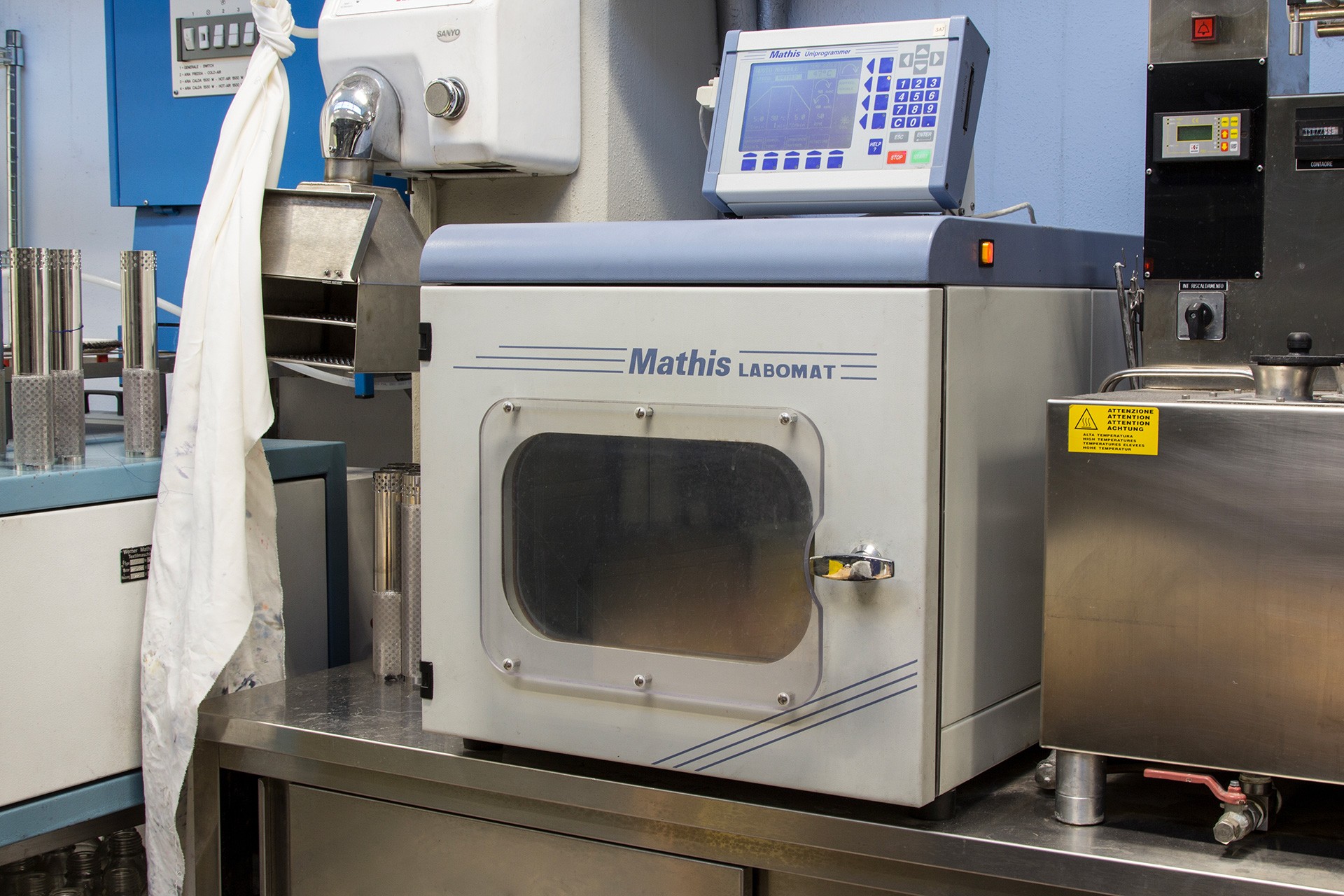
Rotary Dye Proofing Machine
Semi-automatic machine capable of dyeing small fabric samples into a steel container, it is perfect for small dyeing lots.
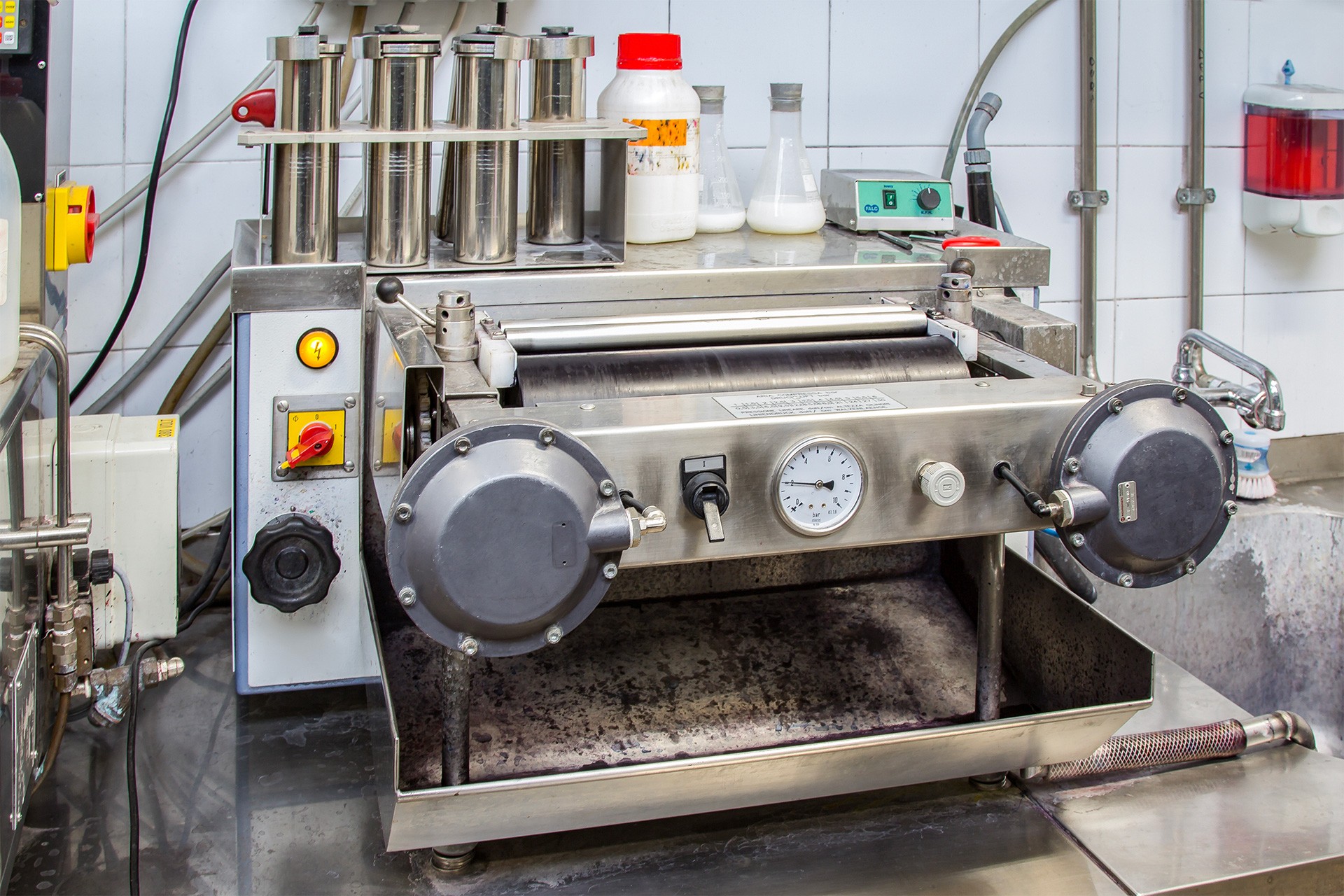
Foulard Laboratory
Machine that remakes a miniature of the dyeing foulard (in relation to) where the production is made.
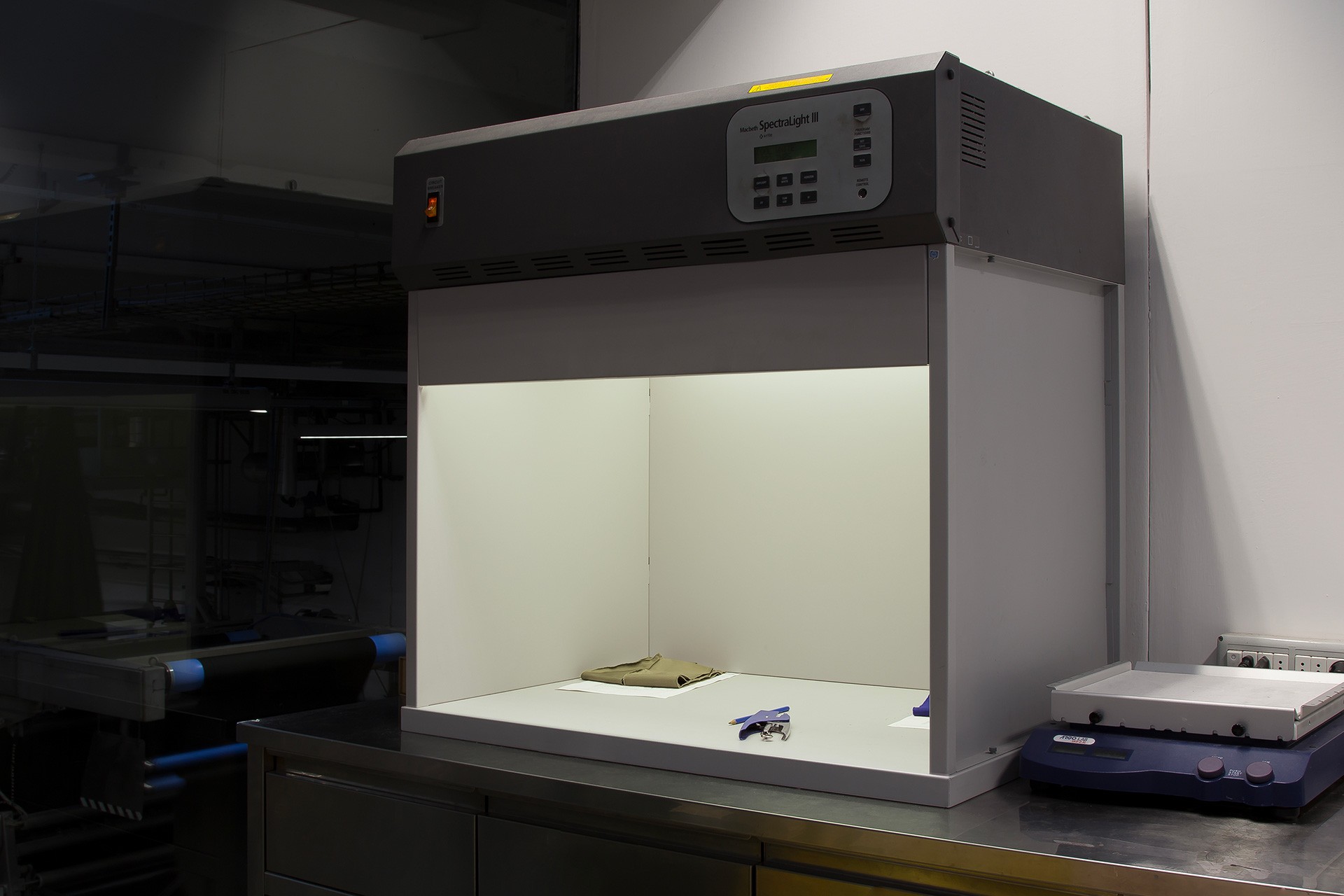
Color Check Lamp
Certified box with six different kinds of lighting to check colour shades before shipment. Under these lights, we can check the way colours react to cold, hot, UV and other light combinations upon customer’s request.
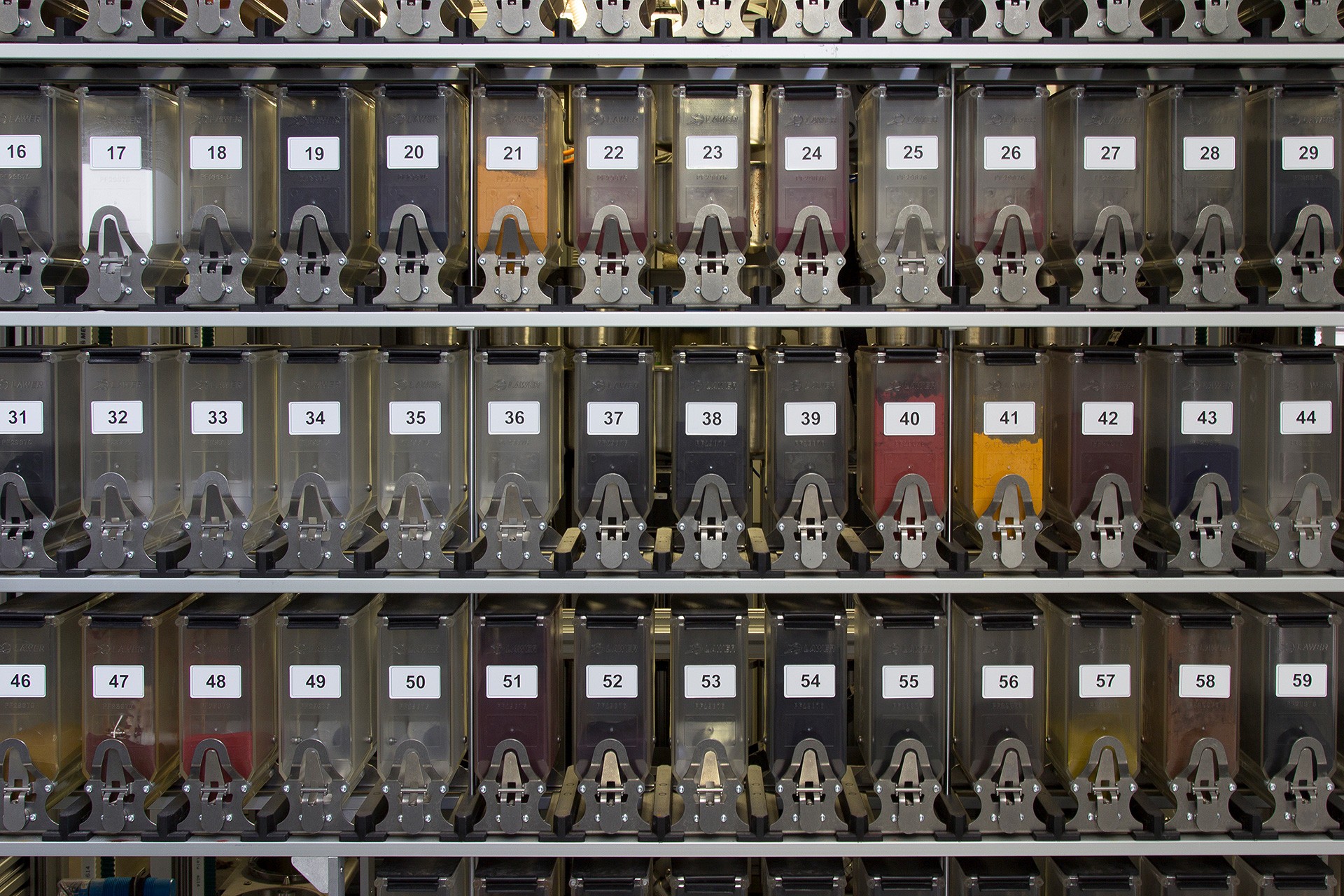
Dye Sample Dosing System
At Beste S.p.a., no person touches or handles dye powders, chemical auxiliaries or anything else because we have three systems available that manage everything through computerized control; from dosages of 0.1 gram of dye to kg of acids or alkalis.
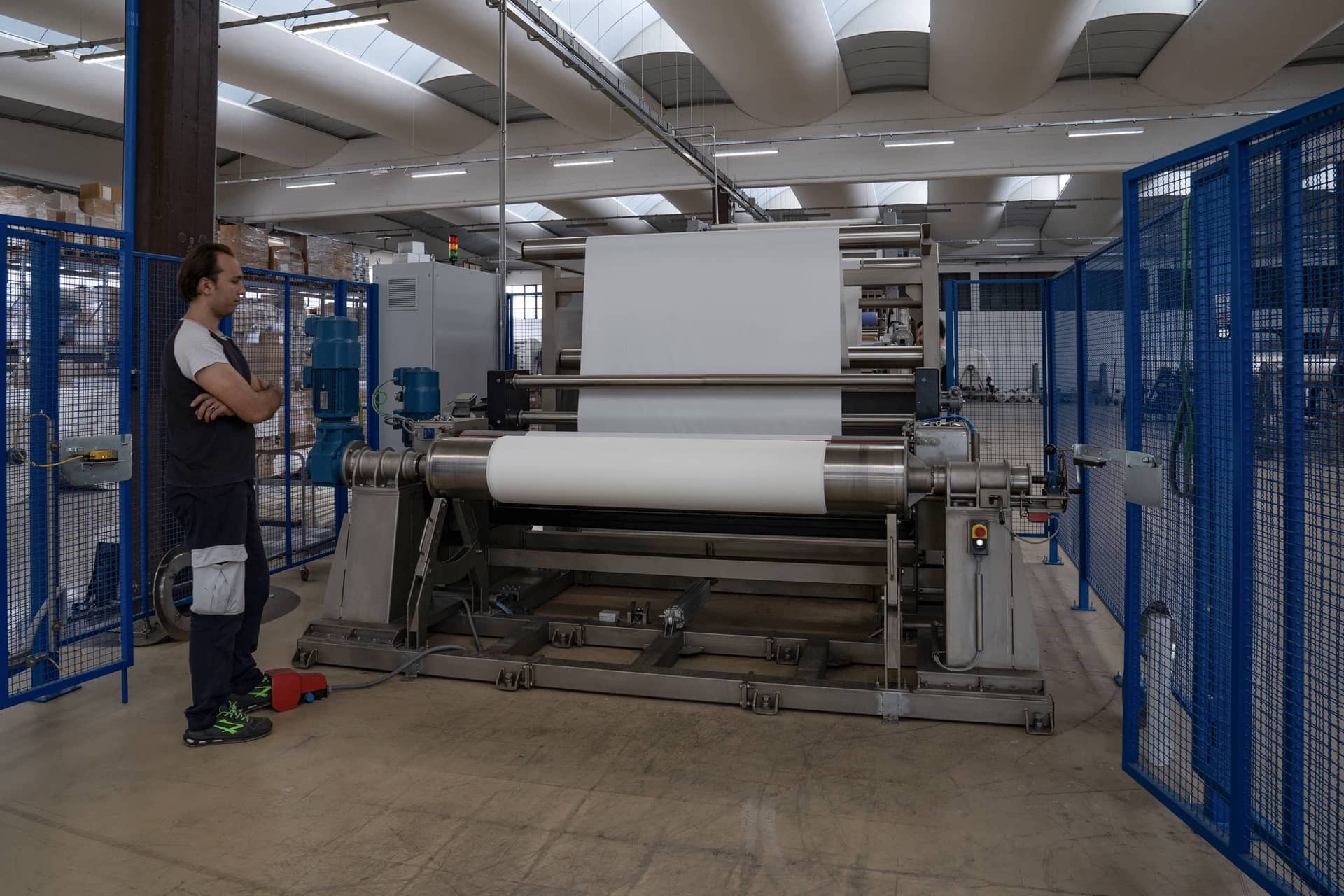
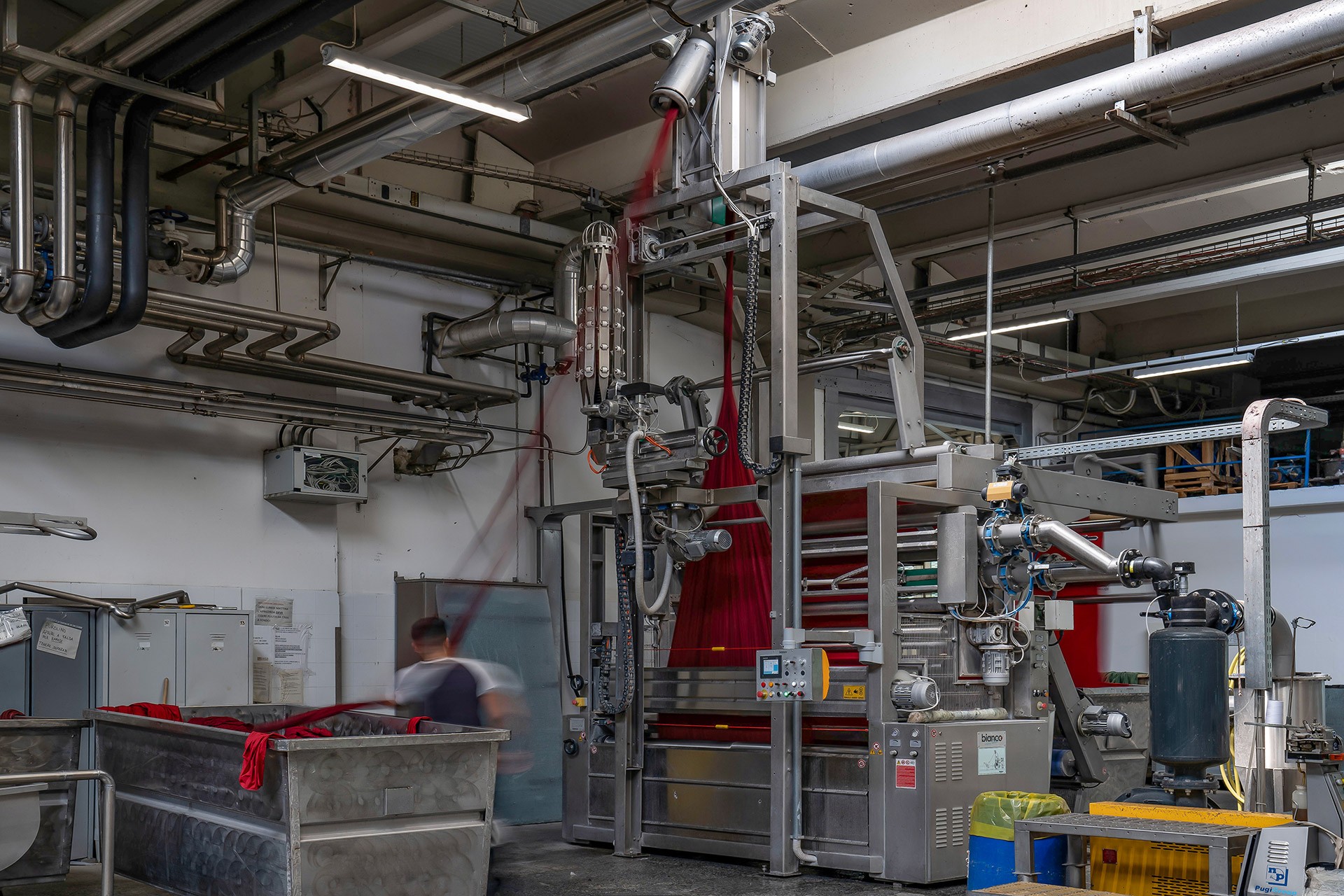
Rope Opener
The fabric is expanded in order to be flat dried in the next phase.
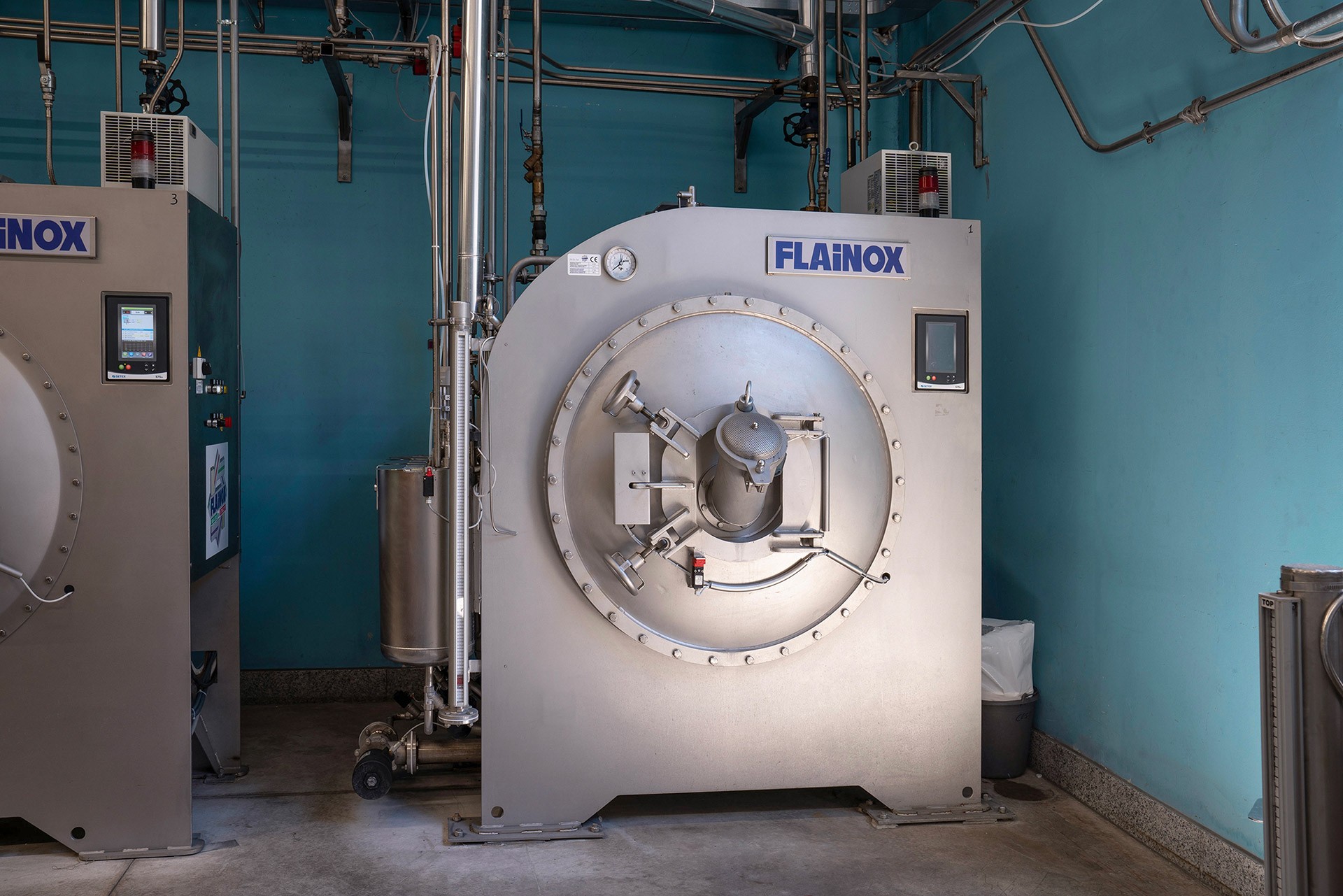
Tumbler Dyeing Process
The fabric or the garment is treated within large tumblers to make it unique and with a type of workmanship that is handcrafted and at the same time unparalleled. Enzymes softening products, dyes and stones are then used and added inside the machine along with fabrics or garments so as to get some very particular effects.
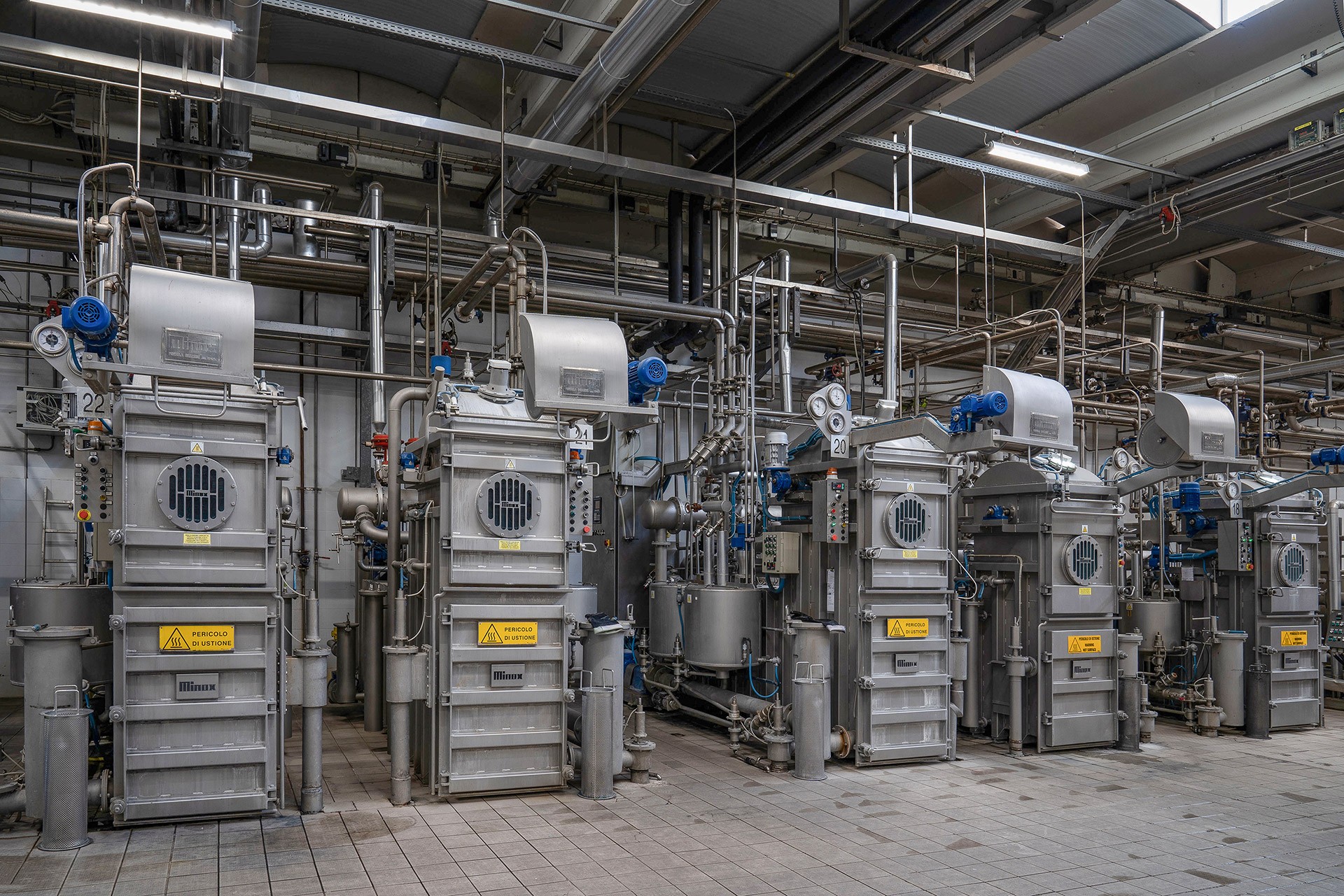
Flow Process
An intermittent process in which the fabric is rope dyed under atmospheric pressure; this treatment allows cellulosic, protein and synthetic fibres to be dyed, except for polyester. The main characteristic of this dyeing process consists in moving the fabric inside the machine through a mechanic energy. We have three different sizes of these machines, one for prototyping process, one for samples and one for production itself.
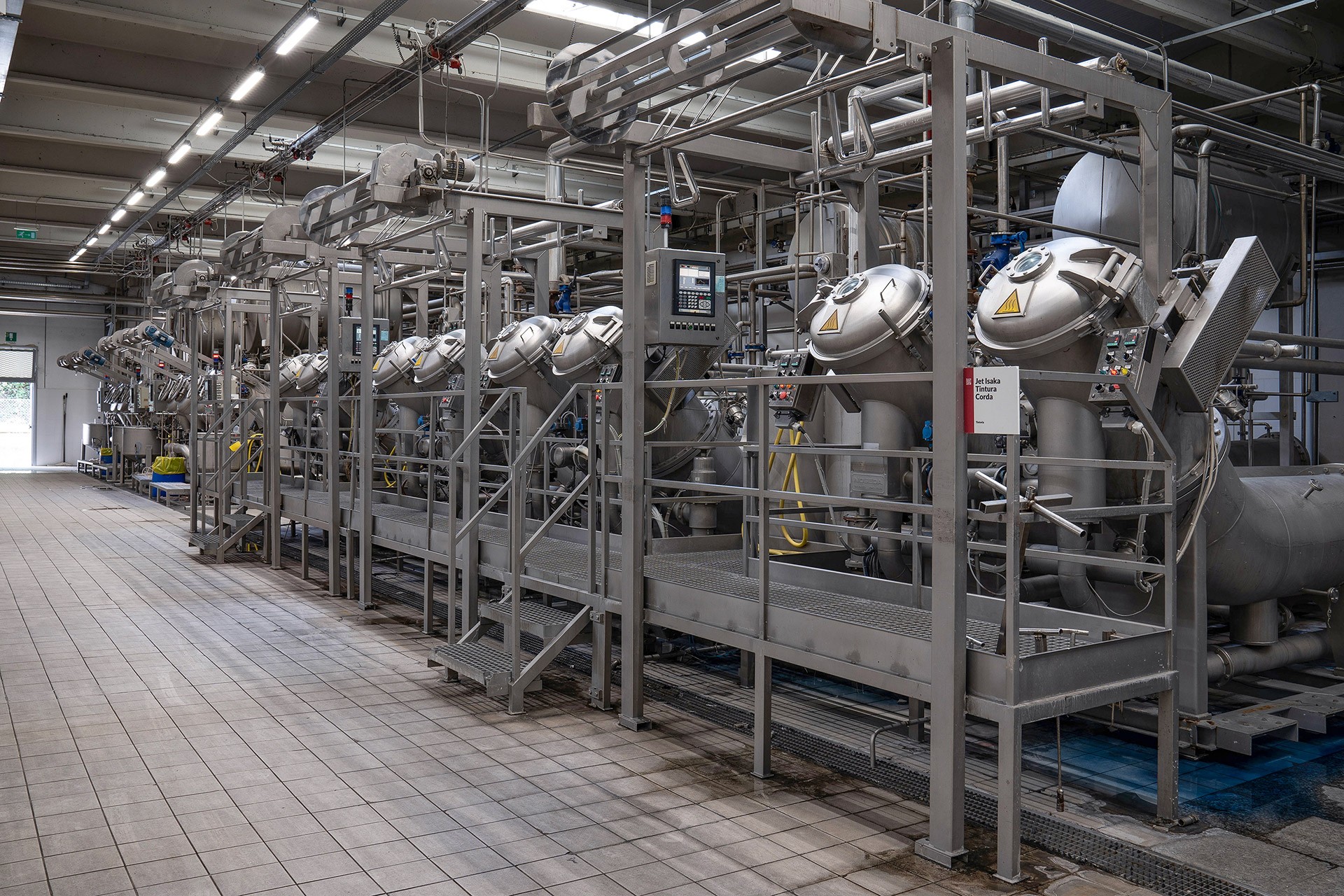
Jet Flow
An intermittent process in which the fabric is dyed under pressure and we have the maximum dyeing fastness and depth. Even though it is the most expensive method of all, it makes the fabric richer in full and vivid colours. JET machines are versatile and capable of dyeing any fibre, as they reach 140°C.
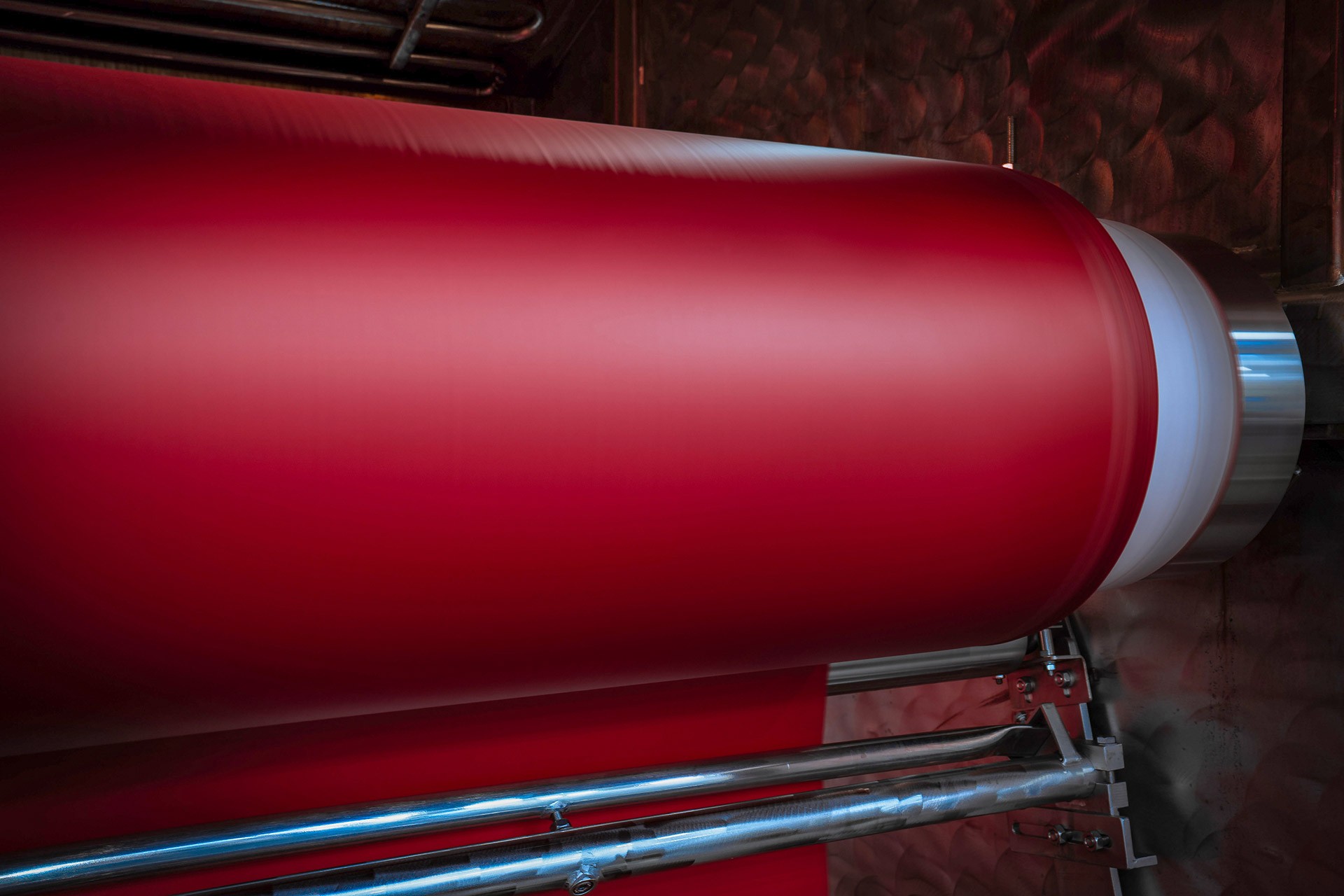
Dyeing Jigger
An intermittent process in which the fabric is hot-dyed. These are machines that work under atmospheric pressure, therefore able to dye every kind of fibre, except for polyester. The fabric moves from cylinder A to cylinder B by plunging itself into the dye.
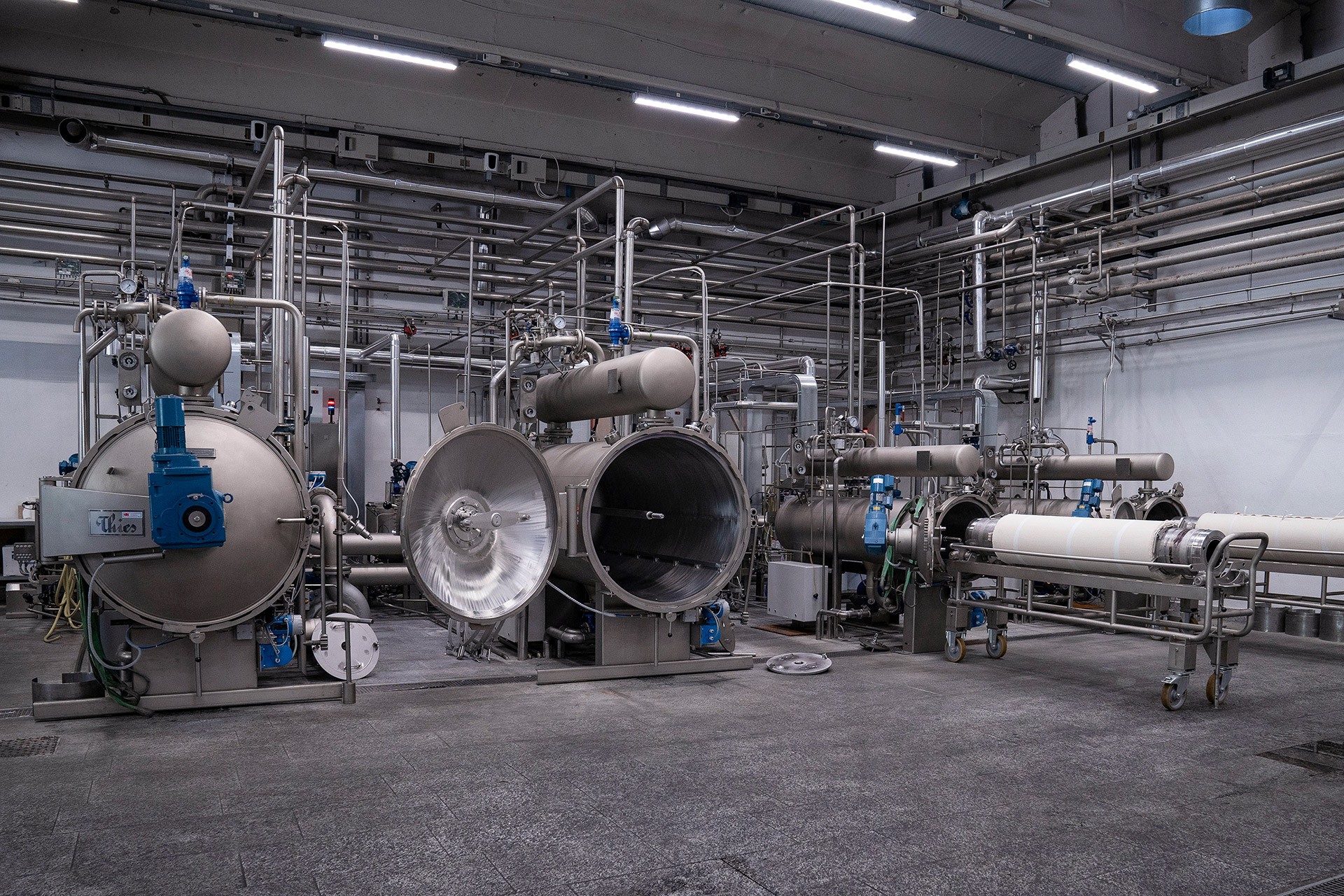
Torpedoes
It consists of a very innovative intermittent pressured dyeing process. A very complex procedure in which the fabric is rolled up on a drilled stand called Subbio, then placed within the torpedo and later submerged. The dyeing process is carried out thanks to the transfer of high-pressured fluid from the inside the stand to the outside going through the fabric, which, therefore, becomes dyed. We witness a great savings in water and electricity usage in this innovative machine, but, above all, it allows shortening the time.
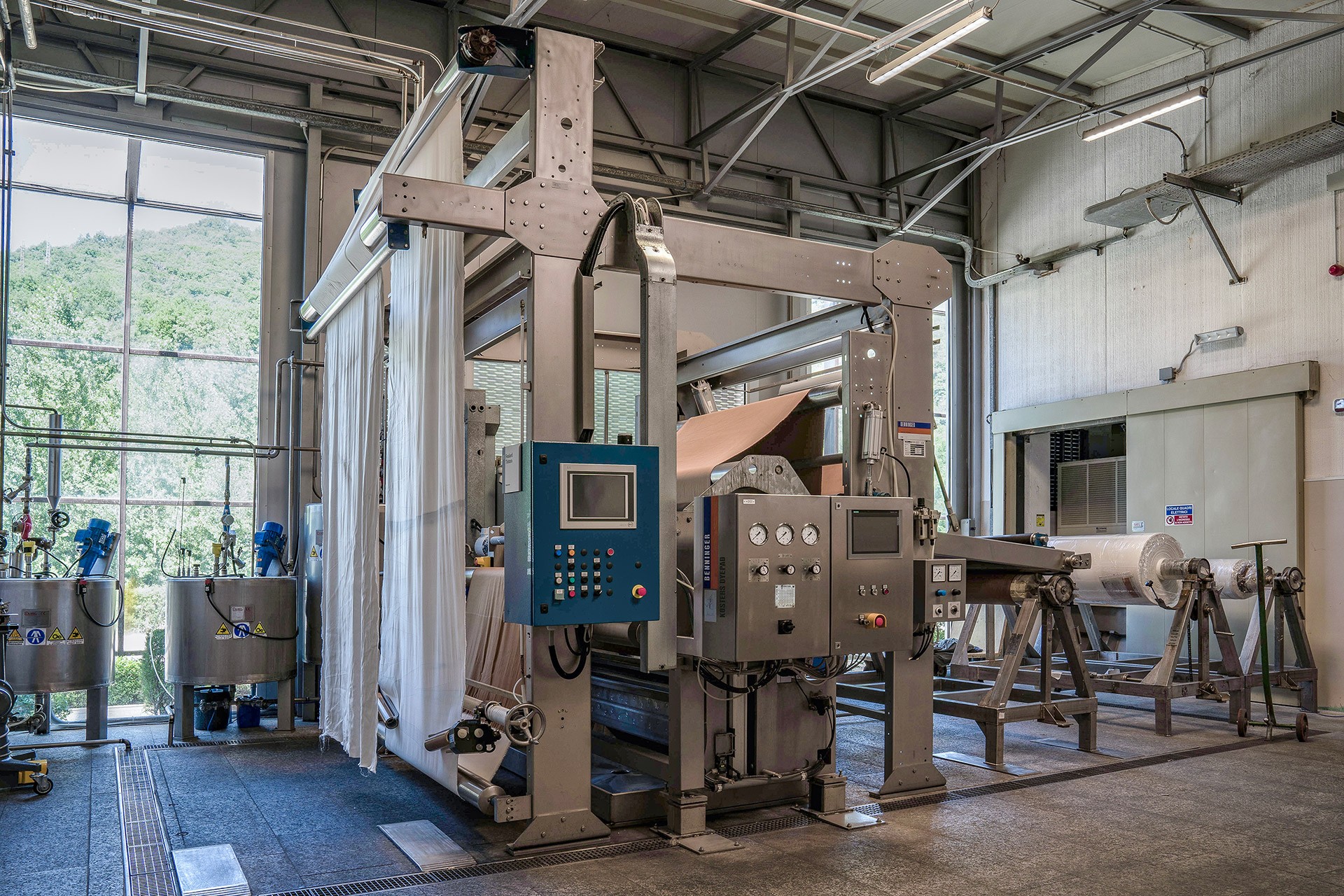
Pad Batch
A continuous dyeing process. This machine exclusively dyes cellulosic fibres. The fabric passes through a marl containing dyes and textile auxiliaries thanks to a chemical reaction that makes the fabric appear instantly and visibly dyed. In order to strengthen the bond between dye and fibre, the fabric needs to store in the dark for 18 hours and be progressively washed out of the excessive colour. This dying phase makes the item flat and it does not present a strong permeation of the colour. It is a cost-effective process used for lots of substantial square footage.

Automatic Dye Dosing System
At Beste S.p.a no one touches or handles dyestuffs, chemical auxiliaries or similar products. Instead, we utilize three computerized systems in place that manage the entire operation; from doses of 0.1 grams of dyestuff, to kilograms of acids, or alkali.
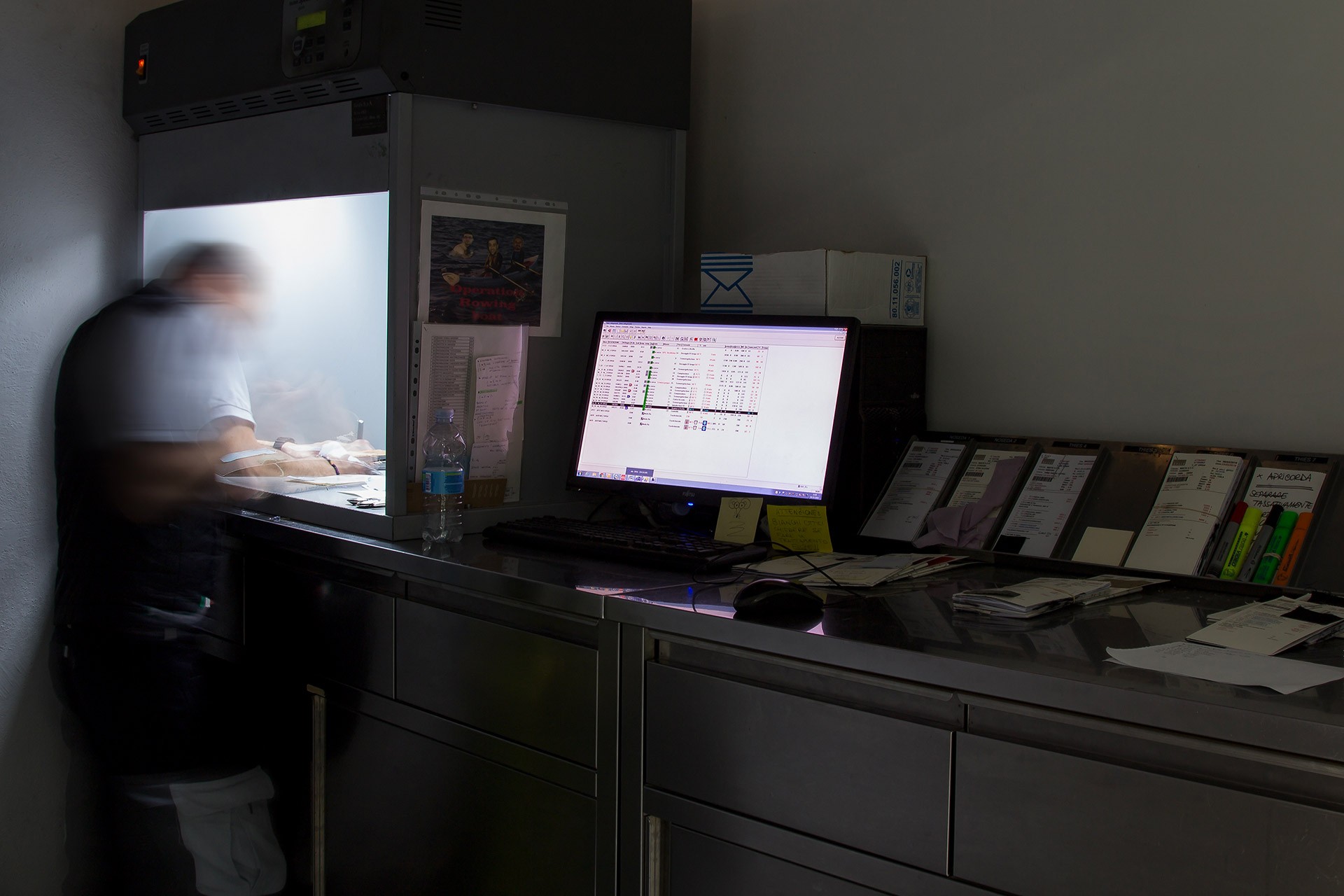
Darkroom
A place neutralized from external interactions where colours realized in the various dyeing processes are inspected and corrected by a technician.
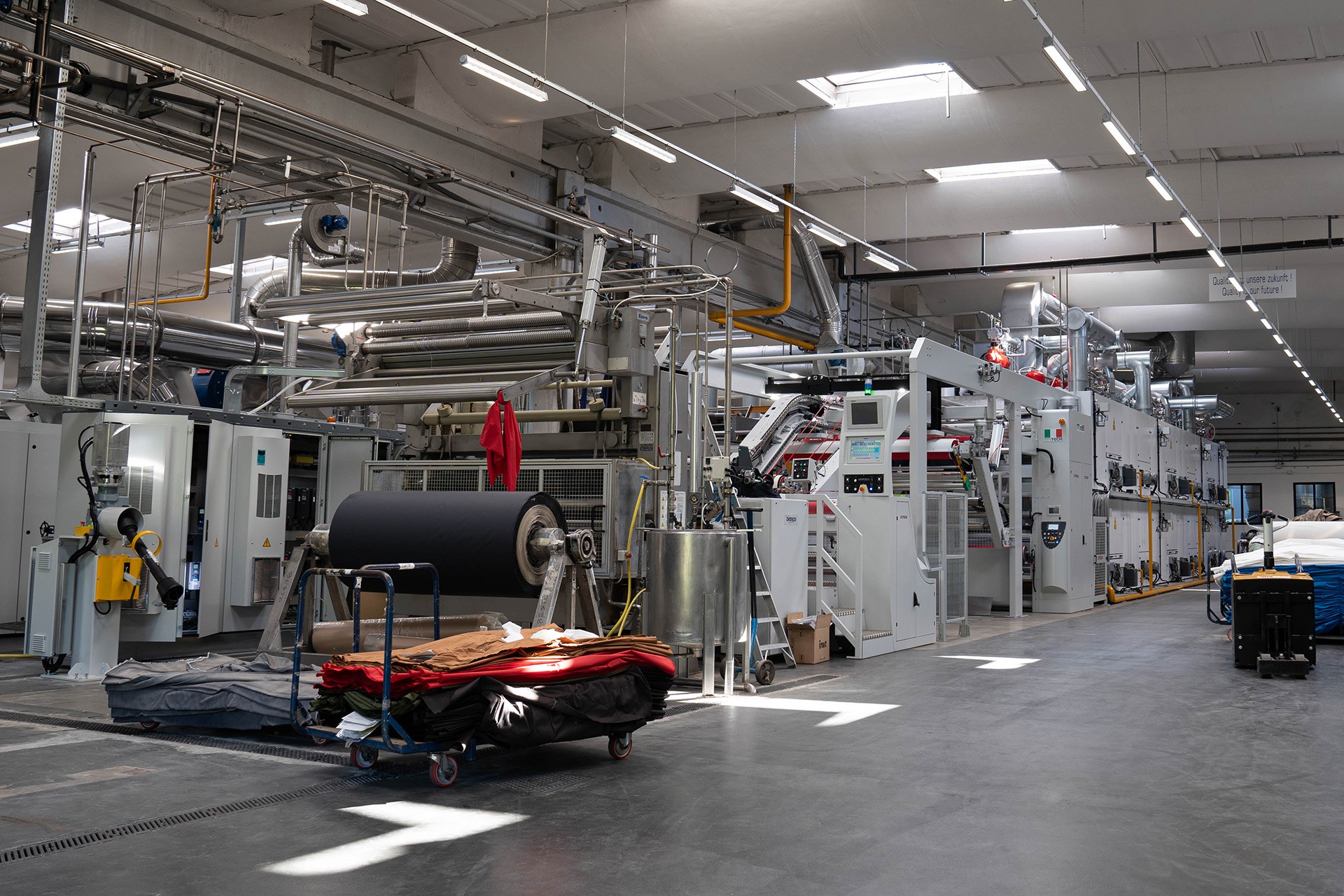
Ramosa Double Deck
In this machine, the fabric is dried and secured to make it stable against shrinkage (caused by steam water, dry cleaning). Through a peculiar technology 4.0 check, we control the residual moisture on the fabric and recover the heat expelled in the chimneys.
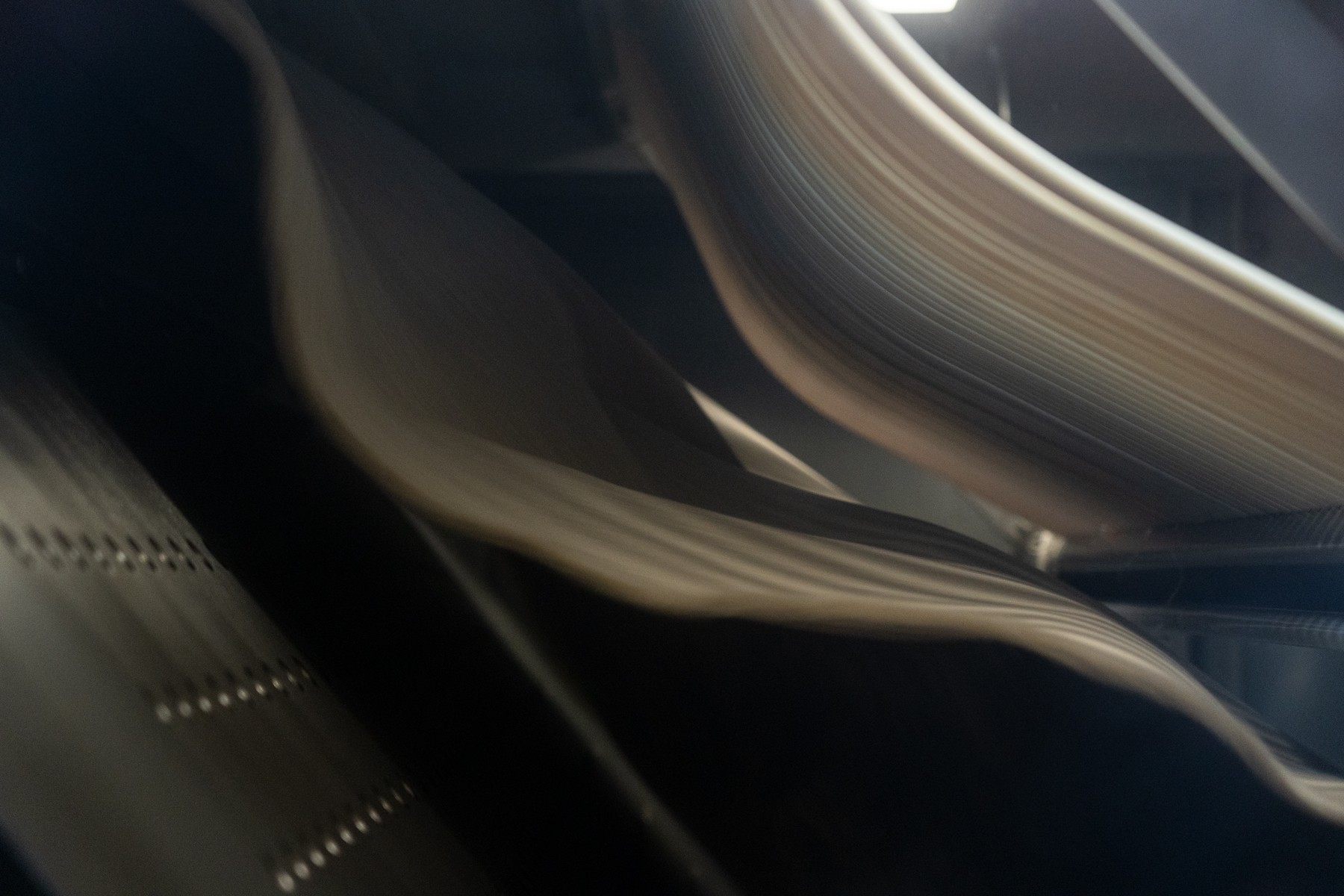
PowerAir
Another machine that completes the washing cycle and the fabrics treatment: the fabric is "whipped" thanks to the hot air jet on moving walls that soften it while it is dried.
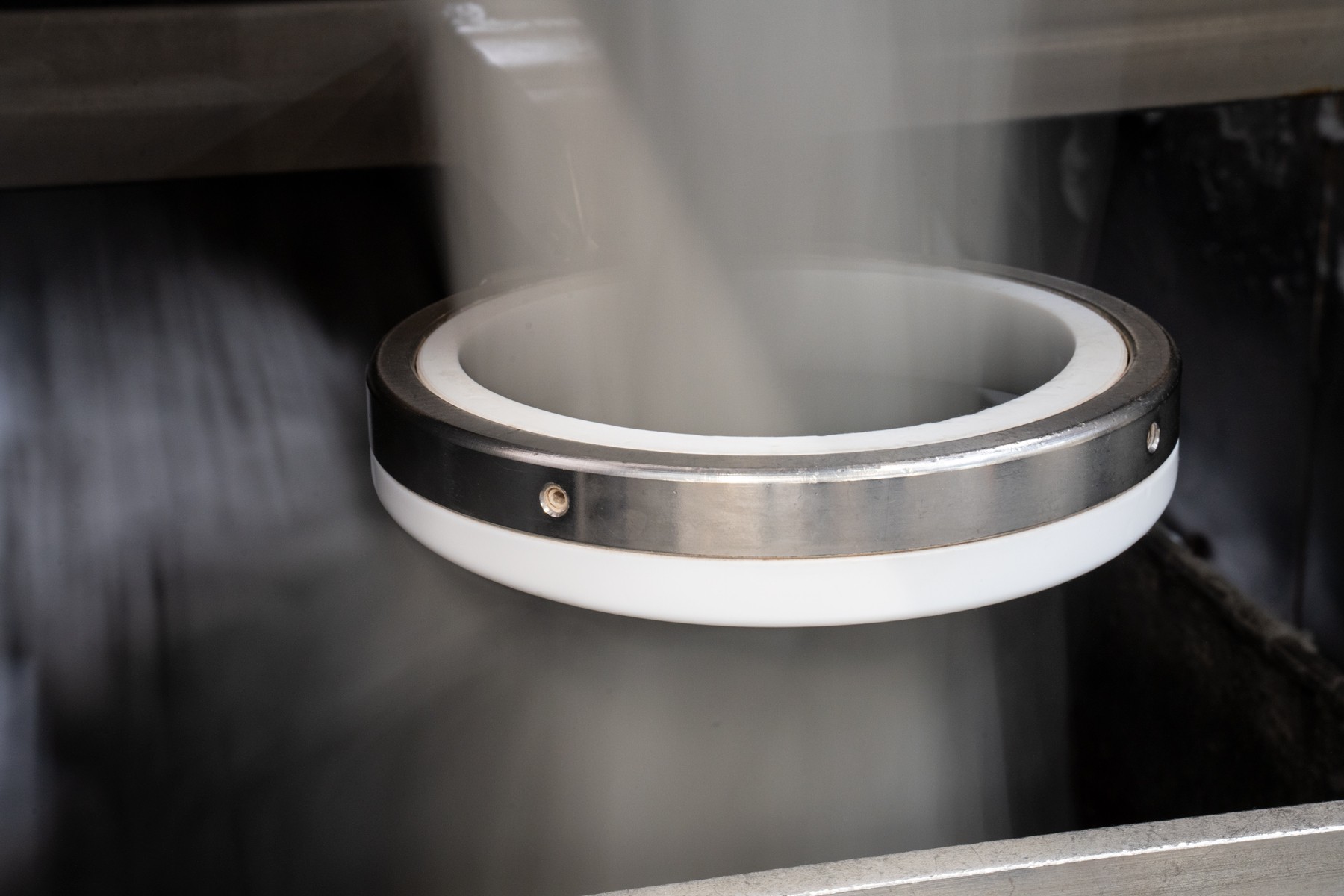
Flyair
Another machine for drying and ennobling fabric: the fabric is dried in rope by passing it through a ring with a strong jet of hot air. While the fabric dries, it is softened by mechanical action.

Diamond Grinder
The fabric is abrased with a very thin sand paper. The goal is to have a peachy handfeel result. Given that the machine is adjusted with high precision because the greatest risk is to tear the fabric if the pressure should be too high, the resulted effect is surely surprising.
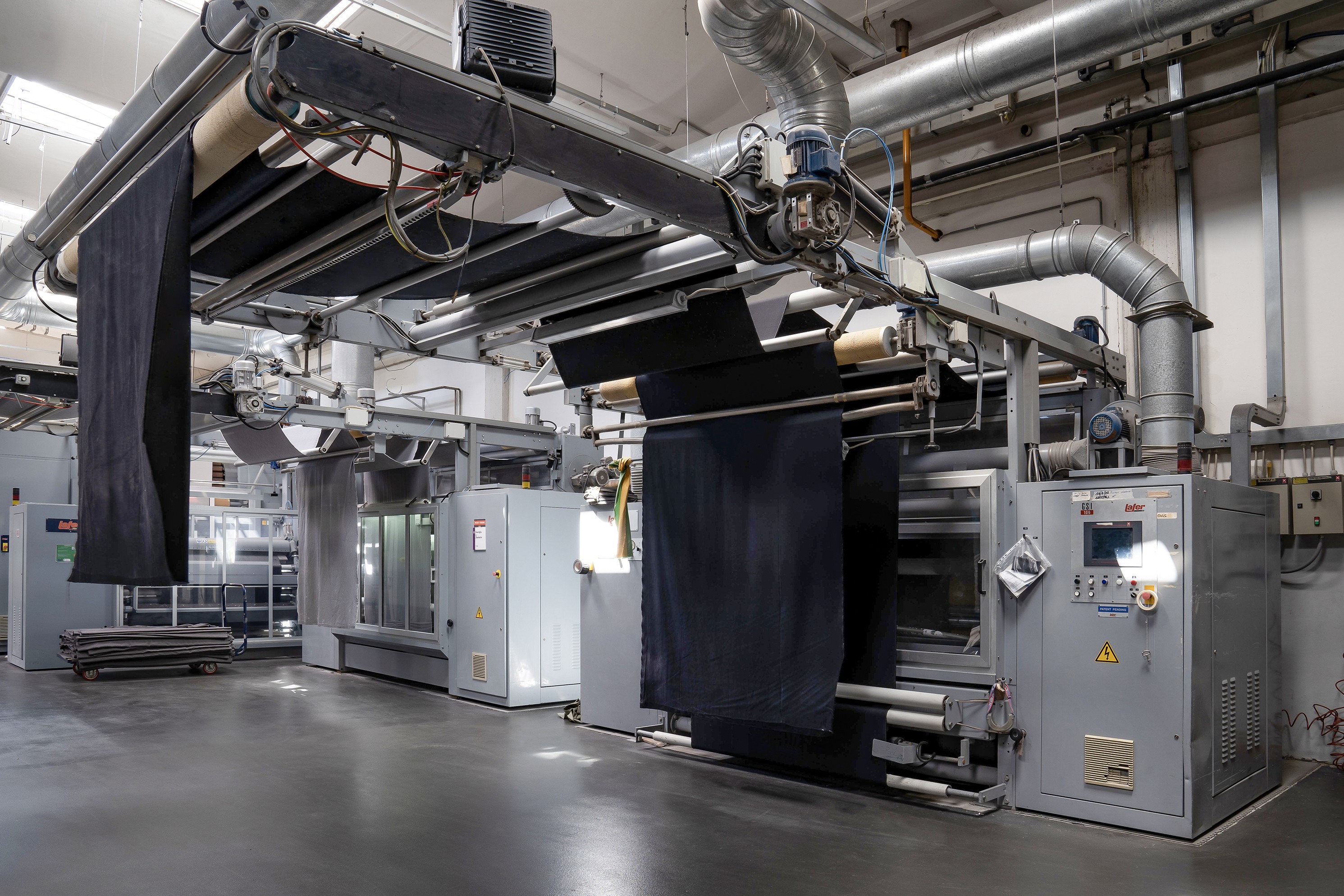
Brush Grinder
The fabric is abrased with some sand paper so as to create a peachy handfeel result. Given that the machine is adjusted with high precision because the greatest risk is to tear the fabric if the pressure should be too high, the resulted effect is surely surprising.
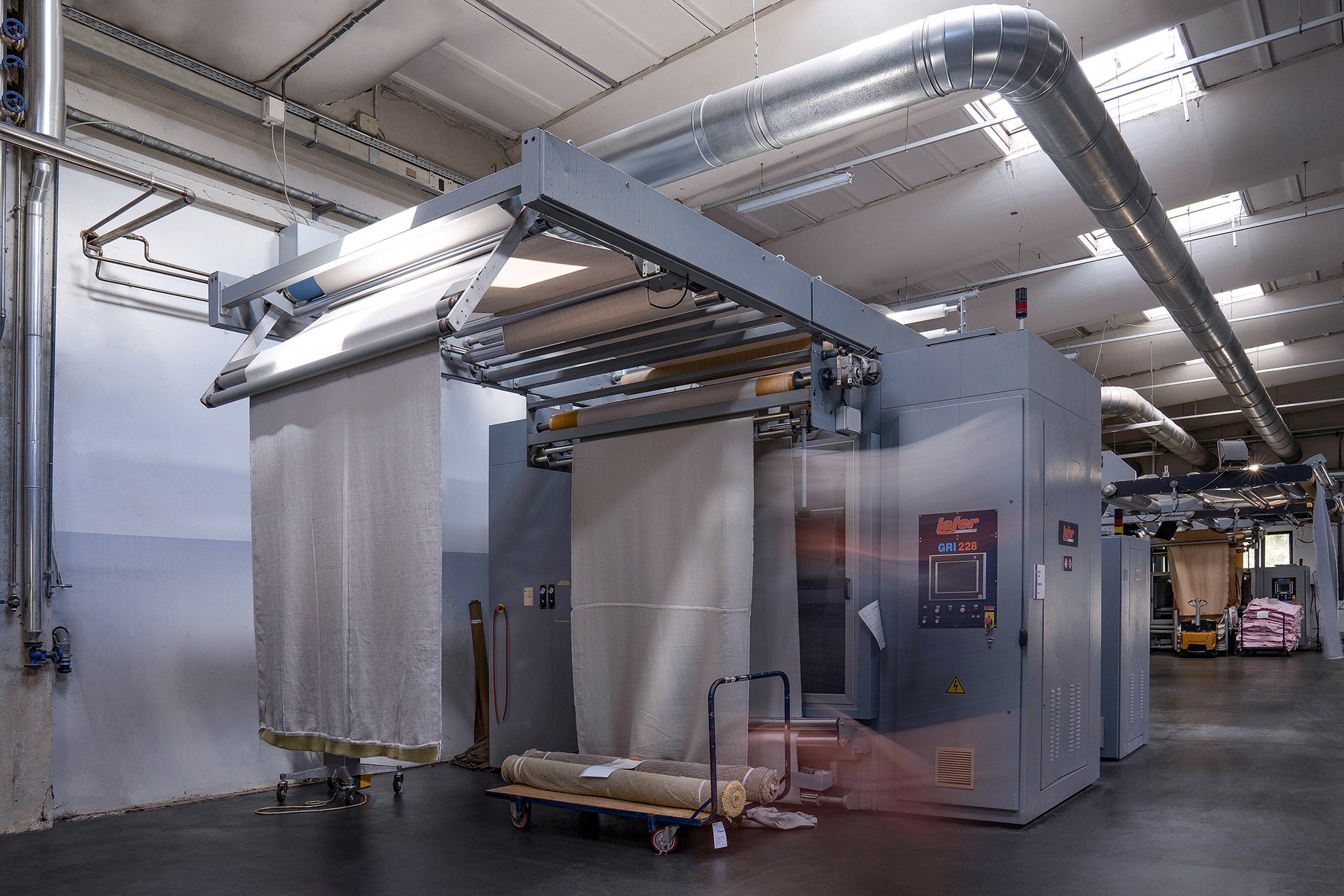
Wet Brushed Woollen
The fabric is wet brushed, namely abraded in one direction to stretch the hair and make it fur-like. The wet brushed treatment helps avoid any risk of breaking the fibre because indeed more elastic.
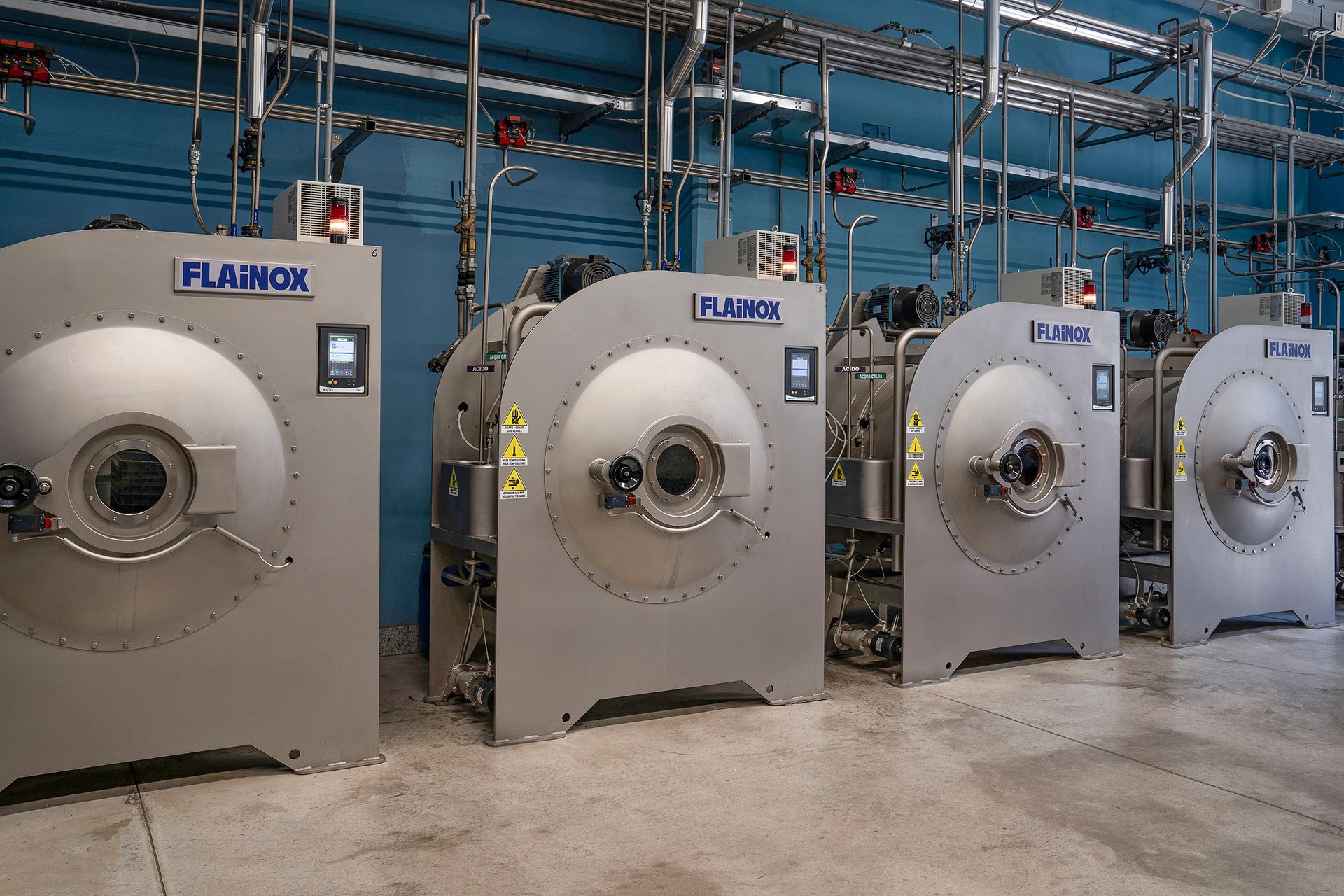
Treatment Tumblers
The fabric is washed and treated in these huge tumblers to make it special, unique and with a type of processing that is artisanal and at the same time truly unique. Enzymes, softeners and stones are used and inserted into the machine along with the fabric to achieve very special effects.
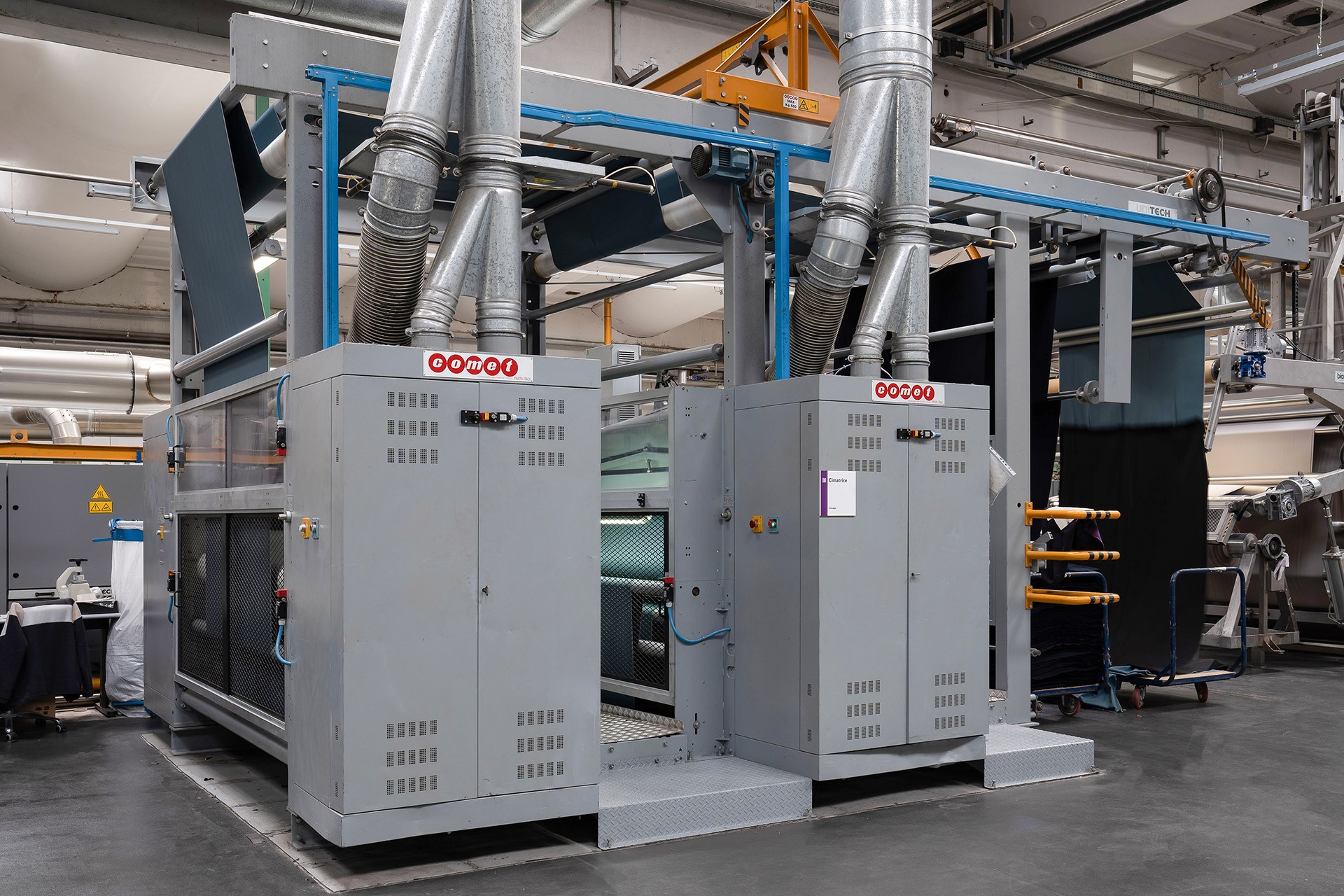
Topping Machine
This machine is comparable to a beard trimmer. In fact, the fabric passes under a very sharp blade that cuts the hair on the surface so as to make the part of the right-side fabric cleaner, shaved and all at the same level.
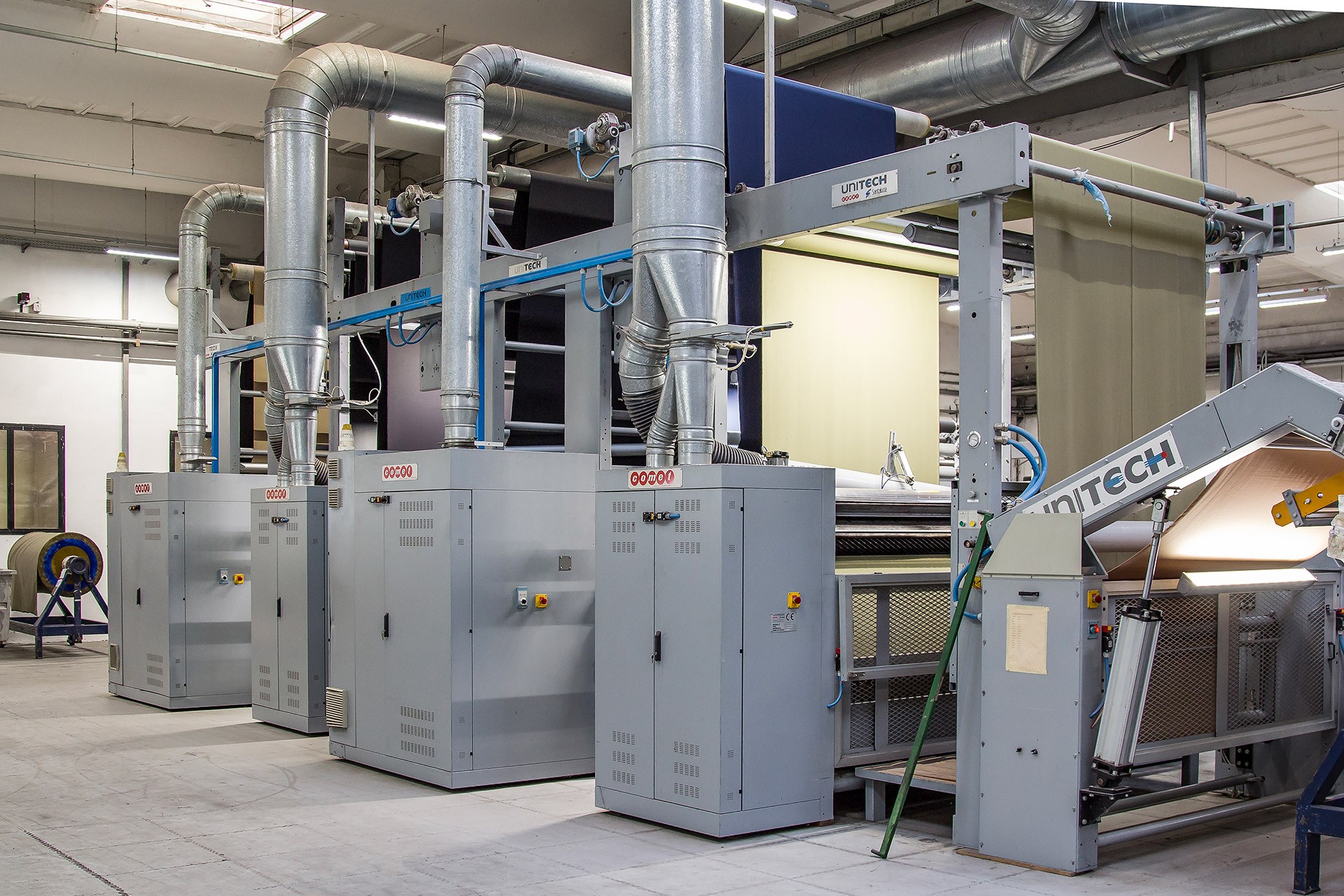
Fabric Shearing Machine
The fabric is brushed with this machine to pull out the hair and make the surface resemble a fur. Depending on the brushed fibres, very different looks can come out.
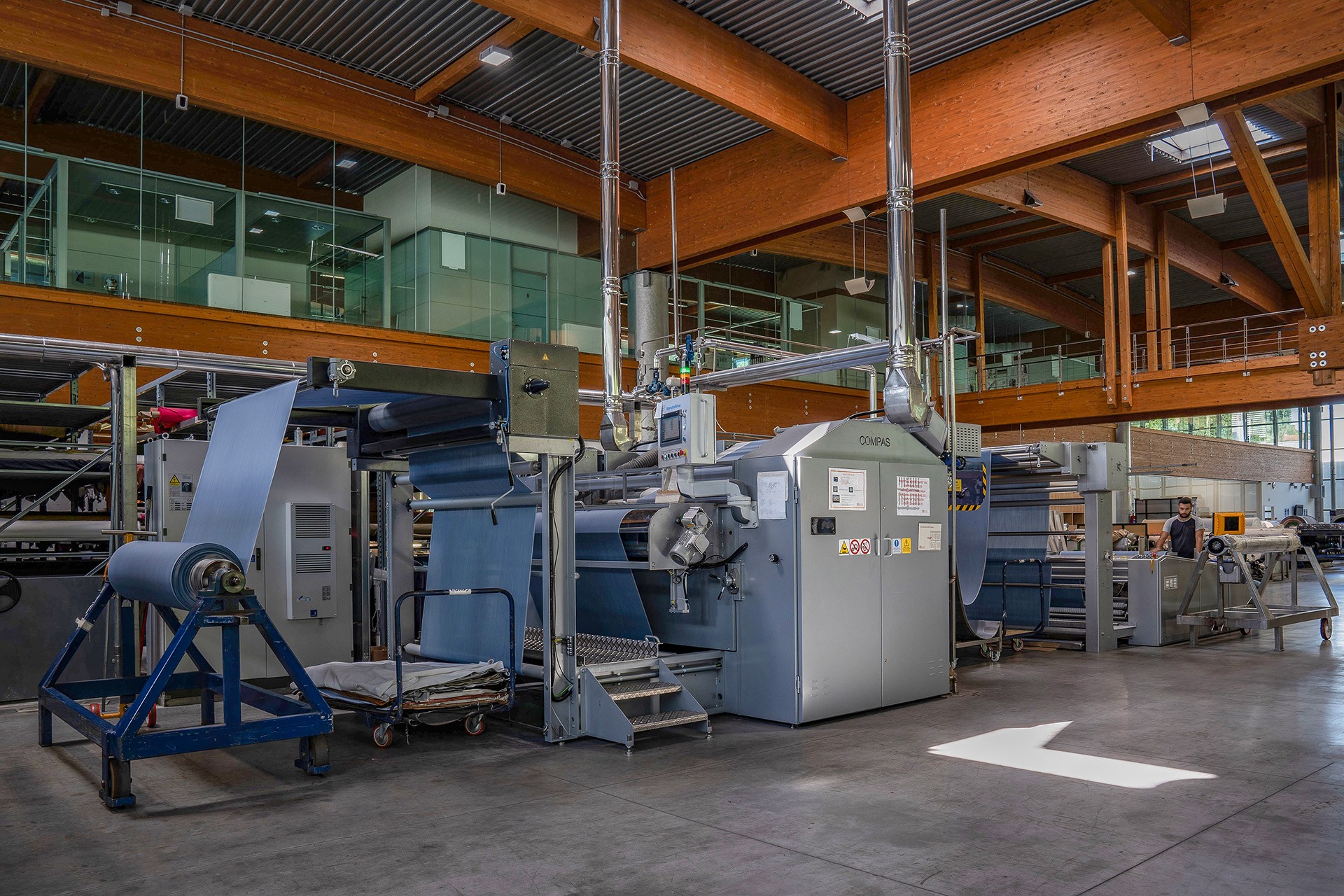
Compactor
This machine is an evolution of the most common Sanfor; here the fabric is forced to compact on itself by means of a rubber cylinder to prevent the fabric from subsequently shorten or stretch in the ironing or washing phases of the garment.
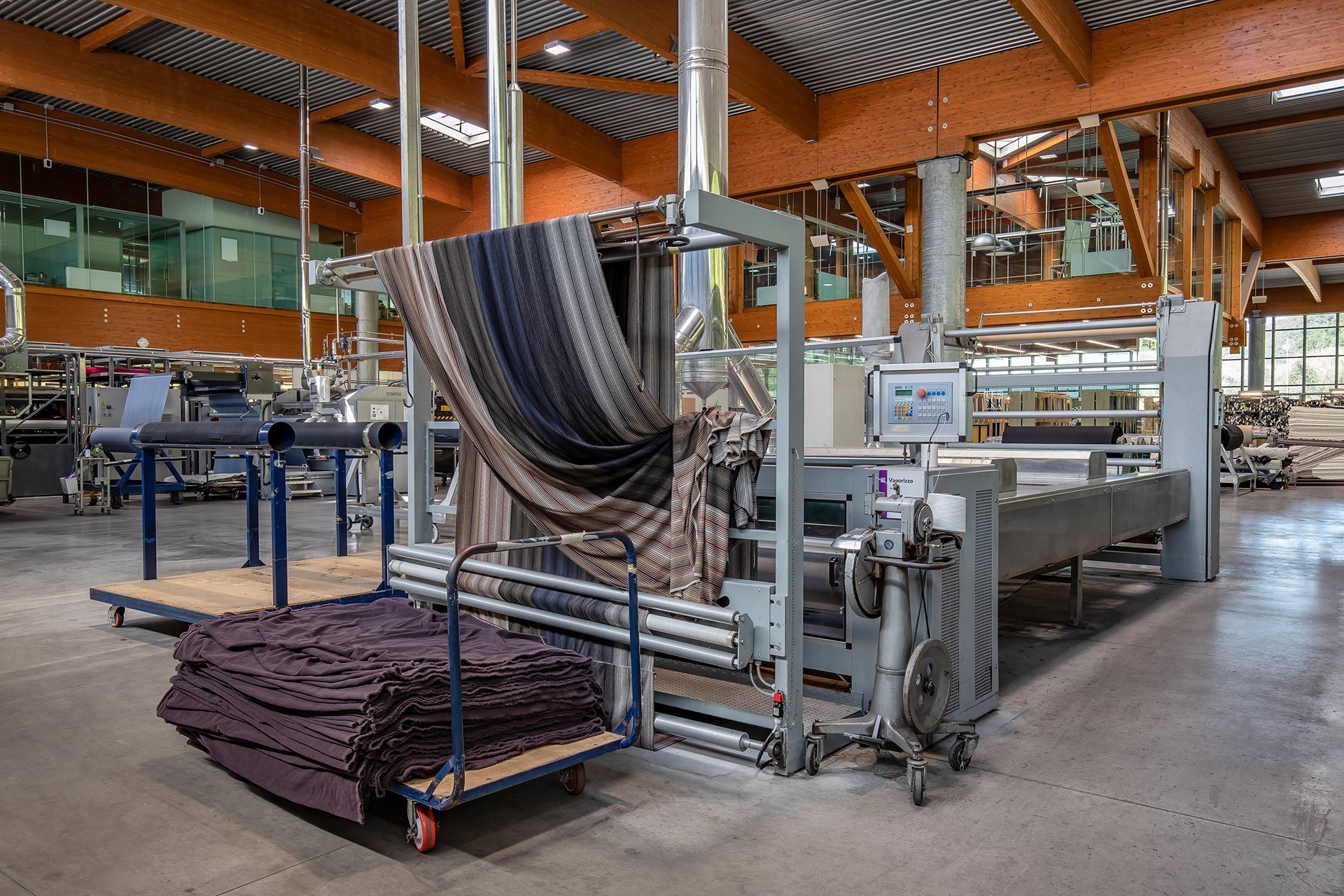
Steaming
The fabric is hit by a huge dose of steam so that it is indented and compacted, preventing shrinkage and defects in subsequent cutting and sewing operations.
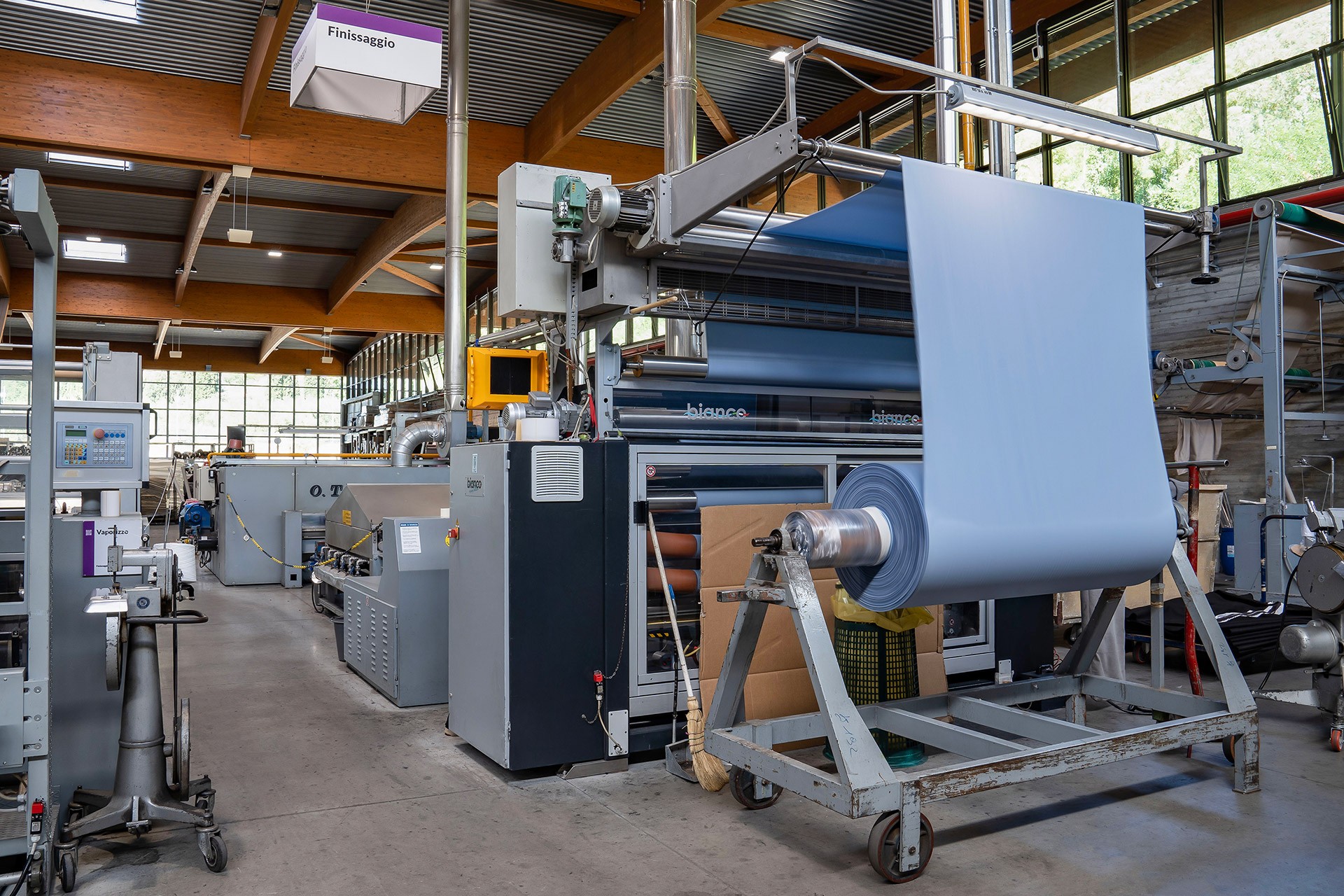
Equalizing
The fabric is rolled with steam and a chain with stabilizing needles and that allows it to be transported without tensions until the classic "piece on tube" is carried out (in which fabrics are commercialized).
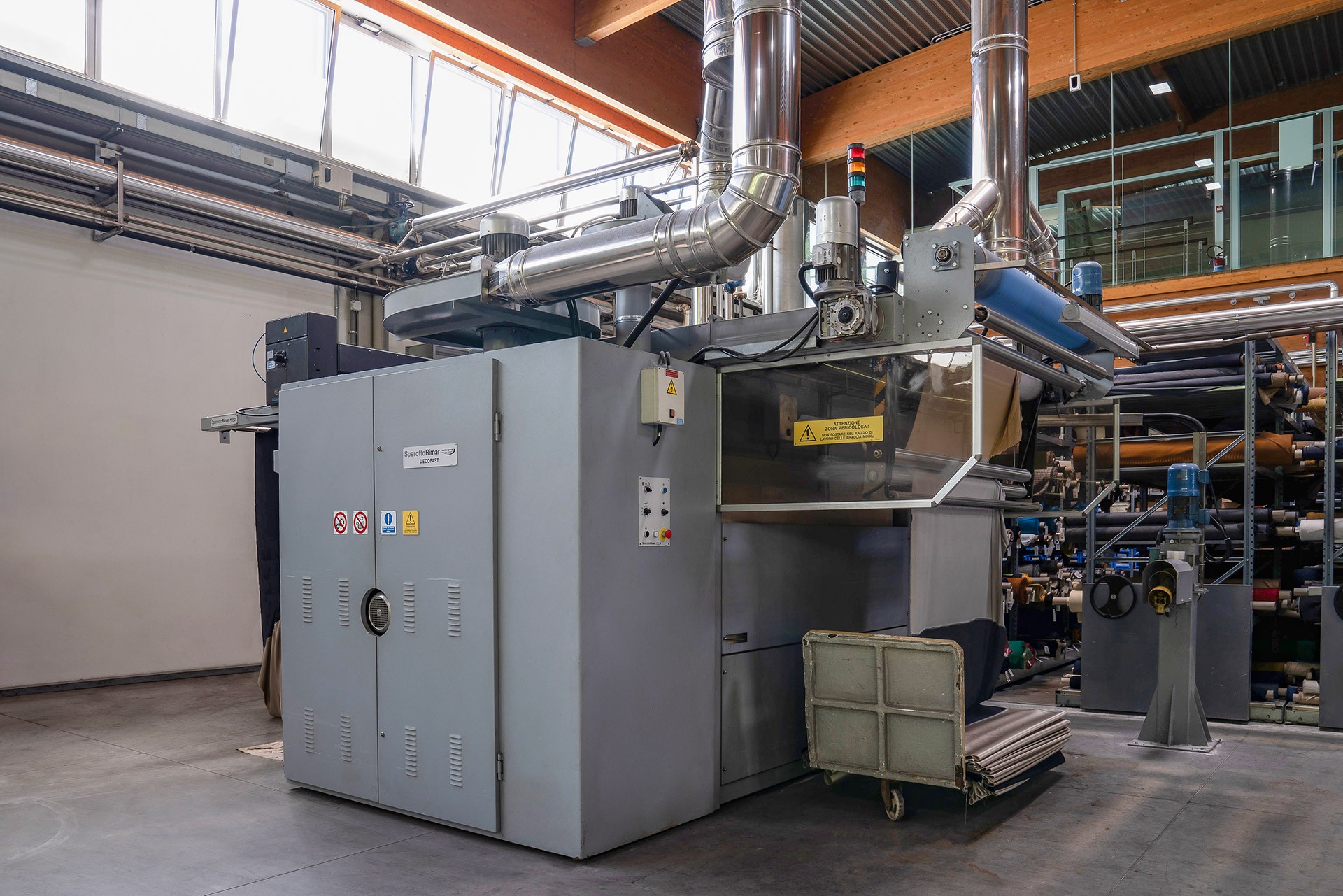
Decofast
With this machine, the fabric is ironed as we normally do with the garment iron.
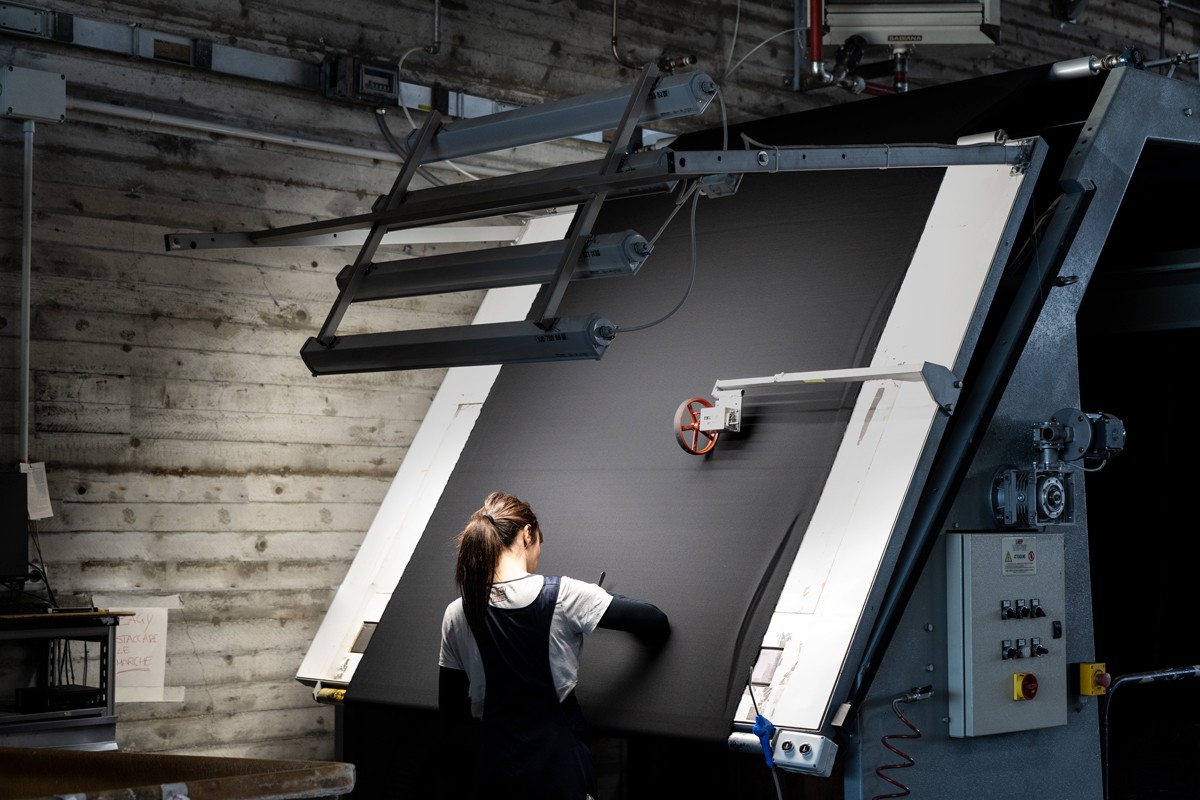
Final Dyed Fabric Check
After the dyeing operation, the fabric is inspected by highly trained personnel who checks uniformity, dye tone and appearance of the fabric before proceeding to the next finishing stage.
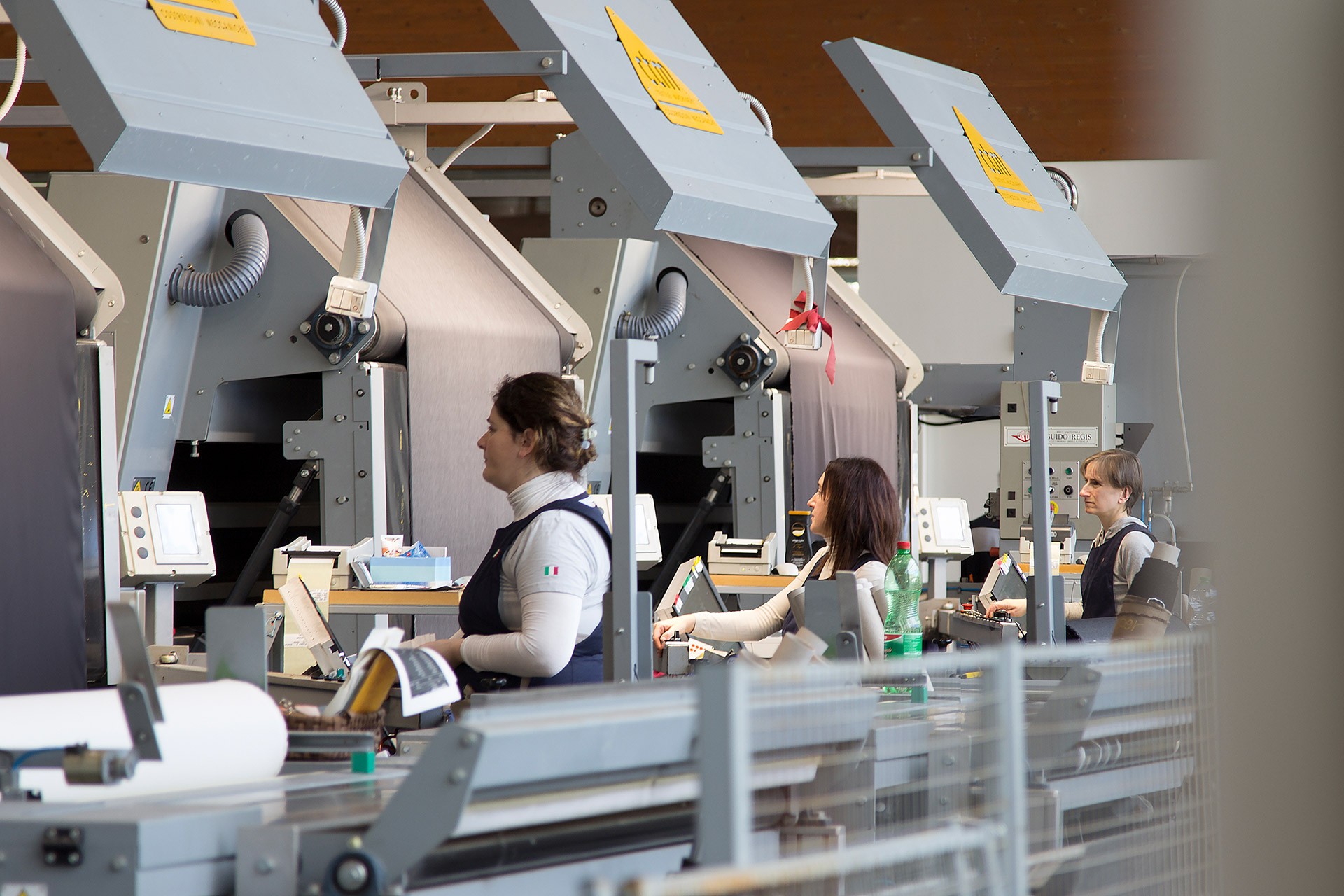
Final Fabric Check
At the end of the production cycle, the fabric is carefully inspected, pointing out one by one all the defects it can present thanks to highly specialized staff who also compiles a report that is sent to the customer where the defects the fabric presents can be seen as on a map.
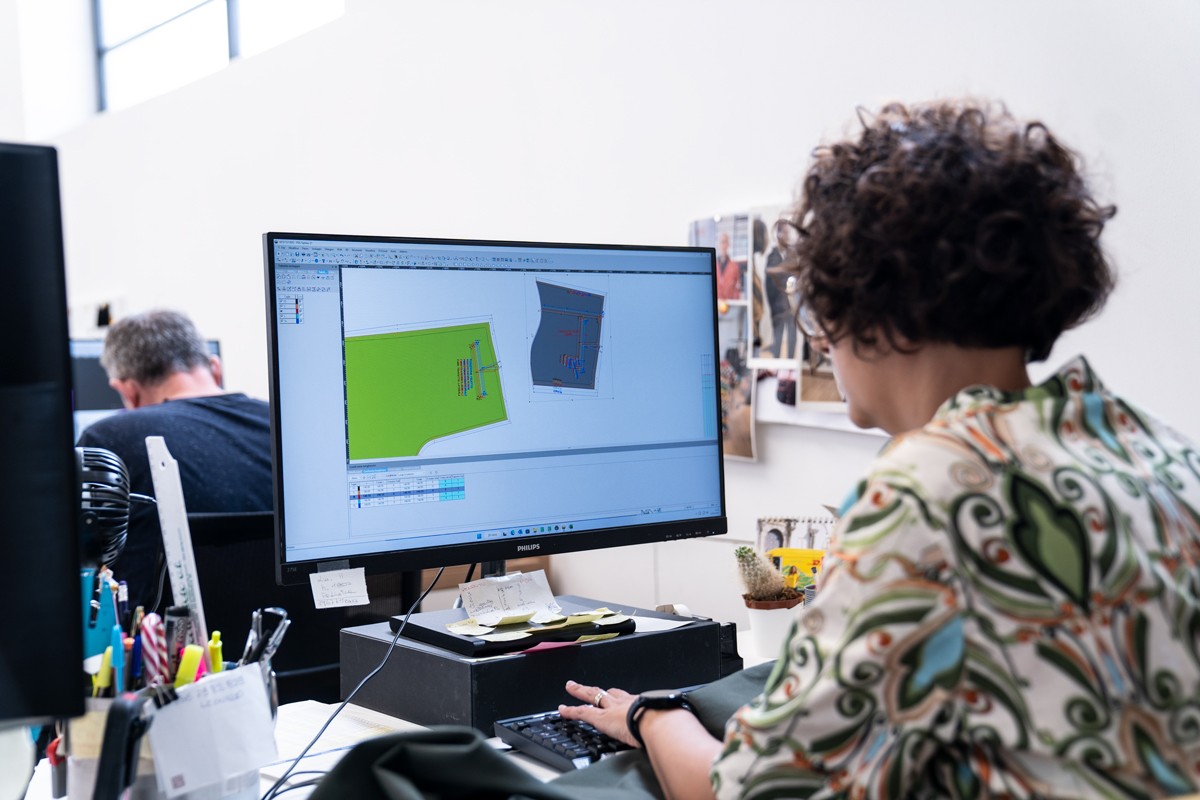
Cad Workstation
Everything occurs on a computer screen, through programs that, in a now very intuitive way, make it possible to manage the two operations that open the production cycle: the development of a pattern according to a given range of sizes (increasing or decreasing from the basic one) and the optimized management of the cutting phase. This is what we improperly mean by post CAD, namely, the activity aimed at minimizing fabric consumption with a software that chooses the best possible fit between the pieces that make up a certain garment.
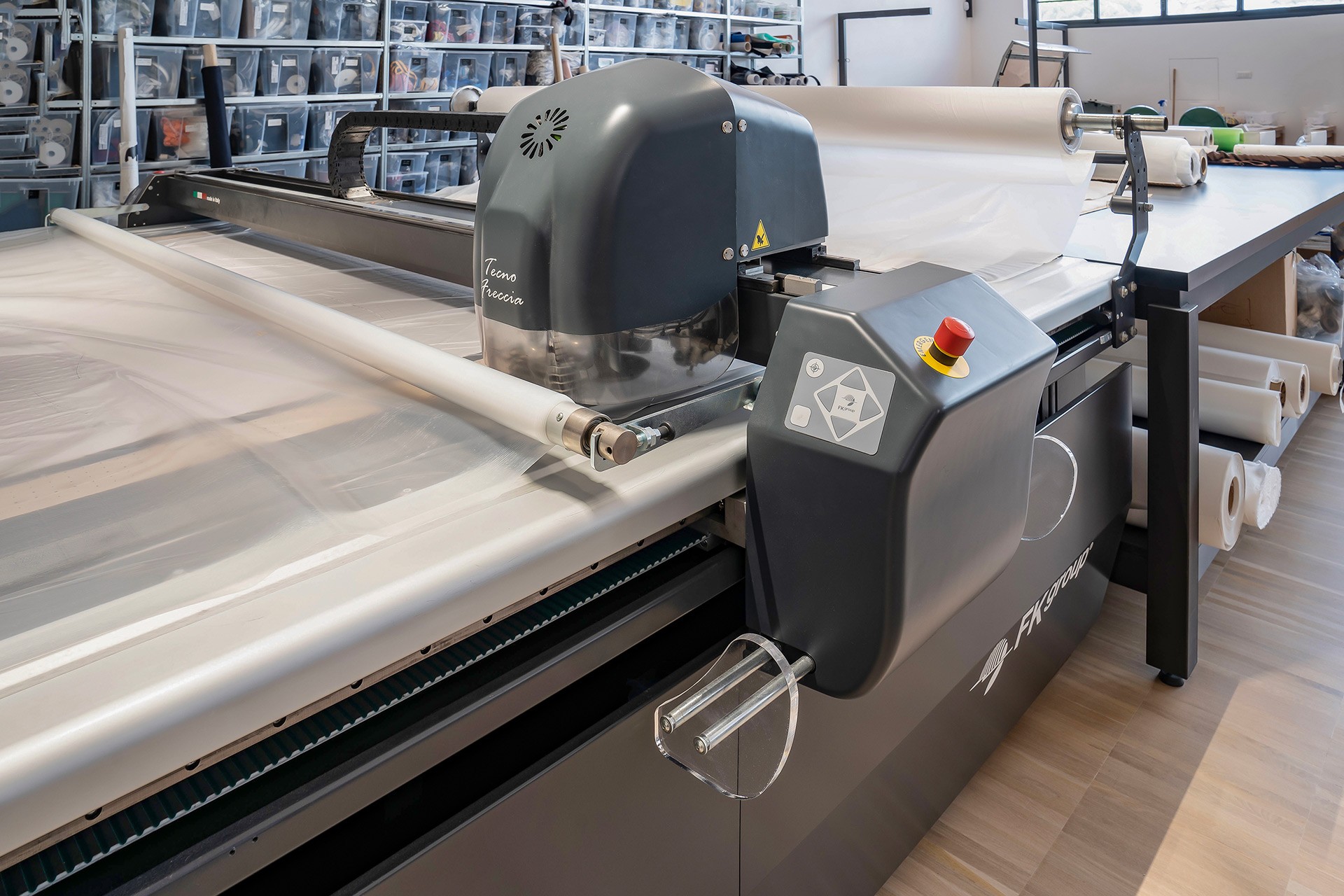
Automatized Cut
Totally electronic cutting method, provided with a circular blade that cuts a textile mattress laying down on vacuum carpet. All the operation is automatic and managed by a computer that moves a working diagram precisely drawn up by a CAD workstation.
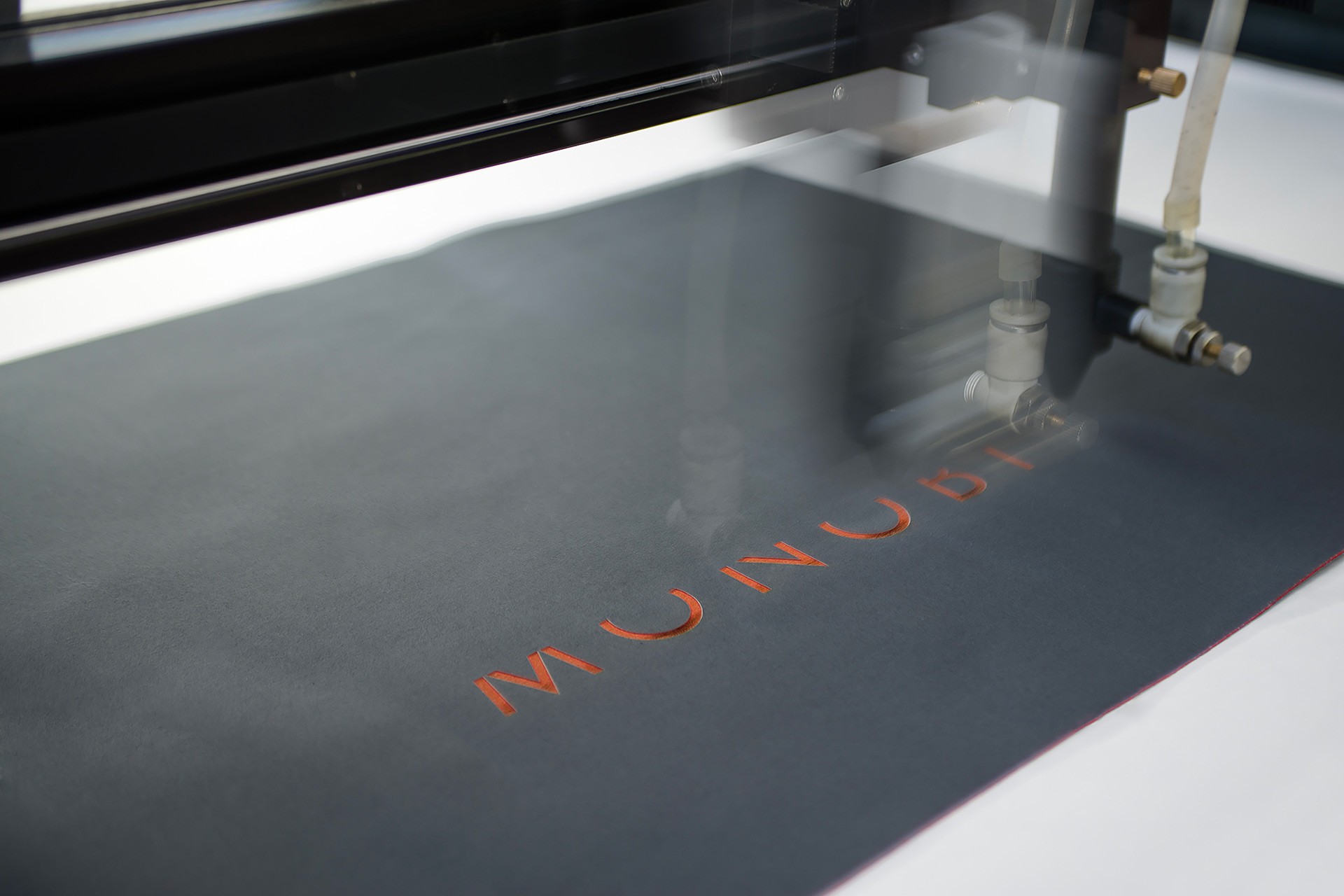
Laser Cut
Focused beam cutting that pushes the precision of operations to the micrometre scale. It can cut or engrave the surface with the same managing easiness of a domestic printer.
Adhesive Machine
Its function is to modulate the consistence and drapery of single fabric pieces. It works according to three different variables, namely time, temperature and pressure. All the components are manually laid down on a conveyor and passed through the grille of the machine.
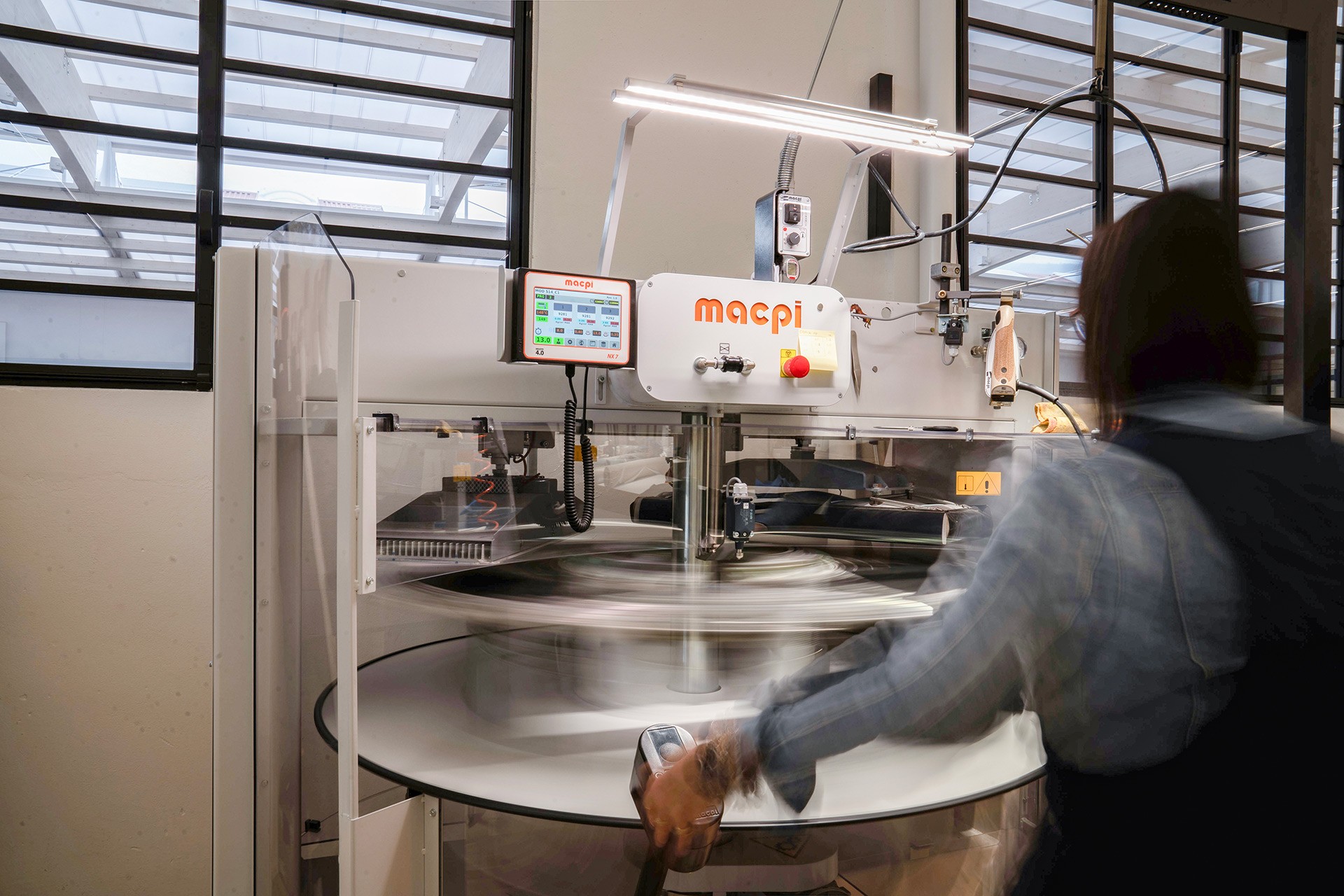
Carousel Press
Fundamental machine to make thermosealed garments. It combines hot press and cold vacuum air to seal the two fabrics together, using films of thermoplastic adhesive. Every single material requires a specific setup, according to the pressure data, temperature and crushing time. This microcomputer allows storing data in order to modify or get it back each time.
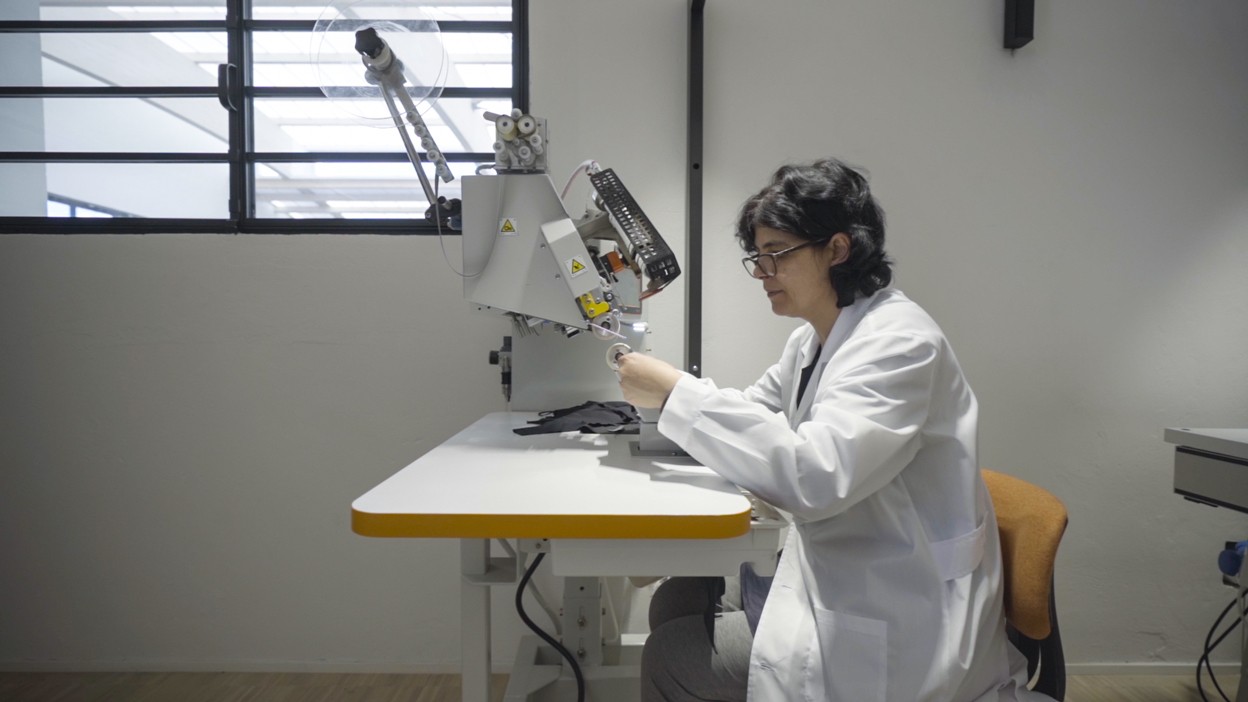
Taping Machine
Its main function is to seal fabrics, namely, apply a tape along the fabrics junctures where the needle holes compromise the integrity and protective capacity of a material. Others more aesthetically oriented are added today to its original function. The process still remains the same: through a hot steam jet and a pair of pressure rollers, the machine applies a tape on cut, sewn, or joined surfaces.
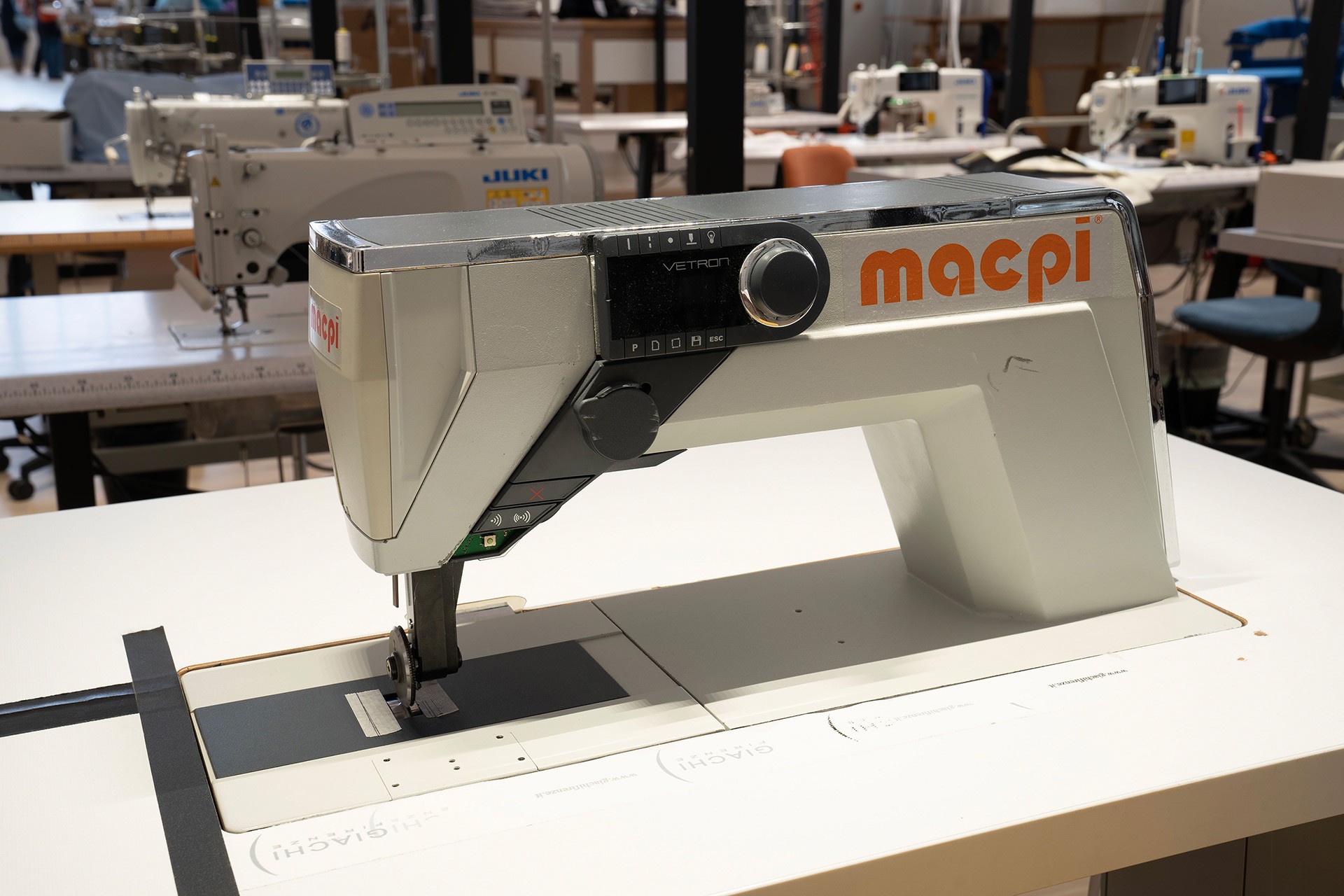
Ultrasonic Sewing Machine
High-technology machine that uses the emission of concentrated ultrasound beam to melt and seal synthetic fibres. It has more or less the same shape as a sewing traditional machine, but it moves without a needle or thread, assembling materials with precision and stability.
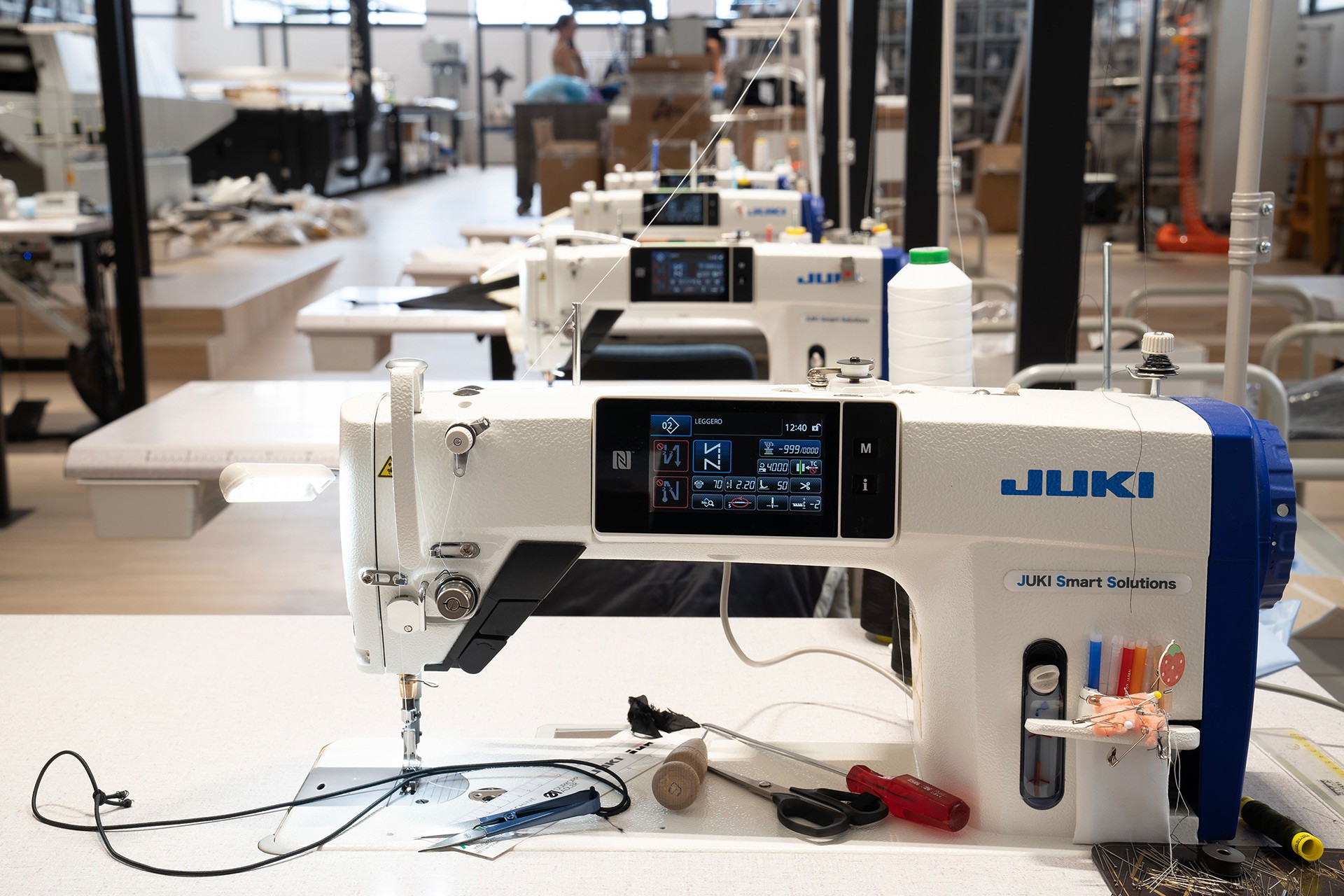
Sewing Machine
A laboratory equipped with sewing machines of the latest generation. Every machine is equipped with a touch screen display that allows managing the machine setting through a series of programs which are regulated according to every fabric weight, their elasticity and the surface resistance. They differ in structure: flat, armed or columned, or for the type of working process they realize. Altogether they present an unparalled creative potential.
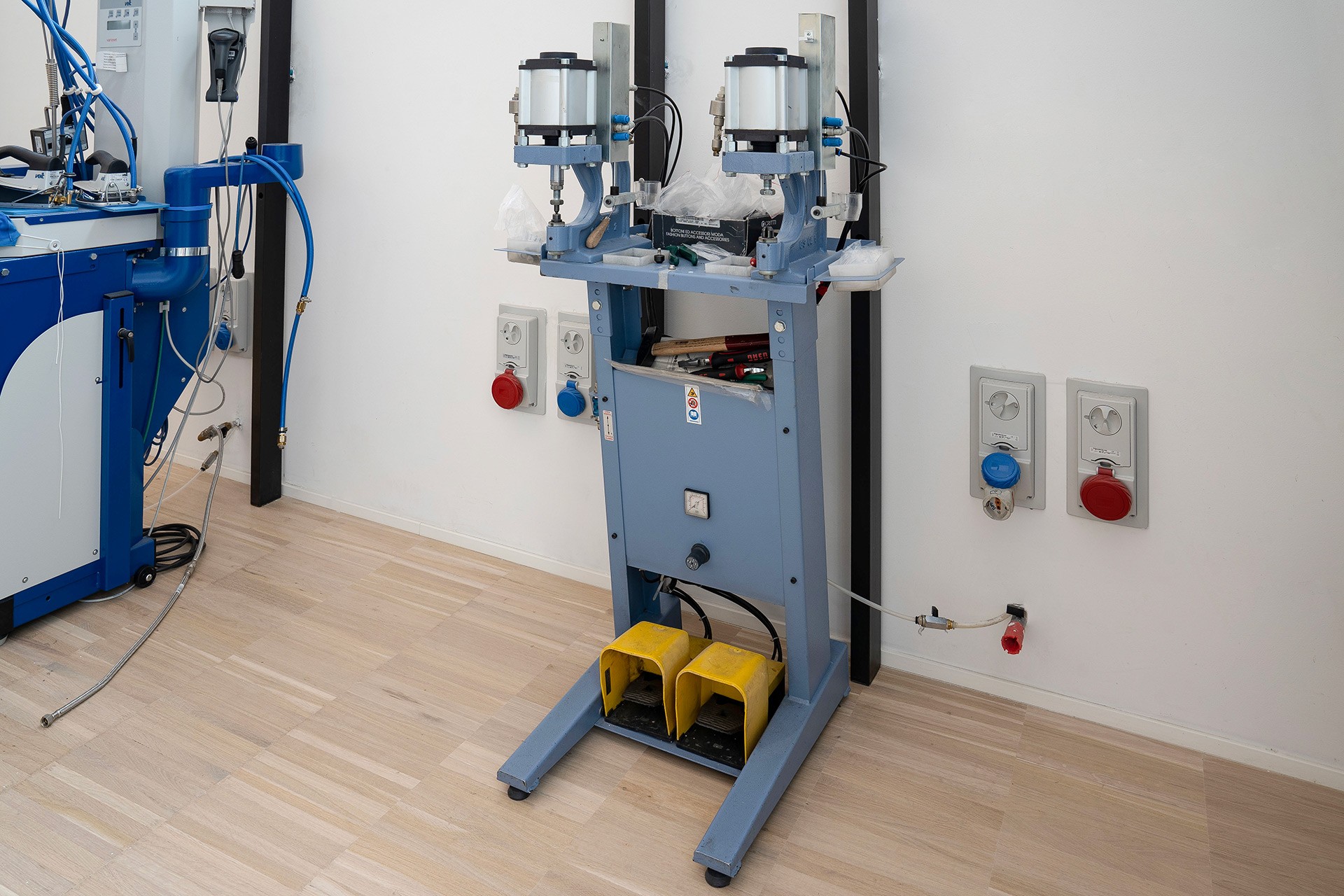
Electronic Button Hanger
Machine electronically controlled that sews every kind of button: with different dimensions, number of internal holes and with varying shank heights.
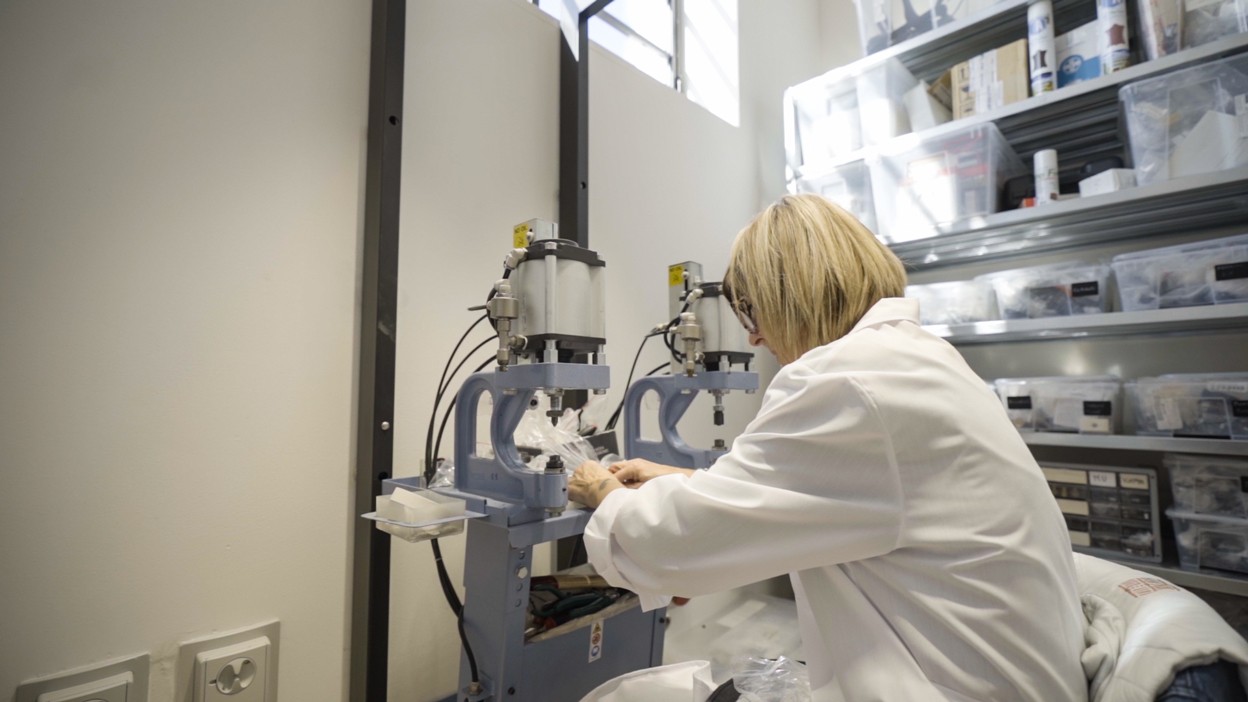
Buttonholer
In the past, not many years ago, these machines were entirely mechanical, engineering masterpieces. However, times have changed and so have machines, but not their function: they manage the embroidery that defines and strengthens the buttonhole. The electric component allows choosing the embroidery shape and dimension quickly, as well as fitting to the fabric type.
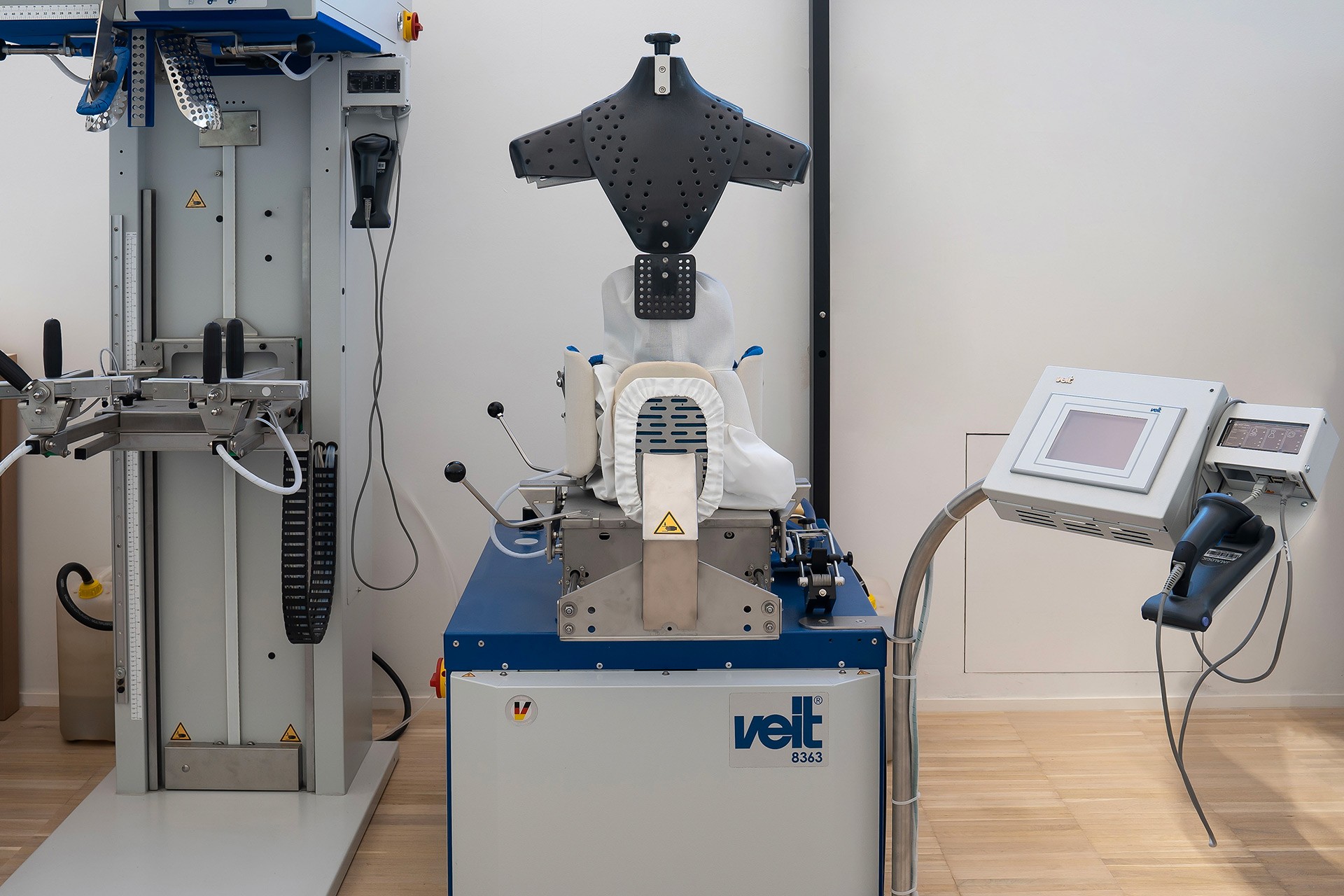
Steam Dummy
Its name derives from the shape of an upper part of the human figure. The garment (jackets and coats) is assembled at the end of every working cycle. Starting from the mid-bust, a jet of glowing steam is released. High pressure and temperature give a real shape to the garment and remove all the working crinkles.
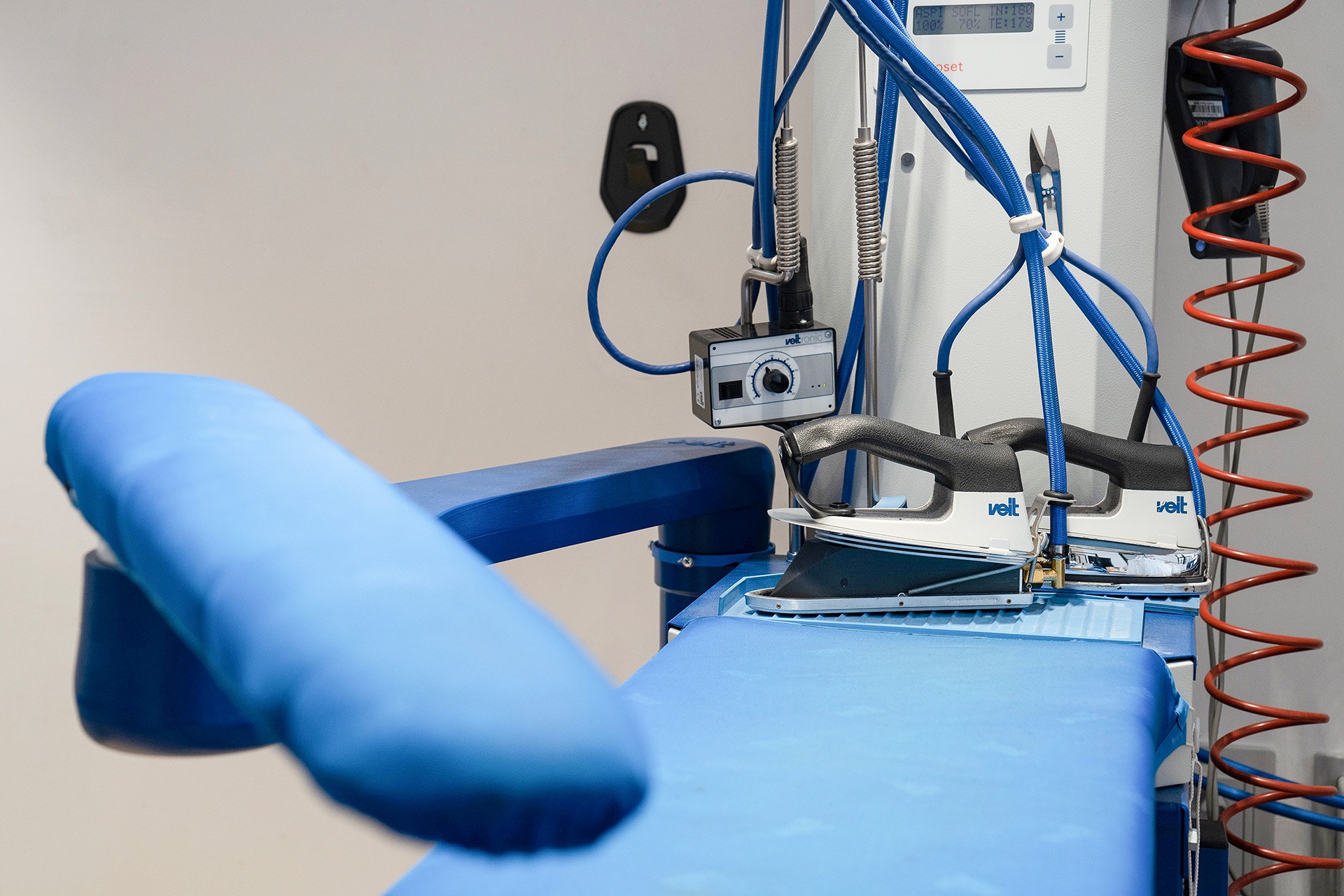
Iron Board
The classic ironing board, similar to the domestic one but differs in performance. Temperatures are higher and a vacuum device allows molding all the materials in the best way possible.
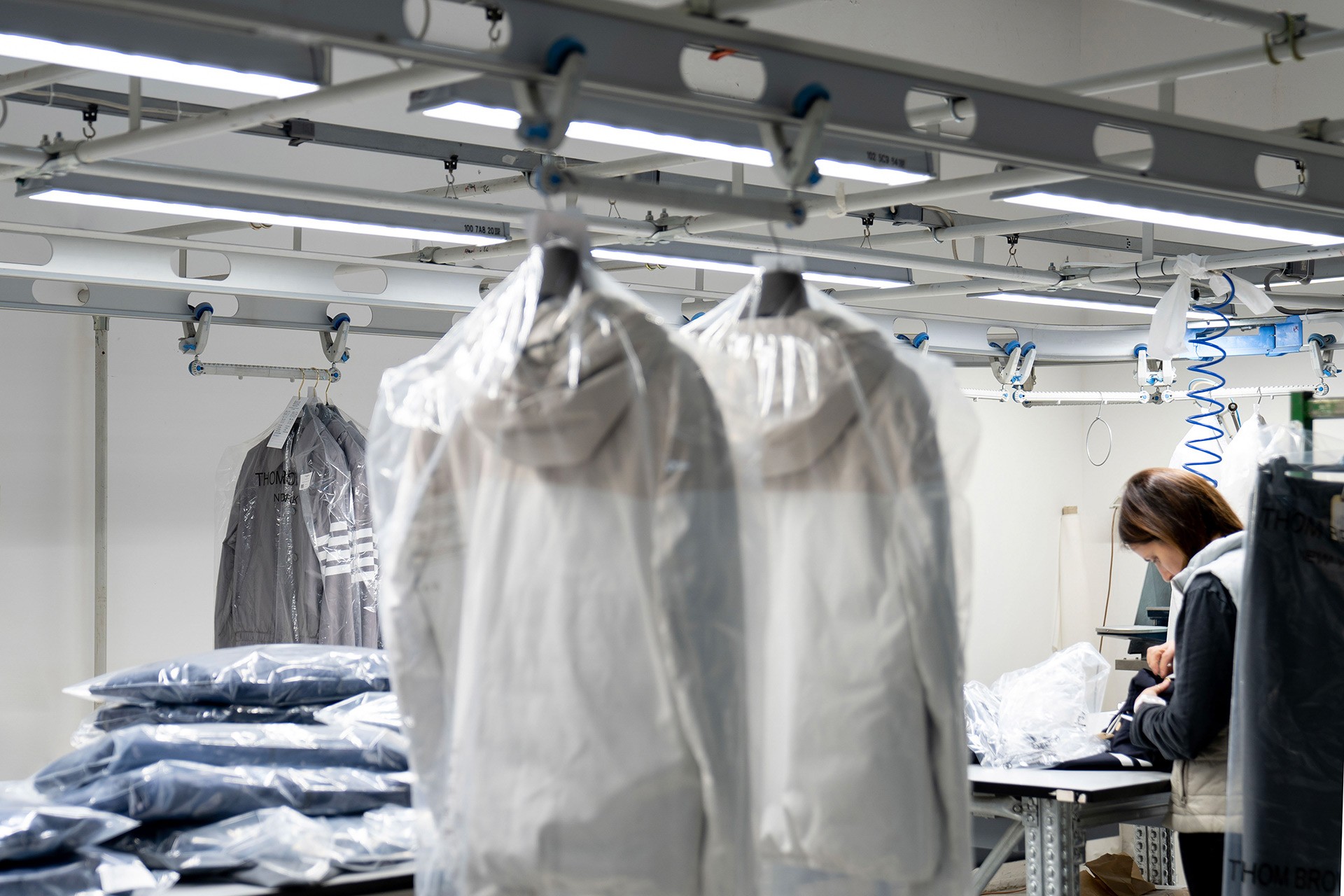
Quality Check Area
This deals with the last “level of judgement”, an area where the single garment quality manufacture and its general correspondence to the guidelines are definitely and accurately evaluated, before entering the warehouse in view of the shipment.
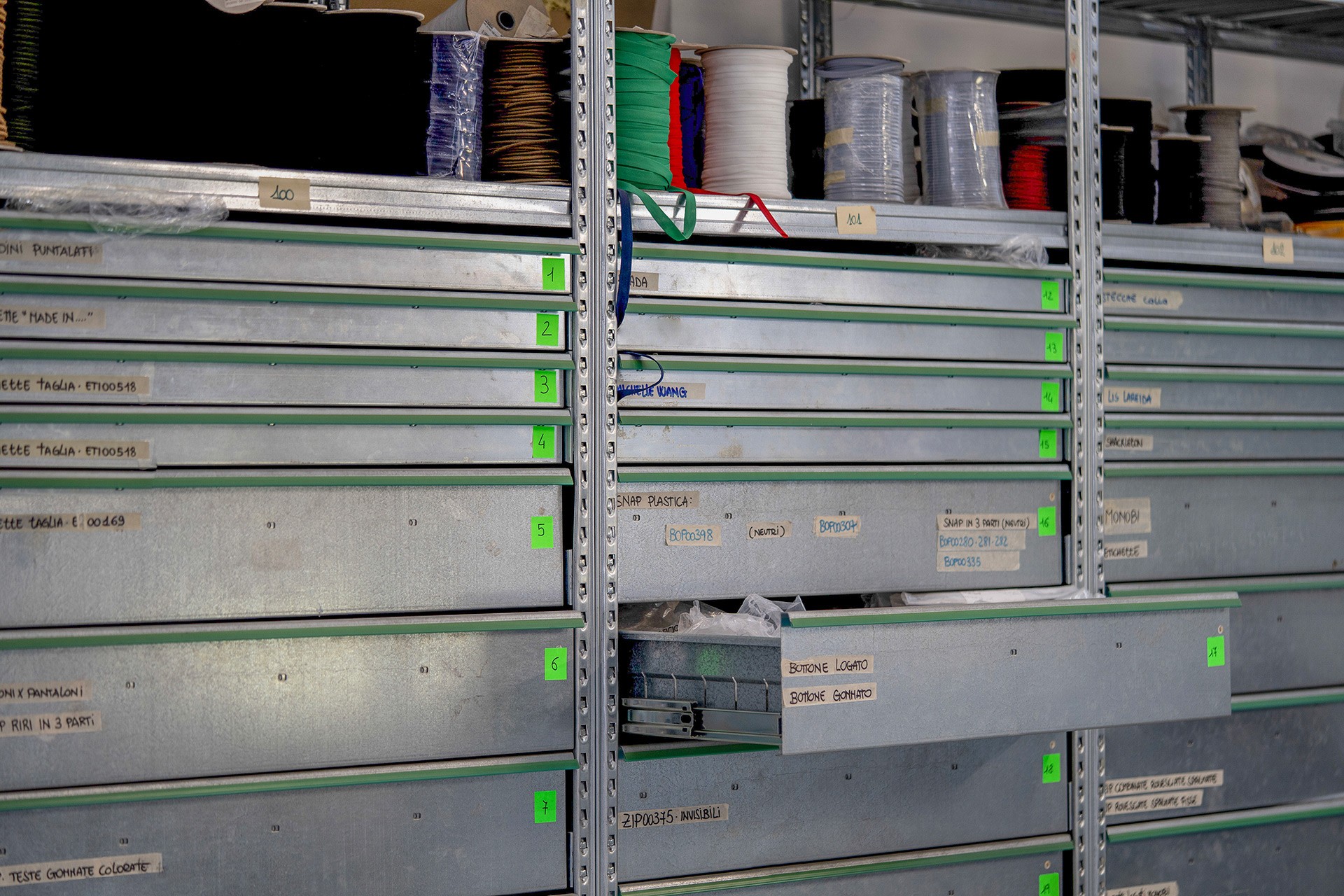
Accessories Warehouse
It consists of a quite wide accessories collection, from the most diverse characteristics and backgrounds. Buttons, snaps, buckles, zippers, ribbons, and everything else is needed to complete and enrich a garment. These are the required ingredients for the “laboratory kitchen”.
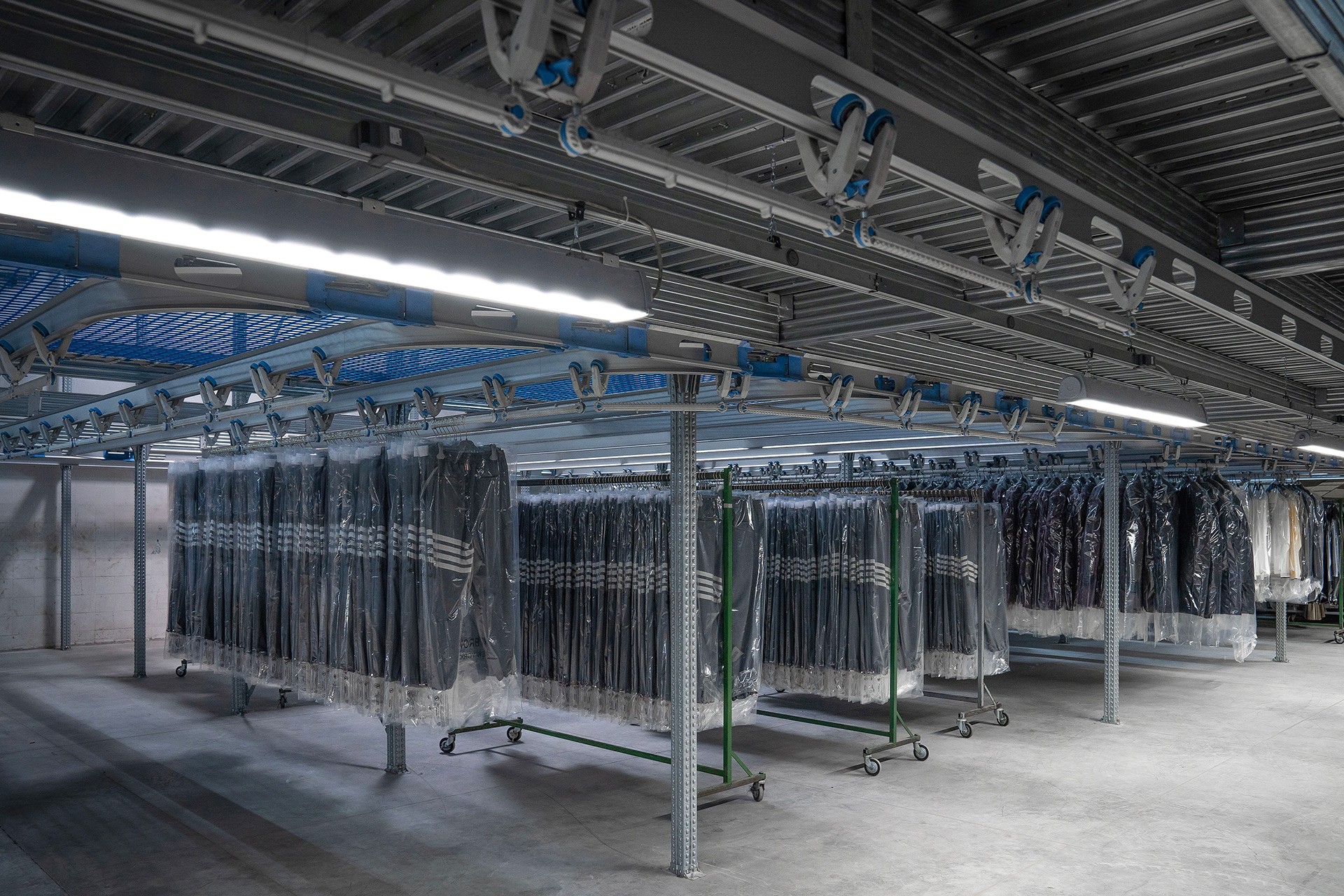
Warehouse for Finished Hanged Garments
Semi-automatic handling warehouse for hanging the finished garments; handling is carried out by "order" or by pattern according to the cases and different necessities, through a computer control.